Optimising microstructure in hot rolled steel for springs
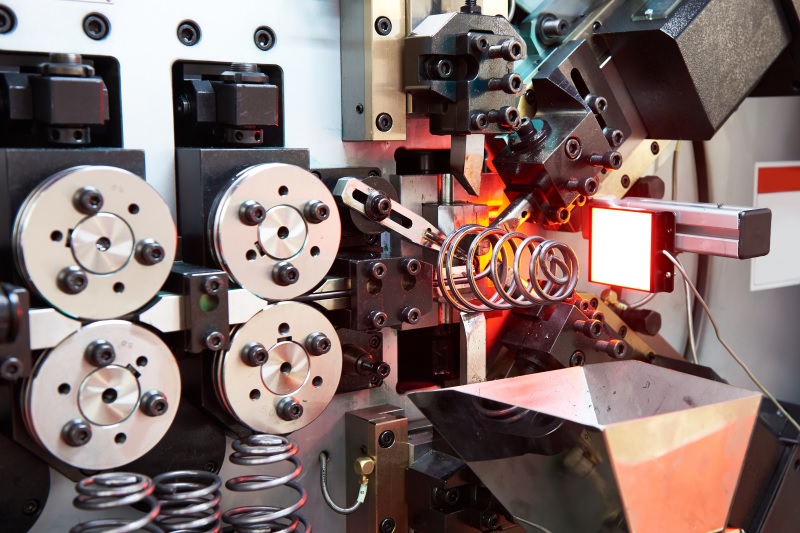
Precision springs are used in various industries - from automotive and aerospace to electronics and healthcare. They are crucial in ensuring proper functionality and safety in devices as diverse as suspension systems, medical instruments, and precision machinery. Precision springs operate under stringent conditions, requiring specific mechanical properties to perform their intended functions effectively. Factors like tensile strength, yield strength, and fatigue resistance must be carefully controlled to ensure the spring can endure repeated compression and expansion cycles without failure. Microstructure optimisation is vital in precision springs when using hot-rolled steel. Through precise temperature and cooling control during the hot rolling process, manufacturers can manipulate the grain size, distribution, and orientation within the steel. Mechanical properties relevant to precision springs Elasticity and spring constant: Elasticity is the ability of a material to deform reversibly under an applied load and return to its original shape when the load is removed. In precision springs, elasticity is paramount as springs must be able to repeatedly deform and then return to their initial state without permanent deformation.
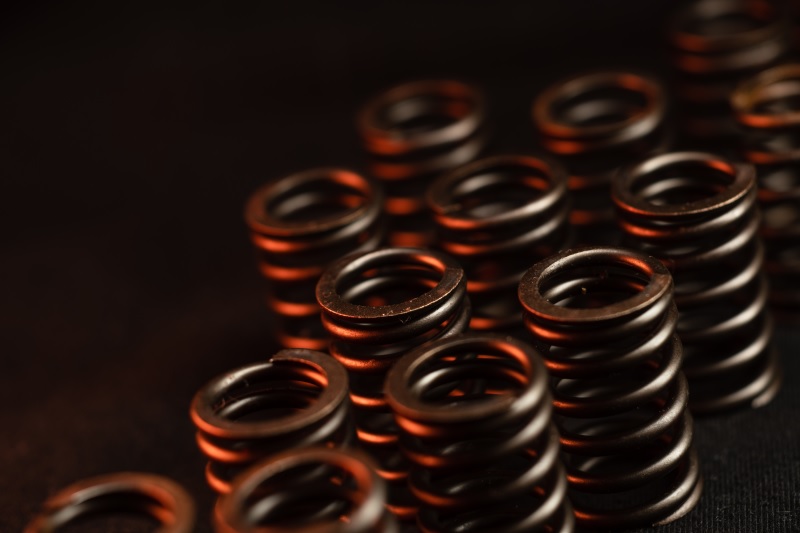
The spring constant (or stiffness) measures how stiff or flexible a spring is. It determines the relationship between the force applied to the spring and the resulting displacement. High spring constants indicate stiff springs, while low values suggest flexible ones. Strength and toughness: Strength refers to a material's ability to withstand an applied force without failing. High strength is essential in precision springs, especially those subject to high loads to prevent permanent deformation or failure. Toughness is the ability of a material to absorb energy and deform plastically before fracturing. Toughness is crucial for preventing brittle fracture, especially in applications with dynamic loading. Fatigue resistance: Fatigue resistance is a critical property for precision springs subjected to cyclic loading. Springs must resist fatigue failure, which occurs when repeated cyclic stresses lead to cracks and eventual fractures. Fatigue resistance is assessed through fatigue testing, which involves subjecting the spring to cyclic loading until failure. Springs with high fatigue resistance have longer lifespans in service. The relationship between microstructure and mechanical properties
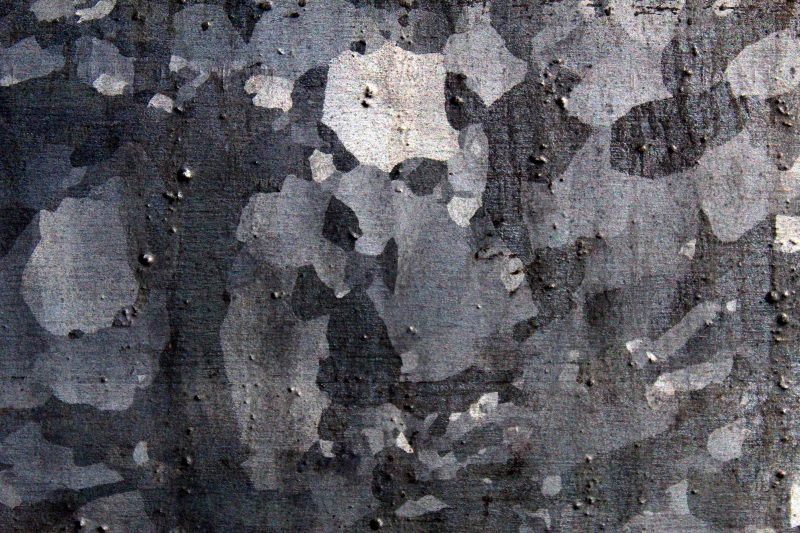
Grain size: Smaller grains tend to result in improved strength and toughness, as well as enhanced fatigue resistance. Phase composition: Specific phases, like martensite or austenite, can enhance strength or toughness, depending on the application. Inclusions and defects: Impurities, inclusions, or defects can weaken the material, reducing its mechanical properties. Importance of precision in mechanical properties for spring applications Consistent performance: Springs are designed to operate within specific force-displacement ranges. Precise mechanical properties ensure consistent performance across a batch of springs. Safety: In applications where springs play a critical role, such as in automotive suspensions or medical devices, deviations in mechanical properties can lead to safety hazards or malfunctions. Predictable behaviour: Precision springs are often used in mechanisms where their behaviour must be highly predictable. Deviations in stiffness or fatigue resistance can lead to unexpected outcomes.
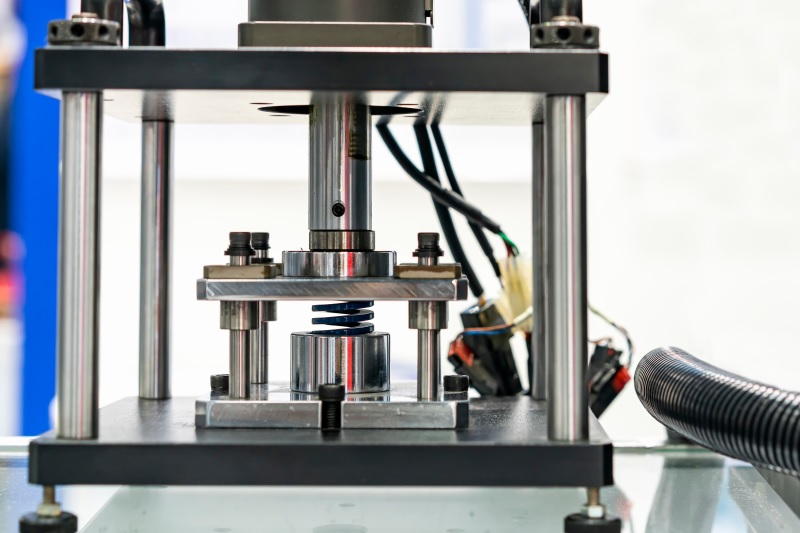
Longevity: Precision springs are expected to have long lifespans. Precise control over mechanical properties can extend the service life of these components. Factors influencing microstructure in hot-rolled steel Temperature and cooling rate during hot rolling Hot Rolling temperature: The temperature at which steel is rolled significantly affects its microstructure. Higher rolling temperatures produce finer grains and a more uniform microstructure, while lower temperatures result in coarser grains. The choice of rolling temperature depends on the desired properties and end-use of the steel product. Cooling rate: After hot rolling, the cooling rate also impacts the microstructure. Faster cooling rates, achieved through water quenching, promote the formation of a fine-grained structure with improved mechanical properties, including strength and toughness. Slower cooling rates can produce coarser grains. Alloy composition and its impact on microstructure: Alloying elements: The composition of steel alloys plays a significant role in determining its microstructure. Different alloying elements, such as carbon, manganese, silicon, and various trace elements, influence the formation of phases within the steel. Carbon content, for instance, affects hardness and strength, while other alloying elements can enhance corrosion resistance, ductility, and other properties. Phase transformations: Alloy composition affects the phase transformations that occur during cooling. For example, adding alloying elements like chromium or nickel can promote the formation of specific phases, such as martensite or austenite, which have distinct microstructures and mechanical properties. Heat treatment methods
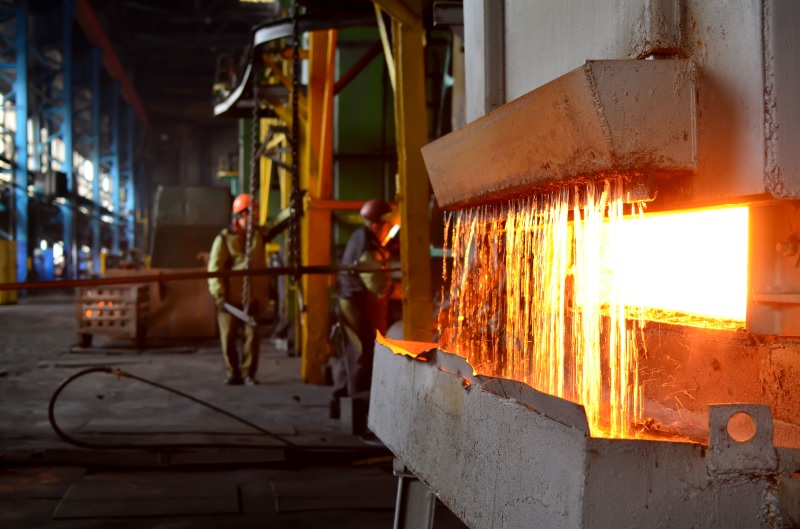
Annealing: It involves heating the steel to a specific temperature and then slowly cooling it to achieve the desired properties. This process can refine the grain structure, relieve internal stresses, and enhance ductility. Quenching and tempering: Quenching (rapid cooling) and tempering (subsequent controlled heating under critical temperature) are employed to achieve specific microstructures and mechanical properties for certain applications. Quenching can result in a hardened microstructure, while tempering can improve toughness and reduce brittleness. Mechanical working and deformation
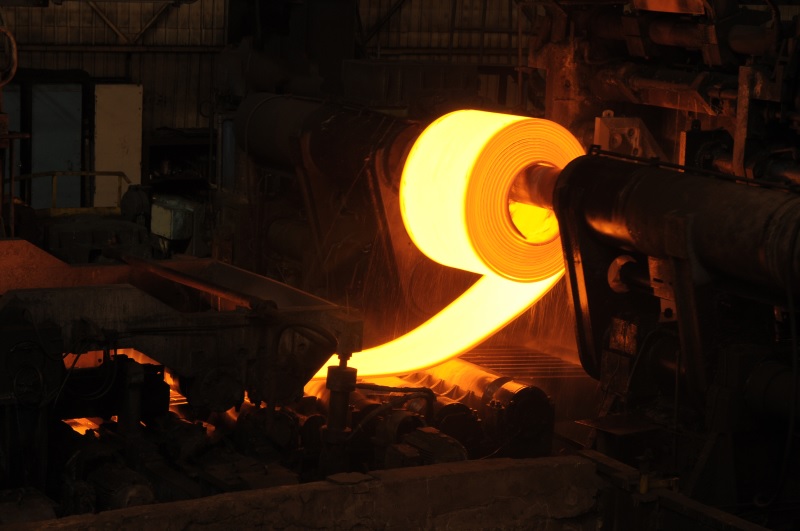
Rolling process: The amount of deformation, rolling speed, and the number of rolling passes influence grain size and shape. Proper control of these parameters is essential for achieving desired microstructures. Forging and extrusion: Besides hot rolling, other mechanical working processes like forging and extrusion can further refine the microstructure of steel. These processes involve shaping the steel under high pressure and temperature conditions, resulting in grain size and orientation changes. Role of impurities and inclusions: Impurities: Sulphur and phosphorus, can negatively affect steel microstructure. These impurities can lead to the formation of undesirable phases and inclusions, which can weaken the material. Strict quality control measures are necessary to minimise contaminants. Inclusions: Inclusions are non-metallic particles or substances found in steel. Their size, shape, and distribution can influence the microstructure and mechanical properties. Inclusions can act as stress concentrators, reducing the material's strength and fatigue resistance.
Buy online
Mild SteelStainless SteelStructural SteelWelding consumablesTMTCementJSW One MSME
About usBlogsSitemapJSW One TMTPolicy
Terms & conditionsPrivacy policyReturn policy