Structural steel connections: bolted vs welded joints - pros, cons, and applications
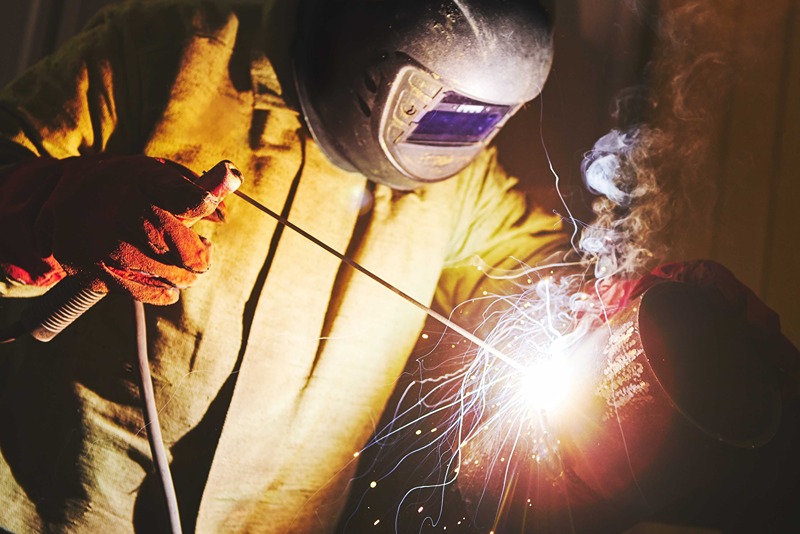
In steel construction, the choice of connection type can significantly impact the structure's strength, cost, and performance. The two primary methods for connecting structural steel components are bolted and welded joints. When the metal gets thicker, you must change the joint design to strengthen the weld. Register with us today to access high-quality steel products. Each method has its pros and cons and specific applications where one may be more suitable.
Types of joints in structural steel
Understanding the types of joints and their applications is crucial for selecting the appropriate connection method. Common types of joints in structural steel include:
Butt joints: used when two pieces are placed end-to-end.
Lap joints: involves overlapping two pieces.
T-joints: formed when one piece is perpendicular to the other.
Corner joints: created when two pieces meet at a corner.
Edge joints: used when the edges of two pieces are joined together.
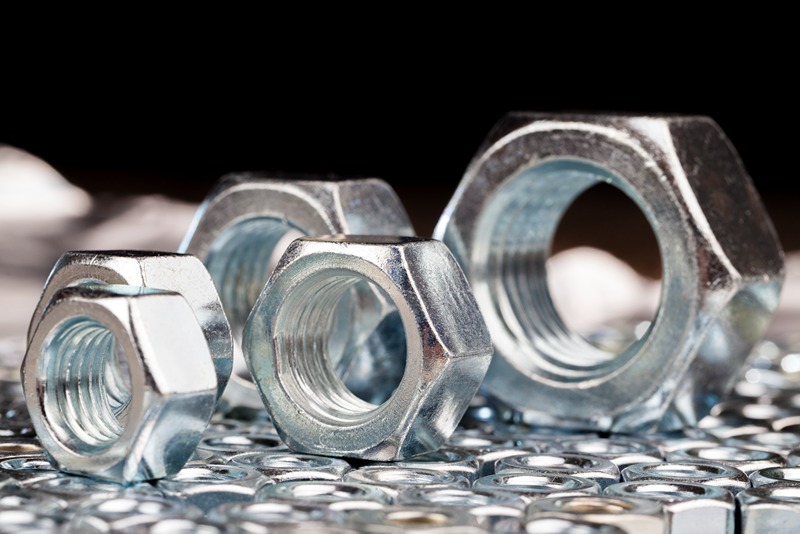
Bolted joints Pros
Ease of installation: bolted joints are generally more accessible and faster, making them ideal for projects with tight timelines.
Flexibility: bolted connections can be easily dismantled and reassembled, offering flexibility for future modifications or repairs.
Quality control: the quality of bolted joints is more accessible to inspect and verify than welded joints.
Cons
Aesthetic concerns: bolted joints may be less visually appealing than welded joints, particularly in exposed architectural structures.
Potential for loosening: bolts can loosen over time due to vibrations or dynamic loads, requiring periodic maintenance.
Applications
Temporary structures: ideal for structures that need to be disassembled or relocated.
Large fabrications: used in large-scale projects like bridges and buildings where prefabricated components are assembled on-site.
Industrial installations: standard in industrial setups where machinery and equipment need frequent maintenance or replacement.
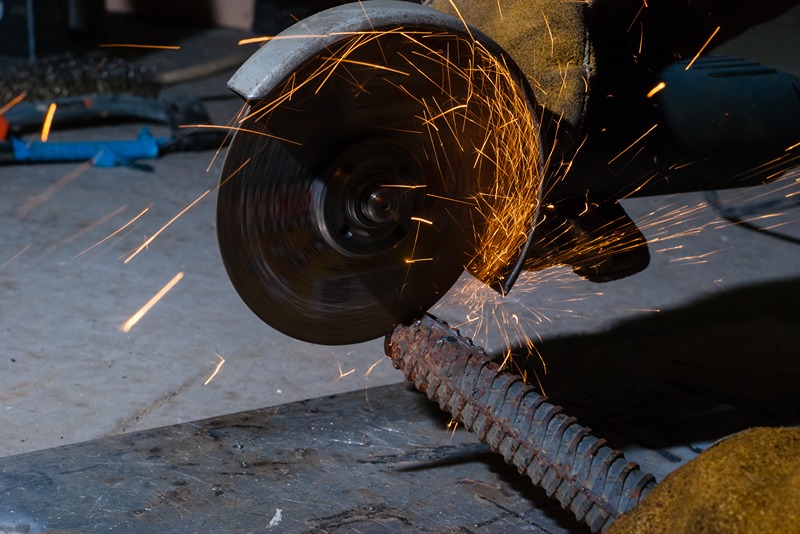
Welded joints Pros
Strength and rigidity: welded joints typically provide greater strength and rigidity, creating a monolithic structure that can better withstand loads.
Aesthetics: welded joints offer a cleaner, more seamless appearance, which is desirable in architectural and visible structures.
No additional components: welding does not require extra components like bolts or nuts, reducing the number of parts needed.
Cons
Complexity: welding requires skilled labour and specialised equipment, increasing the complexity and cost of installation.
Inspection challenges: inspecting the quality of welds can be more difficult, requiring non-destructive testing methods.
Permanent connection: welded joints are permanent and cannot be easily dismantled or modified.
Applications
High-strength requirements: used in structures where high strength and rigidity are paramount, such as high-rise buildings, bridges, and offshore platforms.
Architectural structures are preferred in applications where aesthetics is essential, like exposed steel structures and artistic installations.
Heavy machinery: standard in fabricating heavy machinery and equipment requiring robust connections.
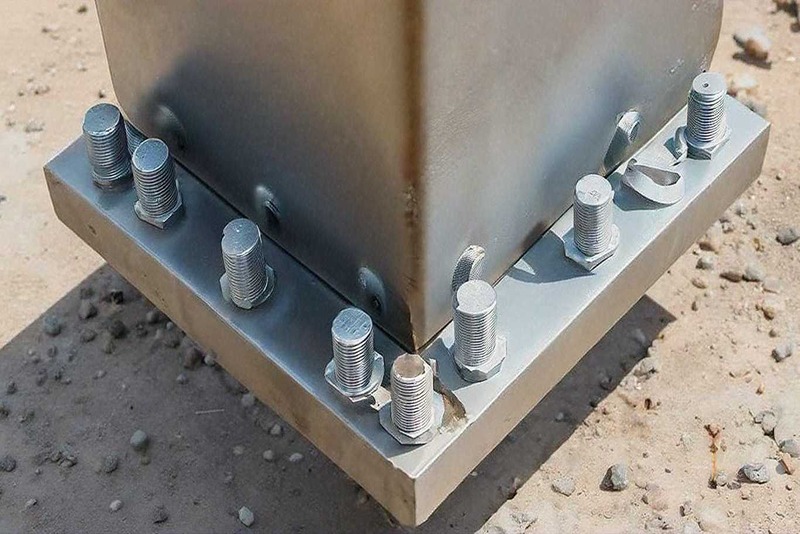
Types of welds Understanding the different types of welds is essential for selecting the appropriate welded joint for your application. Common weld types include:
Fillet weld: used for lap joints, t-joints, and corner joints, providing a triangular cross-section.
Butt weld: used for butt joints, where the edges of two pieces are joined together.
Groove weld: used when the joint requires a deep penetration, suitable for thick materials.
Plug and slot welds: used to join two overlapping pieces by welding through one piece into another.
Steel prices and their impact
The cost of steel plays a significant role in choosing between bolted and welded joints. Factors such as steel price fluctuations, the cost of steel beams, and the price of steel wire and wire rods can influence the overall budget of a construction project.
Bolted joints: the cost of bolts and the labour required for installation must be considered. While the initial cost may be lower due to more straightforward installation, maintenance costs could rise if bolts need frequent tightening or replacement.
Welded joints: welding typically incurs higher labour costs due to the need for skilled workers and specialised equipment. However, welded joints often lead to longer-lasting connections with lower maintenance needs, which can offset the higher initial cost.
Buy online
Mild SteelStainless SteelStructural SteelTMTCementJSW One MSME
About usBlogsSitemapJSW One TMTPolicy
Terms & conditionsPrivacy policyReturn policy