The journey of steel from start to finish
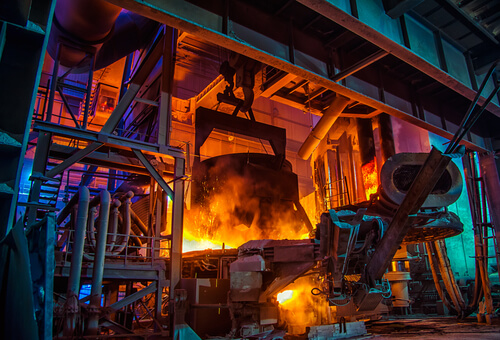
The entire process of converting raw materials into finished stainless steel is quite a lengthy one, but it can be simplified and broken down into six primary steps. Let’s look at these interesting steelmaking process steps.
1. Producing iron
Iron ore, when mined, is a combination of iron with oxygen and several other unwanted substances, which are known as gangue. To produce pure steel, the products that are involved in the steel making process (such as iron ore, coke and lime) must be converted into iron. All these raw materials are placed in a blast furnace and Corex furnace and further melted down to produce hot metal or molten iron. Besides bulk iron ore, prepared burden (such as sinter and pellets) is also fed into the furnace. At this point too, the iron contains several impurities, which need to be removed to make sure that the metal is not brittle. To achieve this, metallic iron is then passed to the steelmaking process as a liquid at nearly 1450°C. This iron is known as hot metal or pig iron.
2. Primary steelmaking
During the process of refining iron to produce steel, the carbon content of hot metal is successfully lowered, generally to less than 1% through an oxidation process in a BOF or Basic Oxygen Steelmaking Furnace. Post completion of this, alloys are added to the furnace to attain the needed chemical composition of the end product in a Ladle Refining Furnace. The content of chemicals is controlled very meticulously during this stage. Previously, most steels were produced through processes such as the bessemer and open Hearth. But these have now been replaced by ultramodern processes such as basic oxygen steelmaking. To remove all impurities, the molten metal is further infused with scrap steel. Oxygen too will be forced through the furnace, which gets rid of carbon and several other impurities. When it comes to electric furnaces, electricity needs to be forced through the furnace, achieving identical results. De-gassing is the ultimate step in steelmaking, wherein all the gaseous particles are eventually removed in the presence of a vacuum atmosphere. After completion of this process, we now have raw steel.
3. Secondary steelmaking
The different grades of available steel are used for different purposes. The grading depends on which elements are still present in the metal, such as carbon dioxide. Most of the carbon will be eventually removed, but it will be substituted by aluminium to produce drawing quality steel. To produce structural steel, additional carbon is left inside, and this imparts greater tensile strength to the steel. Specific techniques can be successfully implemented to change the level of impurities left behind, including stirring, increasing or decreasing the temperature, removing all gasses and ladle injection. When this process is complete and the right grade has been accomplished, the next step can be carried about.
4. Continual casting
In this step, molten steel is cast into cooling moulds. This enables hardening of the steel, following which the steel is drawn out while it is still hot. Guided rollers are then used to pull it out. The steel is then accurately cut into the needed lengths. This steel can be then used to produce billets, beams and slabs, among others. When the parts are completely cooled, they are then sent for a further rolling process known as primary forging.
5. Primary forging
During this process, the rough-cast items are precisely formed into the desired shapes through hot rolling, which gets rid of any defects in the shape and delivers the desired quality levels. The cast steel can be efficiently rolled in successive steps to produce one of the many desired shapes of steel. Of all the shaping methods, rolling is the most common. The precise amount of work to which steel is subjected to along with the temperature during rolling will significantly determine its physical characteristics - whether the steel can successfully be bent, cut, machined, or formed into pipes, tubes or wires. The process of hot rolling can be used to produce seamless tubing, a wide range of bespoke items, and long and flat products. Rolled steel that is produced from slabs is known as flat steel products whereas that produced from billets/blooms is known as long steel products.
6. Secondary forging
To accomplish the final desired shape of steel, there are numerous secondary techniques that can be put into practice such as coating, thermal treating, joining, pressing, drilling, machining and riveting.
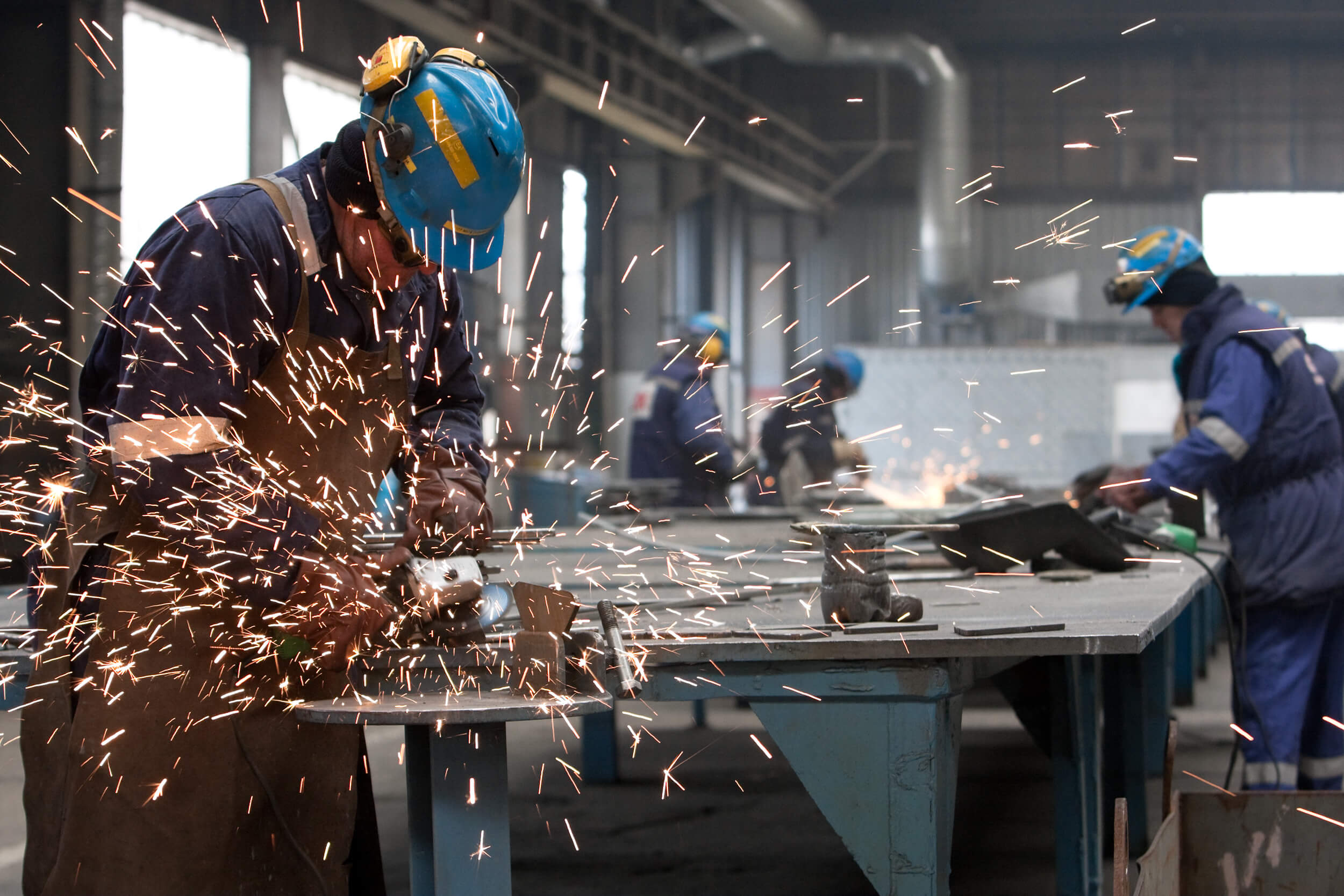
This is the entire journey of steel from start to finish.
Let’s now look at some of the diverse types of steel products.
Flat steel products
Flat steel is further categorised into three categories based on the type of process involved: (1) Hot Rolled Steel (HR), (2) Cold Rolled Steel (CR), and (3) Coated Steel.
Hot rolled steel products
To produce hot rolled steel products, slabs will be thoroughly rolled in a Hot Strip Mill or HSM. The relative plasticity of steel at temperatures that fall between 800°C and 1200°C (which is above the recrystallisation temperature) makes it possible to successfully roll steel into a wide range of useful shapes, while simultaneously enhancing its mechanical properties. Usually, the more the steel is hot rolled, the tougher and denser it becomes. HR Coil ranges from 1.6-25 mm in thickness and is produced in HSM. HR coils are further processed into HR plates as well as Hot Rolled Pickled and Oiled Coils/Plates (HRPO) based on the requirements.
Cold rolled steel products
The HR coil is eventually uncoiled and cleaned or pickled, in an acid-containing long tank. This process successfully removes the blue/black oxide and scales from the surface. After this, the steel is rinsed and trimmed before making its way to the cold reduction mill. The clean pickled coil’s leading end is then fed through a set of rolls and then, onto a recoiler. Cold reduction mills comprise up to 6 stands, and a majority are of the four-high variety. Through a combination of extremely high roll force and strip tension, the thickness of the steel is reduced at each stand progressively. The pickling and cold reduction are continuous processes. Post pickling, the strips are joined from end to end before they are passed through the reduction stands. Post cold rolling, the steel may be annealed or tempered to improve its metallurgical properties.
Coated steel
Coating on steel enhances corrosion resistance as well as the aesthetic value of the final product. Coated steel is further classified based on the type of coating process that is involved. These are tin coated steel, Galvanised (GI), Galvalume (GL), Galvannealed (GA), Pre-Painted Galvalume (PPGL), and Pre-Painted Galvanised (PPGI).
Long steel products
Long steel products are manufactured from billets or blooms in the hot rolling process. These mills differ significantly from flat products mills in the fact that the rolls that are used for bars and wire-rod products are profiled. In most cases, several passes are needed to produce the final shape. Several types of alloy steel are produced in the bars and wire-rod form. The technologies used are High Yield Quenched and Self Tempered to produce TMT rebars and ultimately ensure superior quality as well as sustainable products.
We will now look at some of the innovative technologies to minimise the environmental impact when it comes to the production of steel.
HYBRIT process
The goal of using HYBRIT or Hydrogen Breakthrough Ironmaking Technology is to produce zero-carbon in the process of steel production. This new-generation procedure uses hydrogen, which can remove oxygen present in the iron ore. Yet, the outcome is water vapour and not carbon dioxide. This leads to the formation of green steel.
Jet process
One of the latest technologies when it comes to exceptional converters is the Jet Process. Because of this advancement, a wide scope of scrap rates can be successfully handled in a highly profitable way. The Jet Process is an innovative technique for the amplification of scrap rates and HBI (Hot Briquetted Direct Reduced Iron) rates when it comes to converter steelmaking.
Molten oxide electrolysis
Molten Oxide Electrolysis is an unorthodox electrometallurgical system that makes it possible for quick production of metal from oxide raw material to the liquid state. It ensures significant simplification of the entire process and minimisation of essential energy needs.
The last word
The journey of steel from the initial raw materials right up to the finished product is quite fascinating. That said, it can take a toll on the environment, making it necessary to work towards eco-friendly and sustainable ways in the process of steel production. JSW Steel is committed to manufacturing sustainable and environment-friendly steel, increasingly in the future. We use technology such as High Yield Quenched and Self Tempered in production to ensure superior quality and sustainable products. We are also among the first Indian steel manufacturers to have received GreenPro Ecolabel certification which makes us environment-friendly and sustainable manufacturers. The steel industry across the globe is learning to adapt and change towards a greener future, and JSW is one among them.
Visit JSW One MSME, a one-stop marketplace dedicated to fulfill all your industrial product requirements . Benefit from the seamless digital highway connecting steel manufacturers in India and abroad with steel dealers and MSMEs. The best part is that you can buy quantity as little as 2 tons , online through expert guidance in every step of the way.
Buy online
Mild SteelStainless SteelStructural SteelTMTCementJSW One MSME
About usBlogsSitemapJSW One TMTPolicy
Terms & conditionsPrivacy policyReturn policy