Top techniques for welding TMT bars
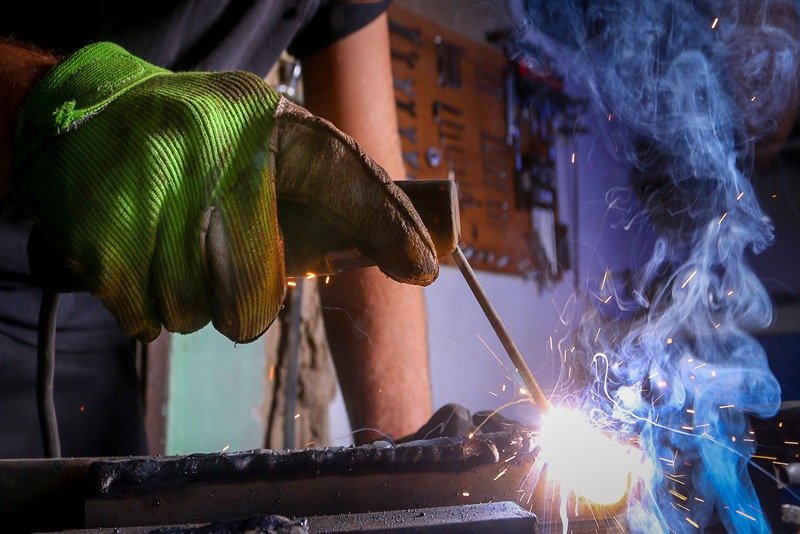
To ensure the safety of workers during Thermo-Mechanically Treated (TMT) bar welding, personal protective equipment (PPE) such as welding helmets, flame-resistant clothing, gloves, and steel-toed boots must be worn. Proper ventilation systems, a clutter-free workspace, fire extinguishers, and regular equipment inspection are also necessary. Finally, training and certification for welders on appropriate techniques and safety protocols are essential to promote a safety culture in TMT bar welding operations. Looking for high-quality industrial materials? Register now to access our extensive industrial material selection. The role welding plays in the use of TMT bars in construction.
Structural integrity: TMT bars often reinforce concrete structures such as buildings, bridges, and dams. Welding allows these bars or other structural elements to be connected securely, ensuring the overall integrity and stability of the structure.
Joint strength: welding TMT bars together creates strong and durable joints that can withstand the forces and stresses experienced by the structure, including tension, compression, and shear forces. This is essential for ensuring the structural safety and longevity of the construction.
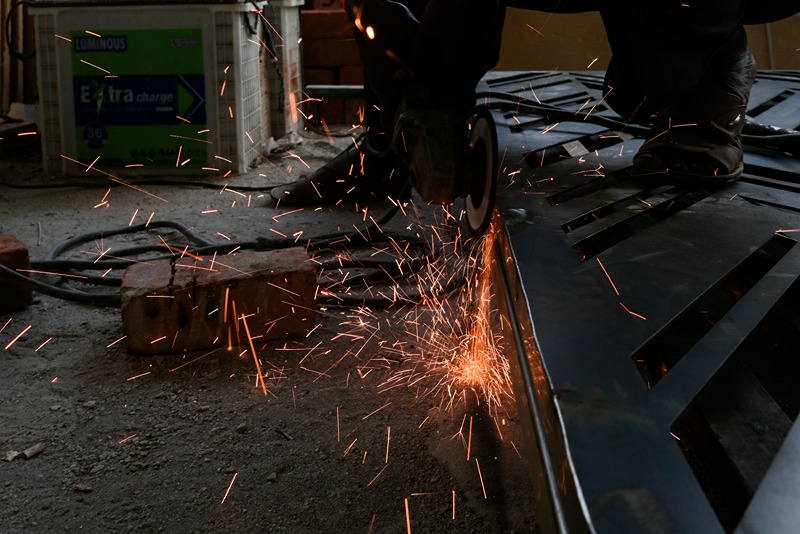
Customisation and adaptability: welding provides flexibility in construction projects by allowing TMT bars to be cut, shaped, and welded into various configurations to meet specific design requirements. This enables architects and engineers to create custom solutions for complex structural challenges.
Seismic resistance: in regions prone to earthquakes, proper welding of TMT bars is crucial for enhancing the seismic resistance of structures. Welded connections between TMT bars help distribute and dissipate seismic forces, reducing the risk of structural failure during earthquakes.
Construction efficiency: welding TMT bars can streamline the construction process by facilitating faster assembly and installation of structural elements. This can lead to cost savings and improved project timelines, making welding essential to efficient construction practices.
Here are some commonly used welding techniques for TMT bars
Shielded Metal Arc Welding (SMAW)
SMAW, also known as stick welding, is a commonly used technique for welding TMT bars.
It involves using a consumable electrode coated in flux to create the arc and the weld.
SMAW is versatile and can be used for welding TMT bars of various thicknesses.
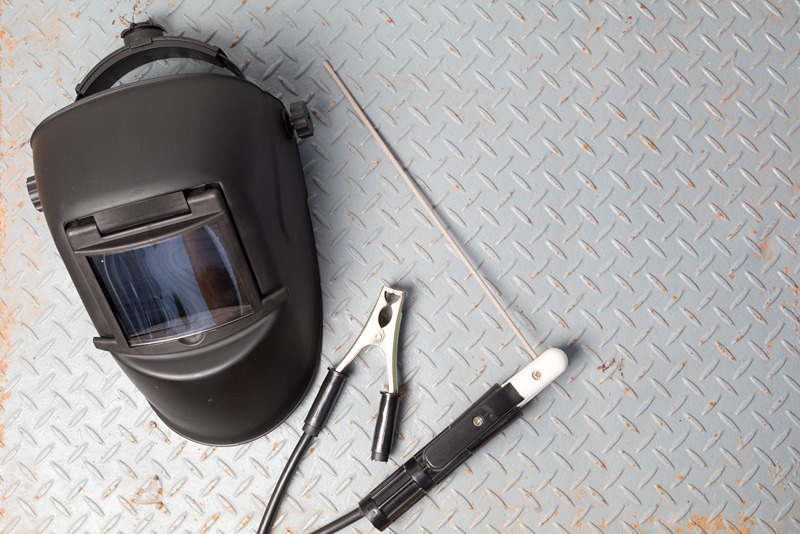
Gas Metal Arc Welding (GMAW)
GMAW, also known as Metal Inert Gas (MIG) welding, creates the weld by continuously feeding a wire electrode and a shielding gas to create the weld.
This technique is suitable for welding TMT bars in industrial settings requiring high productivity.
Discover superior industrial materials by registering on our platform for exclusive access.
Gas Tungsten Arc Welding (GTAW)
GTAW, known as Tungsten Inert Gas (TIG) welding, uses a non-consumable tungsten electrode and a shielding gas.
It produces high-quality welds with precise control over the heat input, making it suitable for welding TMT bars where aesthetics and quality are essential.
Stud welding
Stud welding involves welding a metal stud to the surface of the TMT bar.
It commonly attaches other structural elements, such as brackets and plates, to TMT bars.

Resistance spot welding
The stud welding gun melts the stud and TMT bar with an electrical arc, and then the stud is pressed onto the bar. Once the metal cools and solidifies, the attachment is secure.
Stud welding is a technique used to attach metal studs or fasteners to the surface of TMT bars.
Challenges and solutions in TMT bar welding The Heat Affected Zone (HAZ) presents a critical concern as it can compromise the structural integrity of welded joints. The excessive heat generated during welding can lead to undesirable changes in the material's microstructure, potentially resulting in reduced strength and ductility. Addressing this challenge requires meticulous control of welding parameters, like voltage, current, welding speed, arc length and cooling rates, along with the implementation of preheating and post-weld heat treatment techniques. Additionally, weldability issues arise when working with high-strength TMT bars, which often exhibit higher carbon content and alloying elements. These characteristics can contribute to increased hardness and reduced weldability, leading to cracking, porosity, and incomplete fusion issues. To overcome these challenges, specialised welding procedures and consumables may be necessary. This includes preheating and managing the temperature between successive welding passes during multi-pass welding and selecting appropriate filler metals and fluxes.
Buy online
Mild SteelStainless SteelStructural SteelTMTCementJSW One MSME
About usBlogsSitemapJSW One TMTPolicy
Terms & conditionsPrivacy policyReturn policy