Structural steel stands out when constructing long-lasting buildings due to its strength, ductility and versatility. However, the rainy season can significantly threaten steel structures, as increased moisture levels accelerate corrosion. In this blog, we'll explore ways steel beams, columns, and other structural elements are protected against corrosion.
Understanding structural steel
Structural steel is known for its high strength-to-weight ratio and flexibility in design. It is commonly used in the form of steel beams, channels and angles, I-beams, and columns to create the framework of buildings. An I-section beam, also known as an I-beam, is one of the most prevalent shapes used in steel structures due to its efficiency in bearing loads.
Types of columns in steel structures
Columns: these are critical vertical elements in steel structures, providing essential support to transfer loads from the beams to the foundations. The main types of columns include:
Hollow Structural Sections (HSS): these are often square, rectangular, or circular in cross-section in the form of hollow tubes and are known for their high strength and aesthetic appeal.
Strategies and materials for rainy season corrosion in structural steel
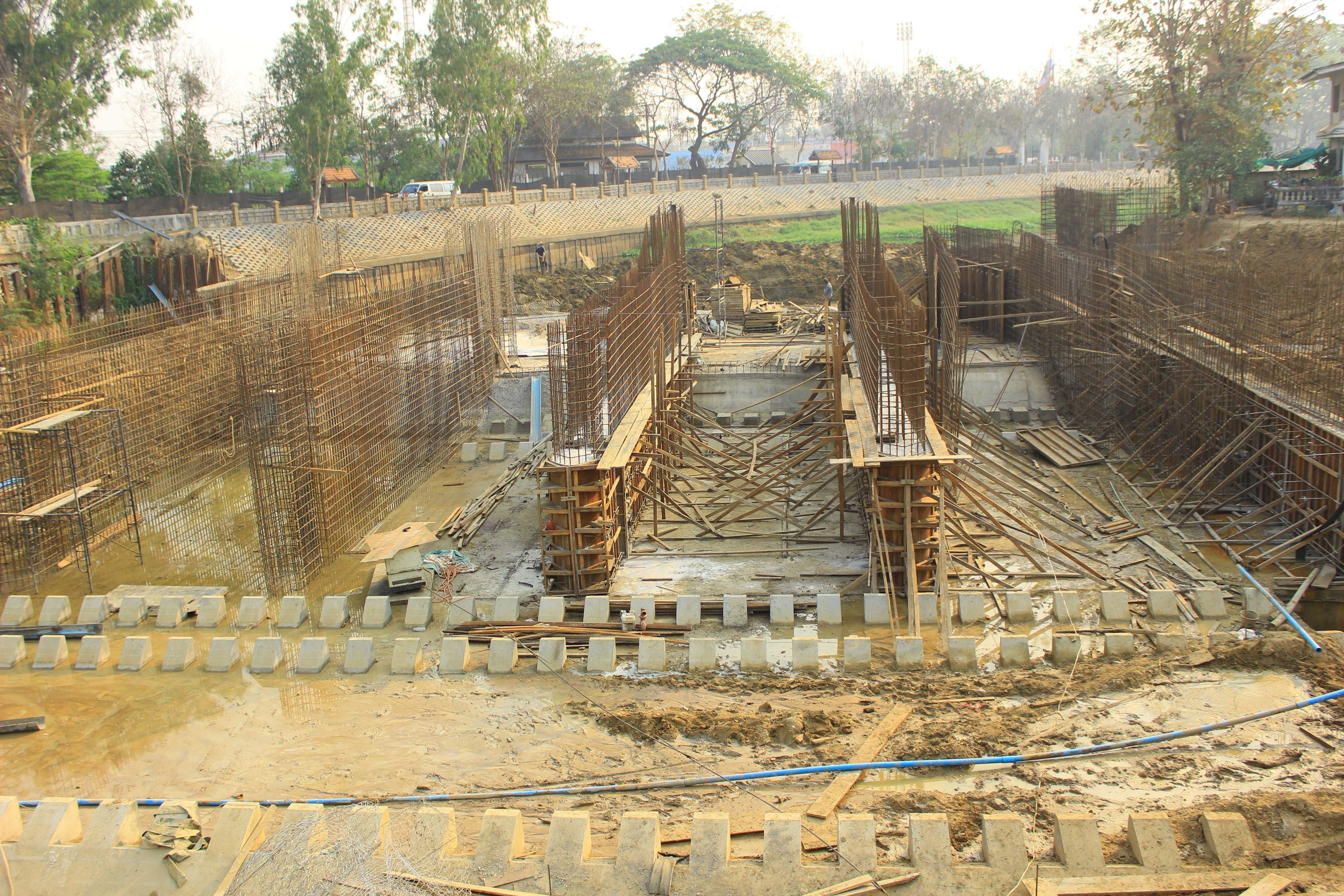
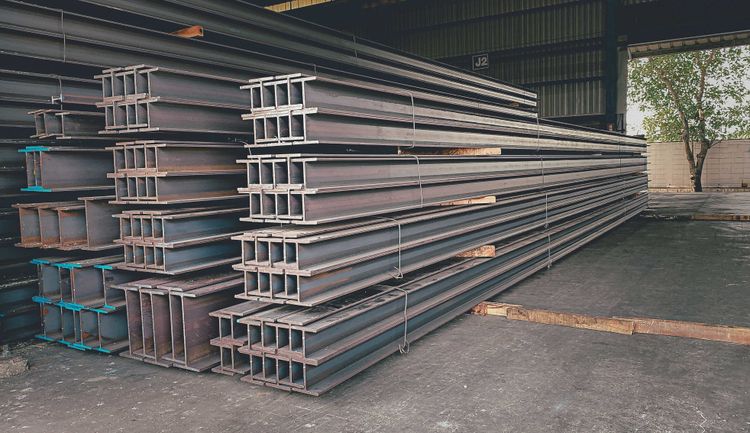
Wide flange columns (W-columns): like I-beams, W-columns have parallel flanges, providing excellent load-bearing capacity.
Built-up columns: made by welding or bolting multiple steel plates, these columns can be customised for specific structural requirements.
The challenge of corrosion
Corrosion is the gradual degradation of materials, usually metals, due to chemical reactions with their environment. In steel's case, exposure to moisture and oxygen leads to iron oxide, commonly known as rust. During the rainy season, the high humidity and persistent wet conditions can significantly speed up this process, compromising the structural integrity of steel elements.
Atmospheric corrosion
Atmospheric corrosion occurs when steel is exposed to the natural atmosphere, including varying humidity levels, temperature, and pollutants. The primary factors affecting atmospheric corrosion are:
- Humidity: high humidity levels can accelerate corrosion by providing moisture necessary for electrochemical reactions.
- Temperature: higher temperatures generally increase the rate of corrosion.
- Pollutants: industrial pollutants such as chlorides, sulfur dioxide (SO2) and nitrogen oxidesolor (NO) can form acidic compounds when combined with moisture, significantly accelerating corrosion.
Prevention measures
- Applying protective coatings such as paints, galvanisation, or other corrosion-resistant coatings.
- Using corrosion inhibitors.
- Implementing regular maintenance and inspections.
2. Galvanic corrosion
Galvanic corrosion occurs when two metals or alloys are electrically connected to an electrolyte (e.g., water). The more anodic (less noble) metal corrodes preferentially to the more cathodic (noble) metal. Key factors include:
- Electrochemical potential difference: the more significant the difference in the electrode potential of the two metals, the higher the risk of galvanic corrosion.
- Electrical conductivity: the presence of a conductive path for the flow of electrons.
- Electrolyte presence: typically water with dissolved salts, acids, or alkalis.
Prevention measures
- Avoiding dissimilar metal contacts.
- Applying insulating materials between different metals.
- Using sacrificial anodes to protect the more valuable metal.
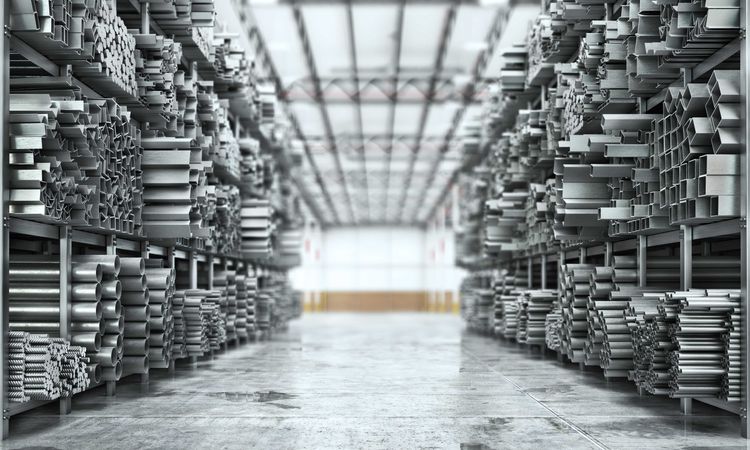
3. Crevice corrosion
Crevice corrosion occurs in confined spaces where stagnant solutions can become trapped, such as under gaskets, washers, or fasteners. Factors influencing crevice corrosion include:
Oxygen depletion: limited oxygen in the crevice compared to the surrounding area can lead to differential aeration, causing localised corrosion.
Acidic conditions: accumulation of acidic by-products within the crevice.
Concentration of corrosive species: higher concentration of chlorides or other aggressive ions within the crevice.
Prevention measures
Designing joints and assemblies to avoid crevices by avoiding very sharp corners.
Sealing joints to prevent the ingression of corrosiand ve solutions.
Using corrosion-resistant materials.
4. Pitting corrosion
Pitting corrosion is a localised form of corrosion that forms small holes or pits in the metal. It is particularly insidious because it can cause rapid penetration of the metal while the overall corrosion rate may appear low. Influencing factors include:
Presence of chloride ions: chlorides are highly aggressive and can disrupt the passive film on metals, leading to pitting.
Metal composition: certain alloying elements such as Mo, N, and Cr can increase resistance to pitting.
Environmental conditions: temperature, PH, and other factors can influence pitting propensity.
Prevention measures
Using high-alloy steels with good pitting resistance, such as stainless steel with higher chromium and molybdenum content.
Maintaining clean surfaces and avoiding stagnant conditions.
Applying protective coatings and cathodic protection such as galvanised or galvalume coatings.
Methods to enhance corrosion resistance
To protect steel structures from corrosion, especially during the rainy season, several methods can be employed:
Protective coatings
Paints and epoxy coatings: applying a layer of paint or epoxy resin creates a barrier that prevents moisture and oxygen from reaching the steel surface.
Galvanisation: this process involves coating steel with a layer of zinc, which acts as a sacrificial anode, corroding in place of the steel.
Corrosion inhibitors
Chemical compounds can be added to the environment surrounding the steel, reducing the corrosion rate. These inhibitors can be mixed with concrete or applied as a spray.
How corrosion inhibitors work
Corrosion inhibitors interact with the metal surface to form a protective film. There are three types of these films:
Passivating film: these are thin, oxide films (30–200 å thick) that provide excellent protection. Examples include chromates and nitrites, though they are less used today due to toxicity concerns, except in critical areas like aerospace and construction. Other examples like tungstates and molybdates work in the presence of air.
Precipitation film: these inhibitors react with soluble species in the environment or with the metal to form a protective layer. For example, phosphonates and polyphosphates form films with calcium ions, while copper-benzotriazole forms a film with copper ions. These films might be porous and not perfectly adherent, but still offer decent protection.
Adsorption film: these inhibitors are usually organic molecules that attach to the metal surface. They have a part that bonds with the metal and a part that sticks out into the solution, reducing the metal's contact with oxygen and water, thus slowing down corrosion.
Proper design and maintenance
Ensuring that steel structures are designed with proper drainage and ventilation can minimise water retention and reduce the risk of corrosion. Regular maintenance, such as inspecting and repairing protective coatings, is also essential. Cleaning and disposal of corrosion products, if any by some mechanical or chemical means can also minimize further corrosion.
Role of structural steel fabricators
Structural steel fabricators play a crucial role in the construction process, from designing and creating steel components to implementing corrosion protection measures. Experienced fabricators understand the importance of selecting suitable materials and protective methods to ensure the durability and safety of steel structures, especially in environments.
Conclusion
Corrosion resistance in structural steel is critical for any construction project, particularly during the rainy season. By understanding the various methods and materials available to protect steel from corrosion and collaborating with skilled structural steel fabricators, you can ensure the longevity and integrity of your steel structure building.
Buy online
Mild SteelStainless SteelStructural SteelTMTCementJSW One MSME
About usBlogsSitemapJSW One TMTPolicy
Terms & conditionsPrivacy policyReturn policyBanking partner