What are the factors that contribute to the quality of steel?
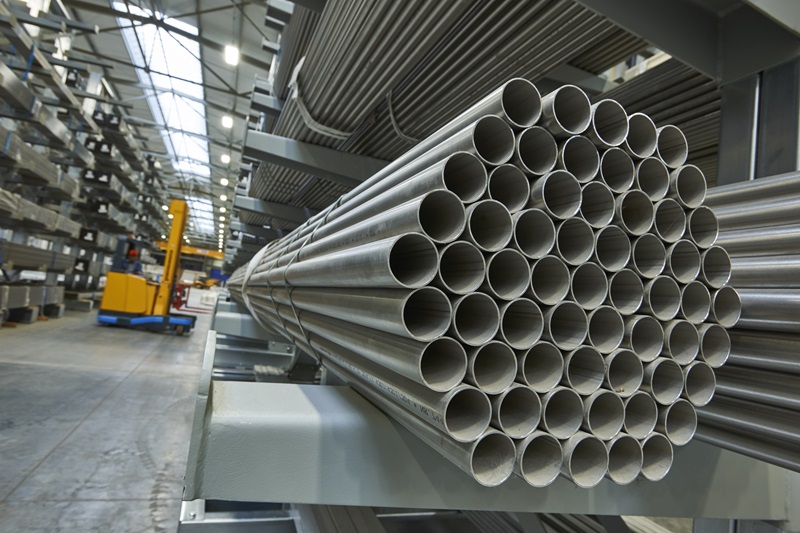
Steel is a durable material used in various industries, including construction, automotive, and manufacturing. When you buy steel online, the importance of quality steel for these industries cannot be overstated. High-quality steel is essential for ensuring structures and products' safety, longevity, and sustainability. JSW steel products are strong, lightweight, and easy to work with, making it ideal for various applications. Additionally, steel is a sustainable material that can be recycled and reused, reducing waste and protecting the environment.
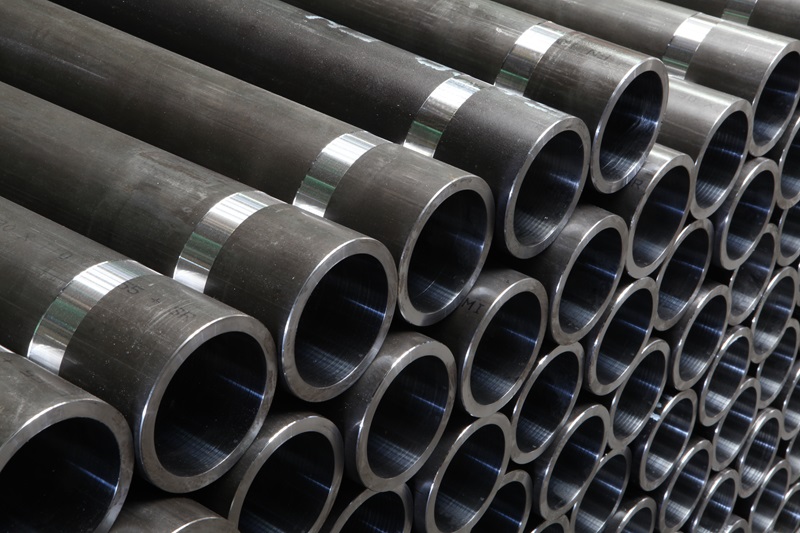
Elemental components of steel and their impact on properties: Iron Primary component: Steel primarily comprises iron, providing its structural foundation. Contribution to properties: Iron serves as the base for the alloy, offering a strong and sturdy framework. Carbon: Key modifier: Carbon content significantly impacts steel properties like. Strength: Higher carbon content increases hardness and strength but reduces ductility. Durability: Carbon influences wear resistance and hardness. Flexibility: Lower carbon content results in increased flexibility and weldability.
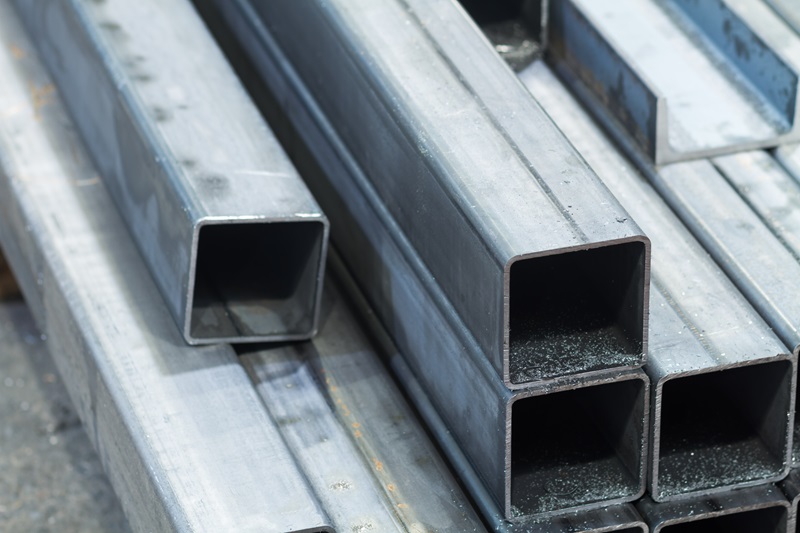
Impact of different compositions on steel properties: Strength: Higher carbon content or adding certain alloying elements like chromium and nickel can significantly enhance strength. Balancing alloying elements allows for tailored strength properties suitable for various applications. Durability: Carbon content affects hardness and wear resistance while alloying elements like manganese and silicon are durable against impacts and deformation. Flexibility: Lower carbon content promotes greater flexibility and ease of shaping. Alloying elements can enhance specific characteristics without compromising flexibility. Influence of manufacturing techniques on steel quality: 1. Process consistency: Quality control: JSW steel products have rigorous quality checks at every production stage, maintaining consistency and adherence to specified standards. Homogeneity: Advanced methods help achieve a more uniform composition and microstructure, reducing impurities and enhancing steel quality. 2. Cleanliness and purity: Removal of impurities: Techniques like refining and degassing remove impurities, resulting in cleaner steel with improved mechanical properties. Reduced inclusions: Innovative processes minimise non-metallic inclusions, enhancing steel's toughness and fracture resistance.
3. Microstructure control: Grain size and orientation: Precise control over the cooling and solidification process influences the microstructure, affecting properties like strength, toughness, and ductility. Phase transformations: Heat treatment methods and controlled cooling rates help achieve desired phases, influencing steel hardness and resilience. 4. Alloying and treatment: Alloy addition precision: Advanced manufacturing allows for precise control over the addition of alloying elements, tailoring steel properties for specific applications. Heat treatment precision: Techniques ensure accurate heating and cooling cycles, optimising steel properties without compromising structural integrity. 5. Energy efficiency and environmental impact: Efficient processes: Modern methods emphasise energy-efficient technologies, reducing the environmental footprint of steel production. Sustainability: Some techniques prioritise sustainable practices, including recycling scrap steel and reducing waste in the manufacturing process. Importance of quality checks during steel production: Quality control is paramount to guarantee consistent and reliable steel products. Applying stringent checks at various manufacturing stages ensures adherence to standards and the delivery of high-quality steel. Raw material inspection: Chemical composition analysis: Raw materials undergo examination before processing to verify their composition and purity, ensuring they meet the required specifications. Visual and physical inspection: Visual assessments and physical tests are conducted to identify any impurities or irregularities that could impact the final steel quality.
Process monitoring: Continuous monitoring: throughout manufacturing, processes are monitored in real-time to maintain consistent temperatures, pressures, and other parameters crucial for quality steel production. Sampling and testing: regular sampling and testing during various stages of processing help identify deviations from desired specifications. Technologies and methodologies for quality assurance: Non-destructive testing (NDT): Ultrasonic testing: Using sound waves to detect internal flaws or inconsistencies in steel ensures structural integrity. Magnetic particle inspection: Reveals surface and near-surface defects by applying magnetic fields to steel components. Radiographic testing: Uses x-rays or gamma rays to examine internal structures for defects without damaging the steel. Spectroscopy: Chemical analysis: Techniques like Optical Emission Spectroscopy (OES) and x-ray fluorescence (XRF) provide rapid and accurate chemical composition analysis of steel samples. Elemental identification: helps verify the presence of specific elements within the steel, ensuring it meets required alloy compositions. Mechanical testing: Tensile testing: measures the strength and elasticity of steel by subjecting samples to controlled tension, ensuring they meet specified standards. Hardness testing: Determines the steel's resistance to indentation or penetration, ensuring it falls within acceptable ranges. Role of alloying elements: Chromium (Cr): Enhancing corrosion resistance: Adding chromium forms a protective oxide layer on the steel surface, improving resistance to corrosion and oxidation. Increasing hardness: Chromium contributes to hardness and wear resistance, which is vital in applications requiring durable and corrosion-resistant steel, like stainless steel. Nickel (Ni): Improving toughness and ductility: nickel enhances toughness, making steel resilient against impacts while maintaining ductility. Corrosion resistance: nickel alloys exhibit excellent resistance to corrosion in harsh environments, such as marine applications. Manganese (Mn): Strengthening and hardenability: Manganese enhances hardenability and tensile strength, increasing strength and wear resistance.
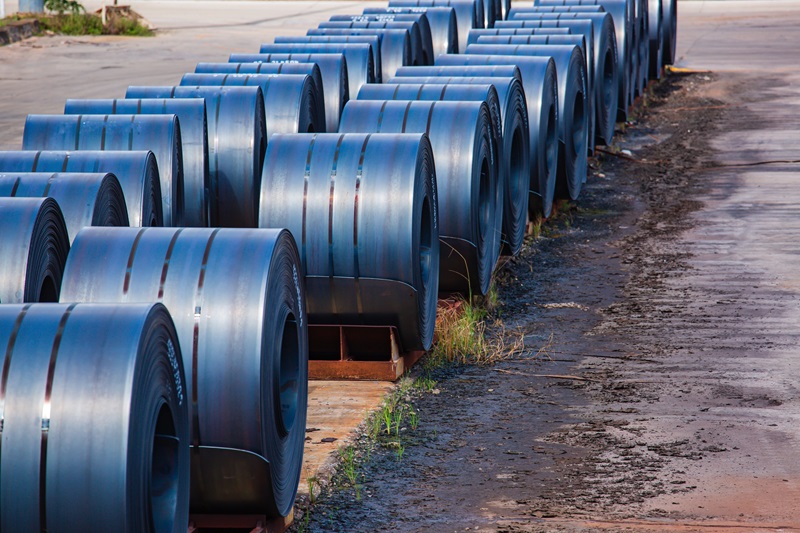
Deoxidation and grain refinement: manganese aids in deoxidising steel and refining grain structures, which is crucial for better mechanical properties. Other alloying elements (e.g., vanadium, titanium, etc.): Fine-tuning properties: Elements like vanadium and titanium are used in small quantities to refine grain structures, improve strength, and enhance heat resistance in specialised steel grades. Enhancement of specific properties: Corrosion resistance: Chromium and nickel: These elements form corrosion-resistant compounds, creating stainless steel grades that resist rust and degradation in various environments. Hardness and wear resistance: Chromium, manganese, and nickel: Combined or individually, these elements increase hardness and wear resistance, which is crucial in manufacturing tools, machinery parts, and components subjected to abrasive conditions. Toughness and ductility: Nickel and manganese: These elements contribute to improved toughness without sacrificing ductility, which is vital in structural components and machinery requiring strength and resilience. By carefully incorporating chromium, nickel, manganese, and other elements in precise quantities, steelmakers create alloys with enhanced properties such as corrosion resistance, hardness, toughness, and ductility. This flexibility allows for the production of specialised steel grades optimised for various applications, ensuring that the manufactured steel meets diverse industrial requirements.
Buy online
Mild SteelStainless SteelStructural SteelTMTCementJSW One MSME
About usBlogsSitemapJSW One TMTPolicy
Terms & conditionsPrivacy policyReturn policy