What is the importance of proper heat treatment in steel crankshaft manufacturing?
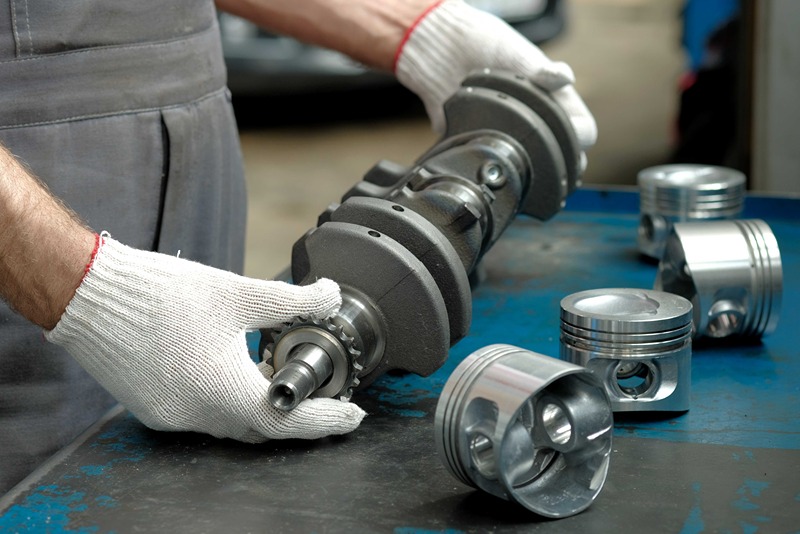
We know how important crankshafts are for car engines. They endure a lot of stress when the engine is running. The materials and methods used to make them depend on the engine type and the specific design of the crankshaft. Using strong materials is crucial to ensure they last a long time. Usually, steel crankshafts are made by shaping them under high pressure (forging), while those made from cast iron are created by pouring molten metal into a mould (casting). Heat treatment is crucial in engineering, especially when applied to a specific section of a crankshaft. While we can check the surface characteristics of the treated journal and potentially achieve the desired condition, we can't be sure about the impact on the inside areas of the crankshaft, and we can't measure it. Exposing the crankshaft to localised heat treatment will result in certain parts undergoing heat treatment with unknown effects. This is because heat can transfer through the material or cause phase changes from ferrite/pearlite to martensite or other desired phases. A steel component's hardening, tempering, or heat treatment involves several steps. These steps alter the material's microstructure and phase changes by exposing the steel to high temperatures, followed by special cooling techniques. Due to its inherent risks, precision and expertise are crucial in executing this process. Advancements in materials
High-strength steels: new steels with tensile strengths up to 950 MPa are becoming more common, and steels with strengths of 1,000 MPa are expected in the future.
New cast steels: a new type of cast steel called grade 5 is used for crankshaft parts. Its strength is like forged steel, making it a better choice for crankshafts, which usually aren't made from cast steel due to minor internal flaws.
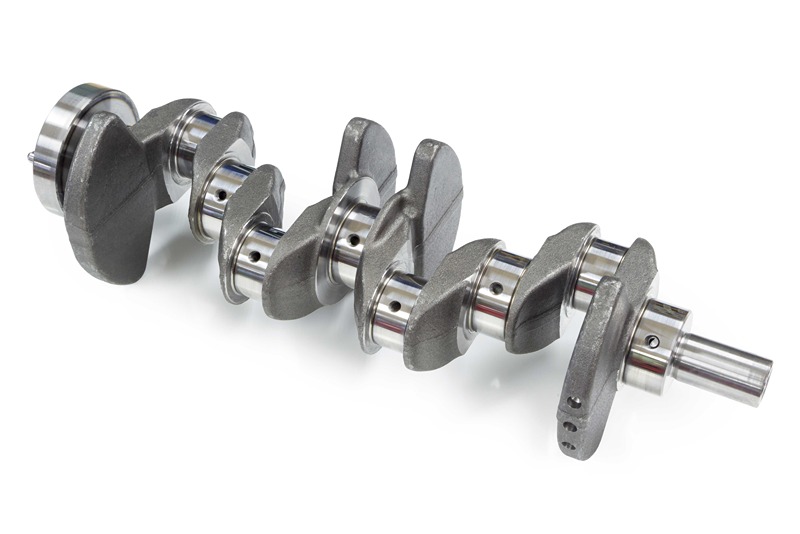
Manufacturing processes
Rotary roll and transverse roll forging: they strengthen crankshafts by placing the toughest layers of steel where the stress is highest.
Cold rolling: this process strengthens crankshaft parts by hardening them and adding compressive stress. It can increase strength by 78%.
Hot rolling: This is used to fix small flaws in cast crankshafts, strengthening key areas like pins and fillets.
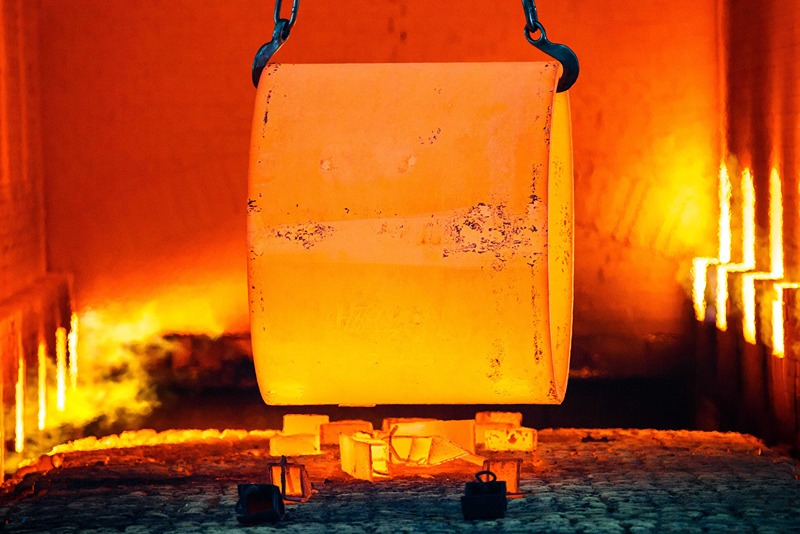
Quality control and testing
Ladle furnace process: this steel-making method effectively removes impurities and gases like sulfur and oxygen, improving the overall quality of the steel.
Ultrasonic inspection: new machines use ultrasound to accurately find and record internal defects, ensuring high-quality steel.
Proper heat treatment is crucial in the manufacturing of steel crankshafts due to several key reasons: 1. Strength and durability Heat treatment processes like quenching and tempering enhance the strength and hardness of steel crankshafts. This is vital for crankshafts as they must withstand high stress and load conditions during engine operation. Proper heat treatment ensures that the crankshaft can endure repeated forces without failing. 2. Fatigue resistance Crankshafts are subjected to cyclic loading, which can lead to fatigue failure. Heat treatment improves the fatigue strength of the steel by refining the grain structure and removing internal stresses. This enhancement in fatigue resistance ensures a longer service life for the crankshaft. 3. Wear resistance Surface treatments like carburising or nitriding or a combination of both increase crankshaft surfaces' wear resistance important for bearing surfaces and journal areas that experience constant friction. A hardened surface reduces wear and extends the crankshaft's lifespan. 4. Toughness While hardness is necessary, toughness (the ability to absorb energy and plastically deform without fracturing) is equally critical. Heat treatment processes are tailored to balance hardness and toughness through proper tempering process, preventing the crankshaft from becoming too brittle and susceptible to fracture under shock loads. 5. Dimensional stability Proper heat treatment ensures the crankshaft's dimensional stability. It minimizes distortions and warping that can occur during machining and operational stresses. This is essential for maintaining the precise tolerances required for proper engine function and reducing vibrations. 6. Corrosion resistance Although not the primary function of heat treatment, specific processes can enhance the corrosion resistance of steel crankshafts. For example, nitriding can provide a thin, hard, corrosion-resistant layer on the surface, contributing to the crankshaft's overall durability in harsh environments. 7. Stress relief Heat treatment helps relieve residual stresses introduced during the forging and machining processes. If not properly managed, these residual stresses can lead to cracking or warping during the crankshaft’s operation. 8. Consistent performance Uniform heat treatment ensures consistent mechanical properties throughout the crankshaft. This consistency is crucial for the engine's balanced and reliable performance, avoiding weak points that could lead to premature failure.
Buy online
Mild SteelStainless SteelStructural SteelTMTCementJSW One MSME
About usBlogsSitemapJSW One TMTPolicy
Terms & conditionsPrivacy policyReturn policy