TMT steel manufacturing process: A comprehensive guide
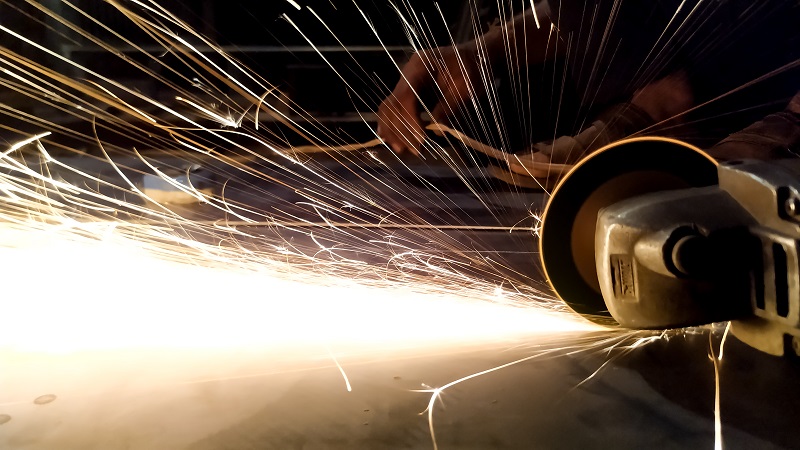
TMT (Thermo-Mechanically Treated) steel has gained immense popularity in the construction industry due to its exceptional strength, durability, and resistance to corrosion. The high-quality TMT steel is divided into primary and secondary types and is produced through a precise and complex manufacturing process that involves several stages. Primary TMT bars typically have a relatively lower tensile strength and yield strength compared to secondary TMT bars. In this comprehensive guide, we delve into each step of this process of both TMT steel: Primary Steel The primary steelmaking process involves the following steps: 1. Pretreatment of raw materials. The mined iron ore undergoes processing to remove impurities and improve quality. This may include crushing, grinding, magnetic separation, and/or flotation to obtain a concentrate. This is followed by sintering which means heating it to high temperatures in the presence of coke and limestone. This process produces clinker that is rich in iron. 2. Blast furnace smelting: Sintered iron ore, coke, and limestone are charged into a blast furnace. The blast furnace is a tall, cylindrical furnace that is heated by hot air blown into the bottom of the furnace. The coke burns in the blast furnace and produces carbon monoxide, which reduces iron ore to molten iron. Limestone reacts with the impurities in iron ore to form slag. This is a molten waste product removed from the top of the blast furnace. 3. Basic oxygen steelmaking (BOS): The molten iron from the blast furnace is transferred to a BOS furnace. In the BOS furnace, oxygen is blown through the molten iron, which oxidises the carbon and other impurities in the iron. This process lowers the iron carbon content and produces molten steel. 4. Alloy addition: The molten steel from the BOS furnace may be alloyed with other elements, such as manganese, chromium, and nickel. These alloying elements are added to the molten steel to give it the desired properties. 5. Casting: Molten steel is then cast into moulds to produce ingots or slabs. The ingots or slabs are then further processed to produce the desired finished steel products.
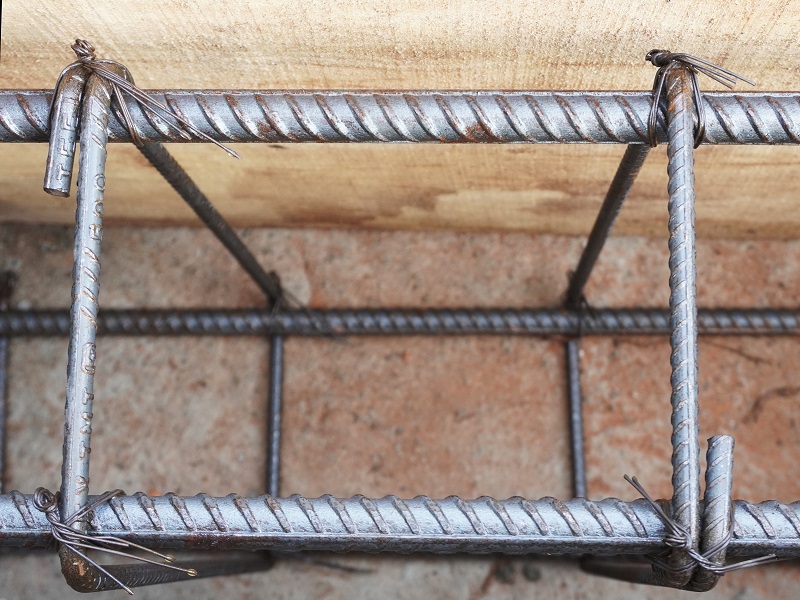
Secondary Steel
The secondary steelmaking process is the second step in steel production. It adjusts the chemical composition of the steel to the desired specifications. The secondary steelmaking process typically involves the following steps: 1. Ladle furnace refining: This includes reusing scrap metal generated during production and recycling cooling water. In the ladle furnace, the steel is heated and stirred. This process helps to remove impurities from the steel and to distribute the alloying elements evenly throughout the steel. 2. Melting: The prepared scrap steel is then melted in an electric arc furnace or a basic oxygen furnace. The intense heat melts the steel, resulting in molten metal. 3. Desulphurisation: The steel sulphur content is adjusted by adding lime to the molten steel. The lime reacts with the sulphur to form slag, which is a molten waste product that is removed from the top of the ladle furnace. 4. Continuous casting. Molten steel is then cast into molds to produce ingots or slabs. The ingots or slabs are then further processed to produce the desired finished steel products. 5. Hot Rolling: The solidified billet, bloom, or slab is then reheated in a furnace to a temperature suitable for hot rolling. Hot rolling involves passing heated steel through a series of rolling mills that reduce its thickness and shape it into the desired form.
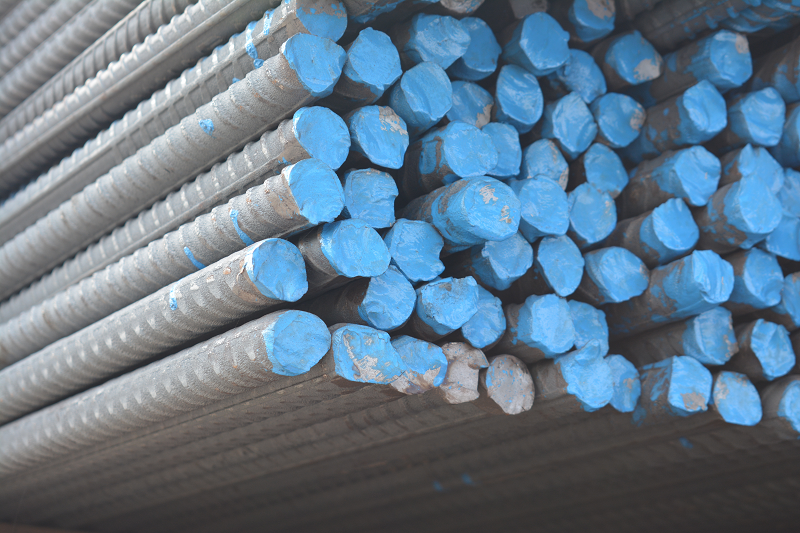
6. Cold rolling: In some cases, hot-rolled steel may undergo additional cold rolling processes to achieve dimensional tolerances, surface finishes, or mechanical properties. Cold rolling involves passing hot-rolled steel through a series of rollers at room temperature, which further reduces its thickness and improves its surface finish. 7. Quenching: Following the hot rolling stage, the TMT bars undergo a quenching procedure whereby they are passed through a series of water jets or cooling pipes. This rapid cooling causes the outer surface to cool quickly while the core remains hot. Consequently, the surface layer hardens and forms a martensitic structure, while the core retains its relative softness and ductility. 8. Self-tempering: After the quenching process, the TMT bars are left to cool naturally in the ambient air. During this period, the heat from the hot core of the bar transfers to the hardened surface, resulting in a self-tempering effect. This self-tempering process gives rise to a tough and ductile ferrite-pearlite microstructure in the TMT bars, enhancing their strength and flexibility. 9. Atmospheric cooling: Once the self-tempering phase is complete, the TMT bars are allowed to cool down to room temperature in the open air. This atmospheric cooling step further stabilises the microstructure and helps alleviate any remaining residual stresses. By following the detailed guide provided, one can gain a comprehensive understanding of the TMT steel manufacturing process and appreciate the efforts and expertise involved in producing this remarkable construction material. The TMT bars on our website are just what your business needs, as they are manufactured with a commitment to continuous improvement and innovation in our production processes. The construction industry is constantly evolving, with new challenges and demands emerging over time. To meet these evolving needs, TMT steel manufacturers must focus on continuous improvement and innovation in their production processes.
Buy online
Mild SteelStainless SteelStructural SteelTMTCementJSW One MSME
About usBlogsSitemapJSW One TMTPolicy
Terms & conditionsPrivacy policyReturn policy