The cold rolling process is a highly effective metalworking technique used to improve the mechanical properties, surface finish, and dimensional accuracy of various metals. Unlike hot rolling, which involves working metals at elevated temperatures (850 degrees celsius to 1200 degrees celsius), cold rolling is performed at room temperature (60 degrees celsius to 180 degrees celsius). This process of cold rolling offers enhanced strength, formability, and dimensional precision. For example, the cold rolled coils and sheets of IS 513 (Part 1):2016 CR2 are known for their high strength, smooth surface quality, easy paintability and high formability. According to the IS 513 standard (cold reduced low carbon steel sheet), CR2 grade is annealed and is in skin-passed condition, meaning it undergoes light cold rolling to improve its surface quality and remove any residual stresses. Ensure quality in every build—sign up today to explore our premium industrial supplies.
In this blog, we will delve into the world of cold rolling steel, its significance, and the benefits it offers.
What is cold rolling?
Cold rolling is a manufacturing process employed to shape and enhance the properties of steel sheets and coils. Unlike hot rolling, which involves heating the metal to high temperatures before passing it through rollers, cold rolling is performed at room temperature or slightly below the recrystallisation temperature. This process of compression and elongation refines the material's structure and yields a wide range of benefits, making it an indispensable technique in the steel industry.
A cold rolling mill is a specialised machine used in the metalworking industry to process and shape metal sheets or strips through the cold rolling process. Cold rolling involves passing the material between a series of rollers to achieve the desired thickness reduction, improved surface finish, and enhanced mechanical properties. Here’s how a cold rolling mill works:
Material loading:
The process begins by loading the material on the entry side of the cold rolling mill. The material may have undergone prior processing steps like hot rolling and preparing it for cold rolling.
Understanding the art of cold rolling of steel
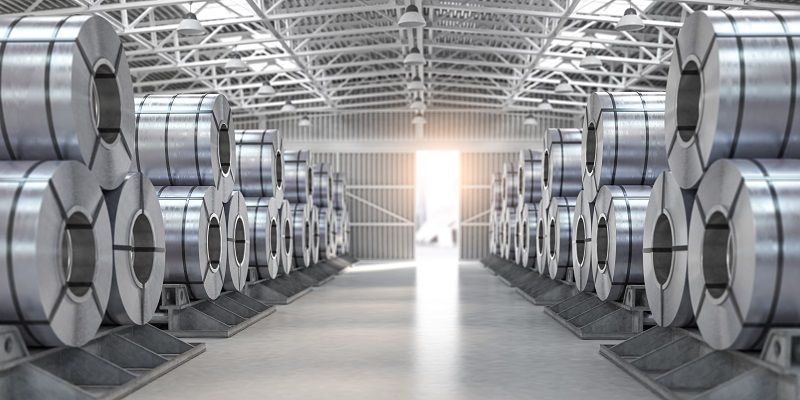
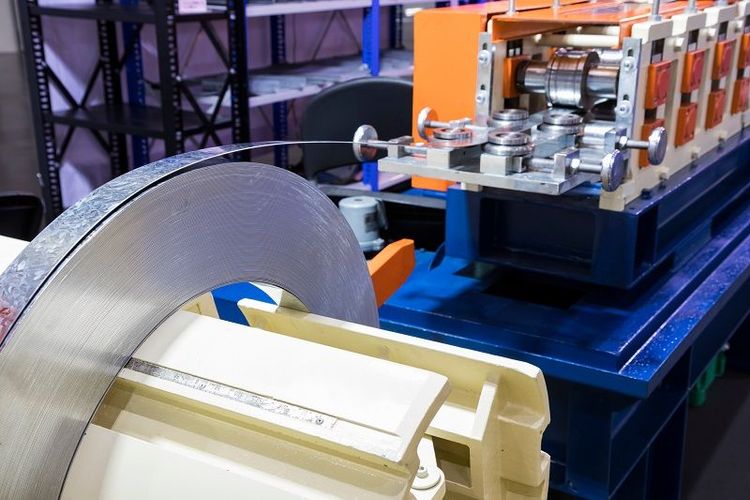
Feeding and tensioning:
The material is then fed through the cold rolling mill's entry section. To ensure smooth and continuous processing, the material is tightly tensioned between the entry and exit sections of the mill. Don't miss out on expert insights—register to stay informed.
Rolling process:
As the material passes through the cold rolling mill, it goes through a series of rollers that gradually reduce its thickness. The rollers are set at specific gaps or clearances, which determine the degree of reduction achieved at each stage. Temperature ranges typically from 60 degrees celsius to 180 degrees celsius and the desired reduction in thickness of the material is from 6 mm to 0.06 mm.
Reversing mill (optional):
In some cold rolling mills, particularly for thinner materials, a reversing mill arrangement is used. This means the material is rolled back and forth in the main rolling mill to achieve the desired thickness reduction.
Tandem mill:
The tandem rolling mill consists of multiple stands, through which the work material passes continually. The thickness of the work strip is reduced by a certain amount at each stand, resulting in a significant total reduction between the first and last stand.
Annealing (optional):
For certain materials and applications, intermediate annealing (also known as process annealing) may be performed between rolling passes. This annealing process helps relieve internal stresses and improves the material's ductility, allowing for further reduction without the risk of cracking. This process is performed from 260 degrees celsius (500 degrees fahrenheit) to 760 degrees celsius (1400 degrees fahrenheit).
Skin passing (temper rolling) (optional):
After the primary cold rolling, the material may undergo skin passing or temper rolling. This is a light cold rolling process applied to improve the surface finish and prolong the ageing behaviour especially in low carbon steel grades.
Exit section and coiling line:
Once the desired thickness and properties are achieved, the cold-rolled material exits the mill. It may be coiled into rolls or cut into sheets, depending on the application and customer requirements.
What is the purpose behind applying the close annealing process to Cold Rolled Close Annealed (CRCA) material?
The close annealing procedure involves subjecting cold rolled steel to high temperatures, just below 720 degrees celsius while preventing the steel coil from coming in contact with oxygen to avoid oxidation. This operation, spanning a duration of 2 to 3 days, often takes place within a bell furnace. Through close annealing, the lamellar pearlite structure undergoes a transformation into spheroidal cementite, leading to a significant improvement in ductility.
Ductility is an essential characteristic of steel, allowing it to undergo processes like drawing. The drawing process is classified into different grades such as simple drawing, deep drawing, extra deep drawing, and non-aging extra deep drawing quality grades.
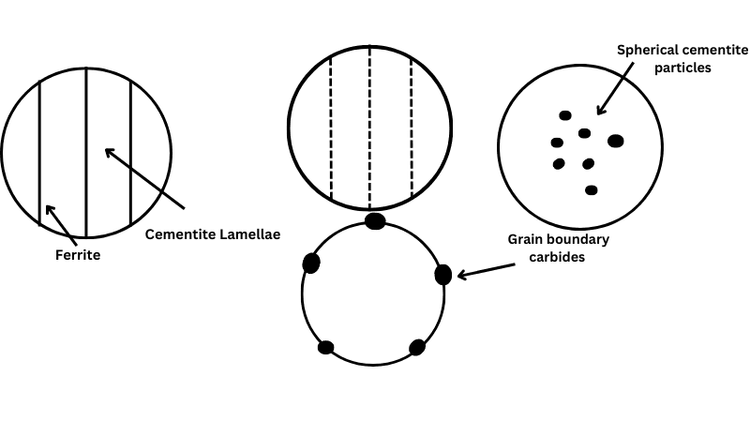
Different grades of cold rolled steel
There are different grades that refer to the quality and suitability of the cold-rolled steel for various applications. Join our community to learn more—register today!
CR1 - Commercial Quality (CQ) or Ordinary (O) Grade: This grade represents a basic quality level suitable for general commercial applications where surface smoothness and finish are not critical factors. CR1 has 0.15% of carbon - it is harder than rest of the grades and less formable. It might be used in applications that do not require intricate forming or deep drawing.
CR2 - Drawing Quality (D) Grade: CR2 has 0.08% of carbon. This grade offers improved surface finish and formability compared to CR1. It is suitable for applications that involve moderate forming or drawing processes, such as appliances, and general engineering components.
CR3 - Deep Drawing Quality (DD) Grade: CR3 has 0.02% carbon. It is specifically designed for deep drawing applications. Deep drawing involves forming a sheet into three-dimensional shapes like kitchen utensils, automotive components, and certain containers.
CR4 - Extra Deep Drawing Quality (EDD) Grade: CR4 has 0.015% of carbon. It is intended for applications requiring intricate and complex deep drawing processes. EDD steel can be door inners, dash panels and bodyside inners.
Advantages of cold rolling steel
Enhanced surface finish: Cold rolling refines the surface of steel, creating a smoother and more polished appearance. This is especially significant for applications where aesthetics play a crucial role, such as in decorative items and architectural elements.
Precise dimensional control: Cold rolling allows for tight regulation of steel's thickness and width. This precision is essential in industries with stringent tolerance requirements, like the automotive and aerospace sectors.
Improved mechanical properties: The cold rolling process enhances the hardness and strength of steel while preserving its ductility. This makes the material more suitable for applications that demand durability and resistance to wear.
Stress and grain refinement: Cold rolling reduces internal stresses and refines the grain structure of steel. As a result, the material exhibits improved mechanical properties and increased resistance to corrosion and cracking.
Conclusion
Cold rolling is a fundamental process that shapes steel into sheets and coils with remarkable precision, improved mechanical properties, and a flawless surface finish. Its wide array of benefits makes it an essential technique in various industries where steel is used. From enhancing surface aesthetics to providing high strength and durability, cold rolling plays a crucial role in the production of steel products we encounter in our daily lives.
Buy online
Mild SteelStainless SteelStructural SteelTMTCementJSW One MSME
About usBlogsSitemapJSW One TMTPolicy
Terms & conditionsPrivacy policyReturn policyBanking partner