Ordinary Portland Cement (OPC) is the most common ingredient in the production of concrete, mortar, and other cement-based products. OPC is known for its versatility, strength, and durability, making it suitable for a wide range of construction applications. It is produced through a specific manufacturing process and has distinct characteristics that set it apart from other types of cement.
Manufacturing process
Mining and raw material preparation: The key raw materials, limestone, and clay, are extracted from quarries. These materials are carefully selected and prepared to ensure they meet the desired chemical composition.
Clinker formation: The prepared raw materials are then heated in a rotary kiln at a high temperature (around 1450°C). During this process, the materials undergo chemical reactions, resulting in the formation of clinker nodules. The clinker is then cooled and ground into a fine powder.
Gypsum is added to the clinker during the grinding process. It is typically added in small proportions (usually around 2-3%) to regulate the setting time of the cement.
What are the advantages and uses of OPC cement?
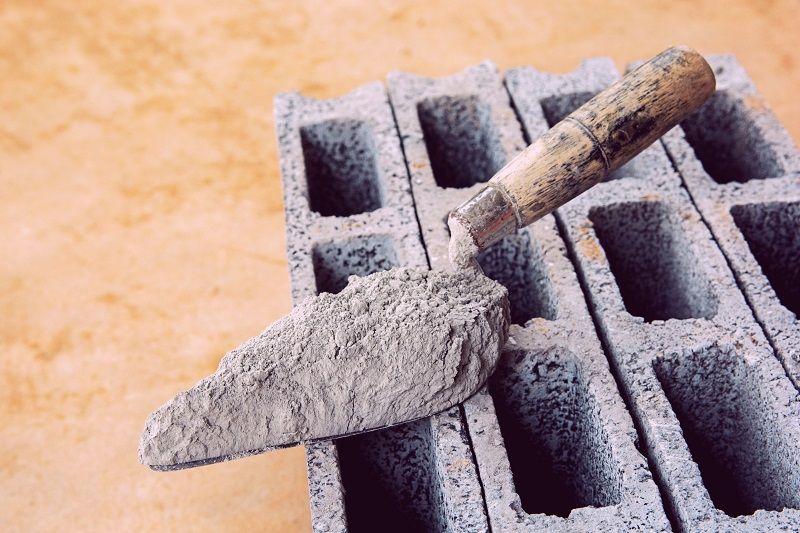
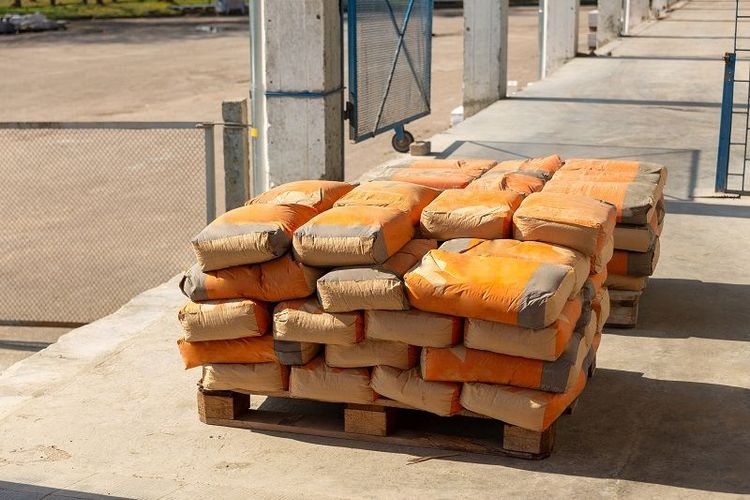
Grinding and packaging: The clinker and gypsum mixture is finely ground to produce OPC cement. The finer the grinding, the higher the strength of the cement. Once the grinding is complete, the cement is packed into bags or bulk containers for distribution and use in construction projects.
Advantages of OPC cement
High compressive strength: OPC cement is renowned for its exceptional compressive strength. It provides the ability to withstand heavy loads and resist external pressures, making it an ideal choice for construction in which structural integrity is crucial. This strength is vital for constructing load-bearing elements like foundations, columns, and beams.
Long-lasting structures: The nature of OPC cement ensures that structures built with it can stand the test of time. It exhibits resistance to wear and tear, making it suitable for projects that demand longevity, such as bridges, dams, and industrial facilities. This durability reduces the need for frequent maintenance and repairs.
Versatility in applications:
Construction of buildings: OPC cement is a versatile material widely employed in the construction of residential, commercial, and industrial buildings. It is used for creating walls, floors, and roofing, providing stability and durability to the entire structure.
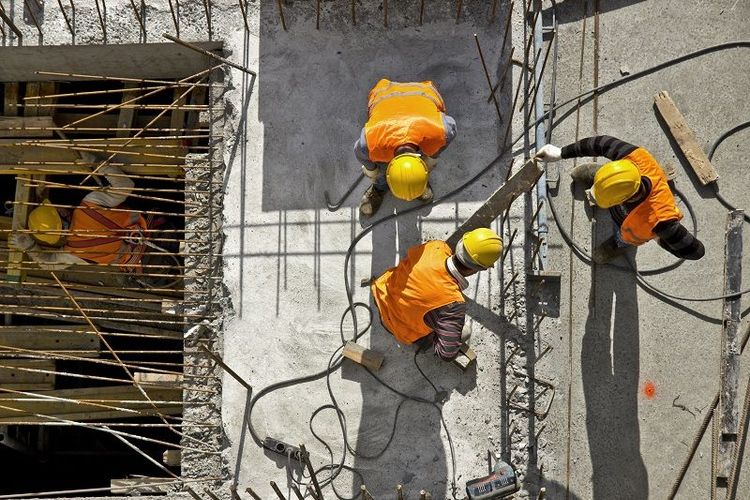
Infrastructure projects: Large-scale infrastructure projects, including roads, bridges, tunnels, and railway tracks, heavily rely on OPC cement. Its strength and durability ensure the safe and long-lasting operation of these critical facilities.
Precast concrete products: The adaptability of OPC cement makes it suitable for producing precast concrete products such as pipes, pavers, blocks, and railway sleepers. These products are used in various construction applications, contributing to cost-effective and efficient building practices.
Cost-effectiveness:
Affordability compared to other types of cement: OPC cement offers a balance between performance and price, making it an accessible choice for a wide range of construction projects.
Value for money in construction projects: The high strength and durability of OPC cement translate into value for money, as it reduces the need for frequent repairs and replacements, ultimately saving construction costs in the long run.
Availability and widespread use: OPC cement is readily available in the market, making it a convenient choice for builders and contractors. Its widespread use reflects the trust builders and engineers place in its reliability and performance. The familiarity with OPC cement simplifies project planning and execution, as it is a well-understood and tested material.
Compatibility with various construction materials:
Adaptable to different aggregates and additives: OPC cement can be tailored to suit specific construction needs by adjusting the mix with various aggregates and additives. This adaptability allows for customisation, enabling the creation of concrete with desired properties such as increased workability, faster curing times, or enhanced resistance to environmental factors.
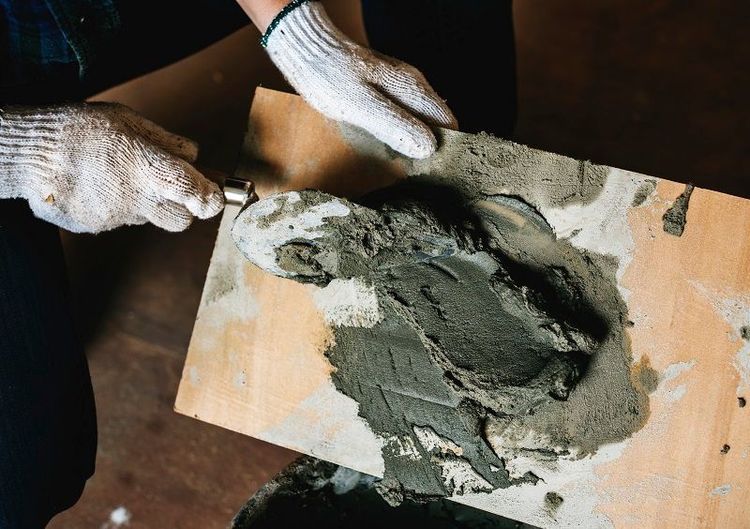
Different grades and types:
OPC 33 grade: This grade provides a minimum compressive strength of 33 MPa. It is suitable for non-structural applications like plastering, flooring, and general construction work.
OPC 43 grade: With a minimum strength of 43 MPa, this grade is widely used for general construction purposes, including residential and commercial buildings.
OPC 53 grade: This high-strength grade offers a minimum compressive strength of 53 MPa, making it suitable for critical structural applications such as bridges, high-rise buildings, and infrastructure projects.
Types of OPC cement:
Ordinary portland cement (OPC): The standard, grey OPC cement, is ideal for most construction applications.
Rapid hardening OPC (RHPC): This type sets and hardens faster than standard OPC, making it suitable for repair and construction projects that require quick curing.
Sulphate-resistant OPC (SRC): Designed to resist the detrimental effects of sulphate attack, this type is used in areas with high sulphate content in soil or water.
Selection criteria based on project requirements:
Strength requirements: The selection of OPC grade should align with the project's structural requirements. Lower grades may be sufficient for non-structural elements, while higher grades are essential for load-bearing structures.
Curing time: Consider the project timeline and the curing time required. For time-sensitive projects, rapid-hardening OPC may be the preferred choice.
Exposure conditions: Assess the environmental exposure of the construction site. For projects in areas prone to sulphate attack, such as coastal regions, the use of sulphate-resistant OPC is advisable to prevent degradation.
Budget constraints: The budget for the project plays a significant role in selecting the OPC grade. While higher grades may offer superior strength, they can be more expensive. Balancing strength requirements with cost considerations is essential.
Choosing the right OPC cement variety involves assessing the project's specific needs in terms of strength, curing time, exposure conditions, and budget constraints. Selecting the appropriate grade ensures that the construction material meets the performance requirements of the project while maintaining cost-effectiveness.
Buy online
Mild SteelStainless SteelStructural SteelTMTCementJSW One MSME
About usBlogsSitemapJSW One TMTPolicy
Terms & conditionsPrivacy policyReturn policyBanking partner