What are the chemical properties of different types of cement and how do they affect construction?
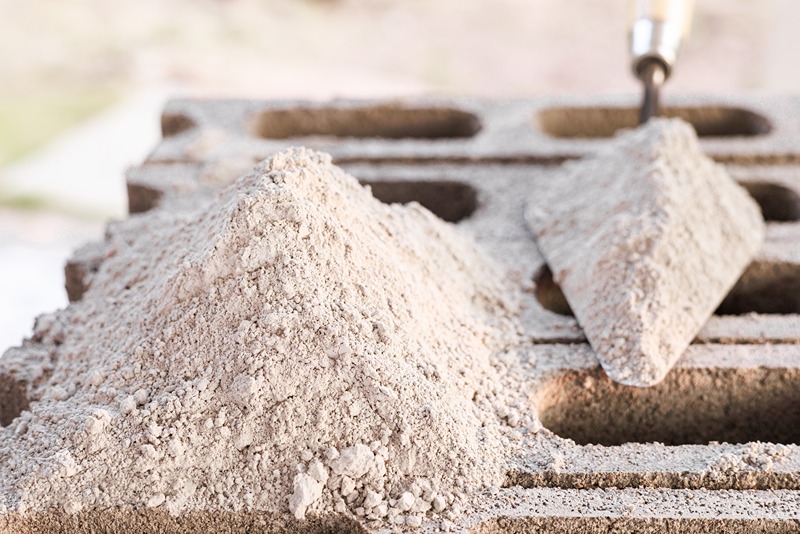
Cement is a crucial material in construction, used to bind various elements together in concrete and mortar. Although different types of cement share common components, their chemical properties can vary, which affects how they perform in different construction environments. Understanding these chemical properties is important for choosing the right type of cement for specific construction projects. Let’s explore the chemical properties of common types of cement and how they influence construction. 1. Ordinary Portland Cement (OPC) Chemical composition:
Calcium oxide (CaO): 60-67%
Silicon dioxide (SiO₂): 17-25%
Aluminium oxide (Al₂O₃): 3-8%
Iron oxide (Fe₂O₃): 0.5-6%
Magnesium oxide (MgO): 0.1-4%
Sulphur trioxide (SO₃): 1-3%
Effect on construction:
Strength: OPC provides high initial strength, making it ideal for fast-paced construction projects like roads and bridges.
Setting time: due to its high calcium oxide content, OPC sets and hardens quickly, though it may be prone to cracking due to rapid hydration.
Versatility: OPC is widely used in various construction projects, from residential to commercial buildings.
2. Portland Pozzolana Cement (PPC) Chemical composition: Contains the same base components as OPC, with added pozzolanic materials like fly ash, volcanic ash, or silica fumes (15-35%). Effect on construction:
Durability: the pozzolanic materials react with calcium hydroxide, improving durability and making PPC more resistant to chemical attacks. This is useful in structures exposed to water or chemicals, like dams or marine structures.
Workability: PPC has finer particles, improving workability, which is advantageous in plastering or finishing works.
Lower heat of hydration: PPC generates less heat during curing, reducing the risk of cracks in large concrete structures such as dams and bridges.
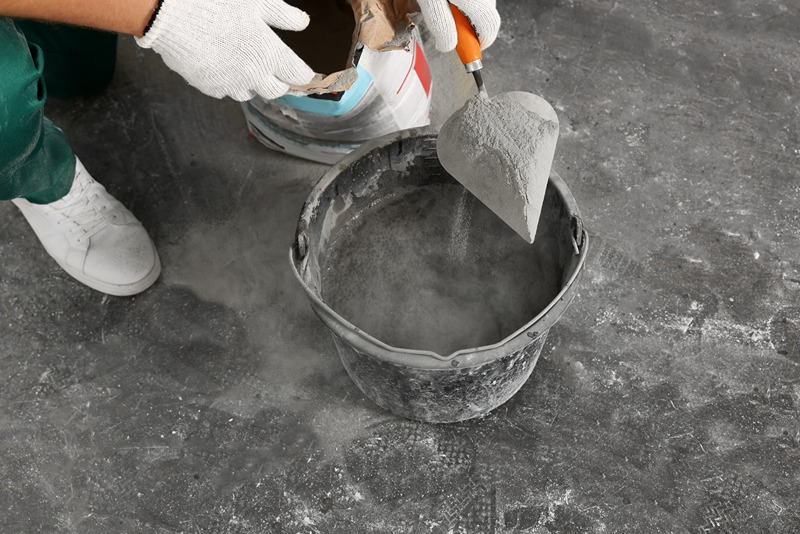
3. Rapid Hardening Cement (RHC) Chemical composition: Higher levels of tricalcium silicate (C₃S), around 55-60%. Effect on construction:
Quick strength gain: RHC sets faster and gains strength quicker than OPC, making it ideal for urgent repairs, road construction, or pre-cast structures.
High early strength: it achieves the same strength as OPC but in a shorter time, beneficial for speeding up construction.
Limited use: due to its fast-setting time, RHC is not suitable for large projects requiring longer working periods.
4. Sulphate-Resistant Cement (SRC) Chemical composition: Reduced levels of tricalcium aluminate (C₃A), typically less than 5%. Effect on construction:
Resistant to sulphates: SRC is specifically designed to resist sulphate attacks, which can damage concrete in sulphate-rich soils or water. It is ideal for foundations, sewage plants, and underground structures.
Longer lifespan: it improves the durability of structures in harsh environments, especially coastal areas where exposure to sulphates can compromise ordinary cement.
5. Low Heat Cement (LHC) Chemical composition: Lower content of tricalcium silicate (C₃S) and tricalcium aluminate (C₃A). Higher content of dicalcium silicate (C₂S). Effect on construction:
Minimised heat generation: LHC produces less heat during hydration, making it suitable for large concrete structures like dams where excessive heat can cause cracks.
Slower setting time: LHC sets slower, allowing more controlled hardening, which is beneficial for large-scale projects requiring gradual strength development.
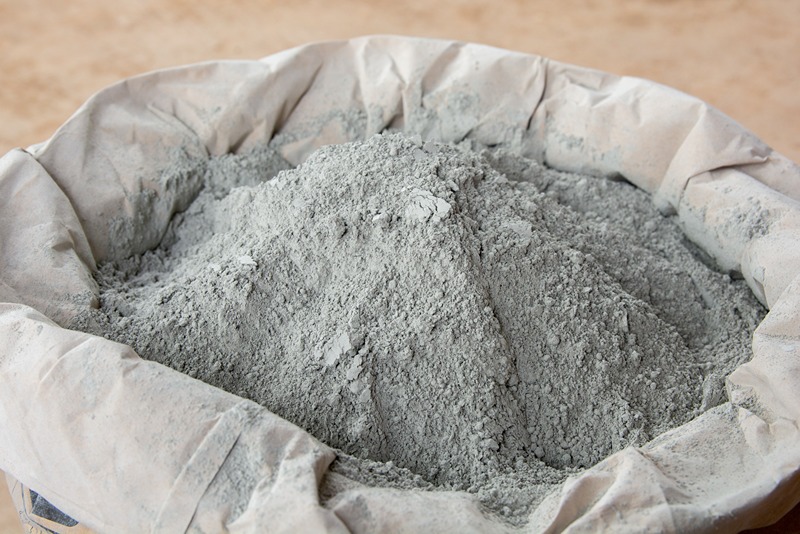
6. White Cement Chemical composition: Similar to OPC but with low iron oxide (Fe₂O₃) content, which gives it a white colour. Effect on construction:
Aesthetic applications: White cement is primarily used for decorative purposes such as in precast panels, tiles, and architectural finishes.
Reflectivity: Its bright surface enhances the aesthetic appeal of buildings, providing a cleaner, modern look.
Expensive: Due to its production process, white cement is more expensive and generally used for decorative purposes only.
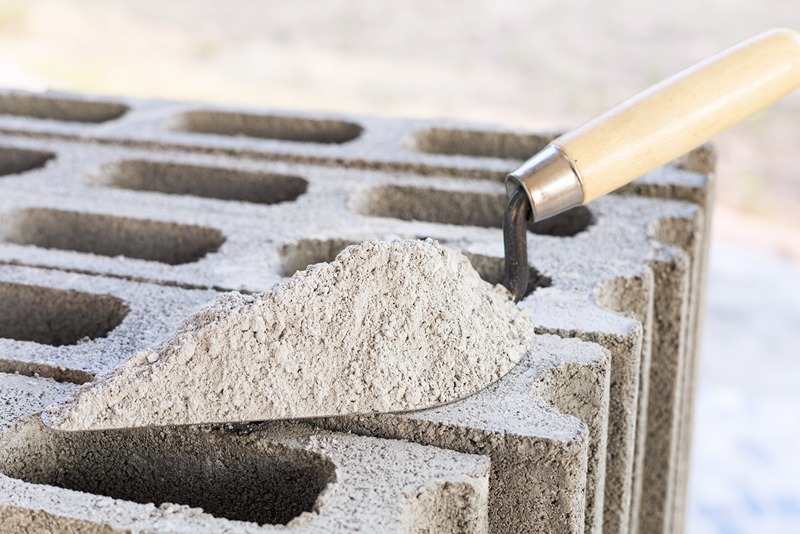
How these chemical properties affect construction
Strength and durability: the chemical composition of cement directly impacts its strength and durability. OPC is ideal for projects requiring high initial strength, while PPC is more suitable for environments where long-term durability is essential.
Setting time: the setting time of cement affects how quickly a project can be completed. RHC, with its high tricalcium silicate content, sets quickly, making it perfect for fast construction. On the other hand, LHC’s slower setting time helps avoid cracks in large concrete pours.
Resistance to environmental conditions: special cements like SRC and PPC are designed to resist chemical attacks and harsh environmental conditions, making them ideal for projects in challenging environments, such as coastal or industrial areas.
Aesthetic finishes: white cement, due to its low iron oxide content, is used for architectural finishes where aesthetics is important, offering a bright, reflective surface for modern designs.
Buy online
Mild SteelStainless SteelStructural SteelTMTCementJSW One MSME
About usBlogsSitemapJSW One TMTPolicy
Terms & conditionsPrivacy policyReturn policy