How to enhance the durability of fasteners using steel coatings?

Steel fasteners are critical components in various industrial, construction, and manufacturing applications, providing essential structural integrity and strength. However, they are often subjected to harsh environmental conditions that can lead to corrosion and degradation over time. Applying the appropriate coatings is crucial to mitigate these effects and enhance the durability of steel fasteners. This blog provides a technical overview of how steel coatings improve fastener longevity and offers detailed guidance on selecting and using the most effective coatings. Understanding the importance of coatings for steel fasteners Despite its strength, steel is inherently susceptible to corrosion, especially when exposed to moisture, salts, chemicals, and other corrosive agents. Corrosion can significantly compromise the mechanical properties of fasteners, leading to failures that might endanger structural integrity. Coatings act as a protective barrier, shielding the steel substrate from corrosive elements, thereby prolonging the service life of the fasteners.
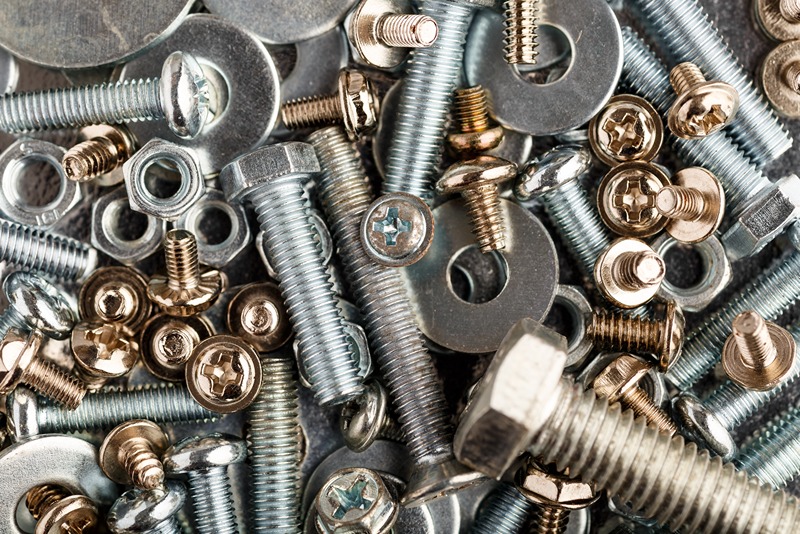
Types of coatings for enhanced durability Different coatings provide varying levels of protection depending on their chemical composition and application process. Here are some of the most used coatings for steel fasteners, along with their technical attributes: Zinc coating (galvanisation): Hot-dip galvanising: this process involves immersing steel fasteners into molten zinc at approximately 450°c. The zinc reacts with the steel to form a series of zinc-iron alloy layers topped with pure zinc, creating a thick, durable coating. Hot-dip galvanising provides cathodic protection, meaning the zinc coating sacrifices itself to protect the underlying steel, making it ideal for outdoor and marine environments where high corrosion resistance is required. Electro-galvanising: zinc is deposited onto the steel fastener using an electric current in this electrochemical process. This method produces a thinner, more uniform coating compared to hot-dip galvanising. Electro-galvanised coatings are less corrosion-resistant but offer a smoother surface finish, making them suitable for applications with moderate exposure to corrosive elements. Phosphate coating: Zinc phosphate: this coating is applied through a chemical reaction between the steel substrate and a zinc-containing phosphoric acid solution. The result is a crystalline layer of zinc phosphate that provides a good base for subsequent painting or lubrication and improves corrosion resistance in moderate environments. Manganese phosphate: similar to zinc phosphate but involving manganese, this coating produces a thicker, denser layer that is highly resistant to wear. Manganese phosphate coatings are ideal for high-friction applications requiring additional wear resistance. PTFE coating (polytetrafluoroethylene): PTFE coatings, known for their low friction and excellent chemical resistance, are applied through spraying and curing. The coating provides a non-reactive barrier that is particularly effective against aggressive chemicals and extreme temperatures. PTFE is suitable for fasteners in chemical processing plants and other corrosive environments. Epoxy coating: Epoxy coatings are created by mixing epoxy resins with hardening agents and applying them to fasteners. Once cured, the epoxy forms a hard, durable layer that offers excellent moisture, chemicals, and mechanical wear resistance. These coatings are well-suited for industrial applications where high durability and corrosion resistance are paramount. Powder coating: This dry-finishing process involves applying a thermoplastic or thermoset powder to the fasteners, which is then cured under heat to form a hard, durable finish. Powder coatings provide excellent resistance to chipping, scratching, and fading, making them ideal for functional and aesthetic applications.
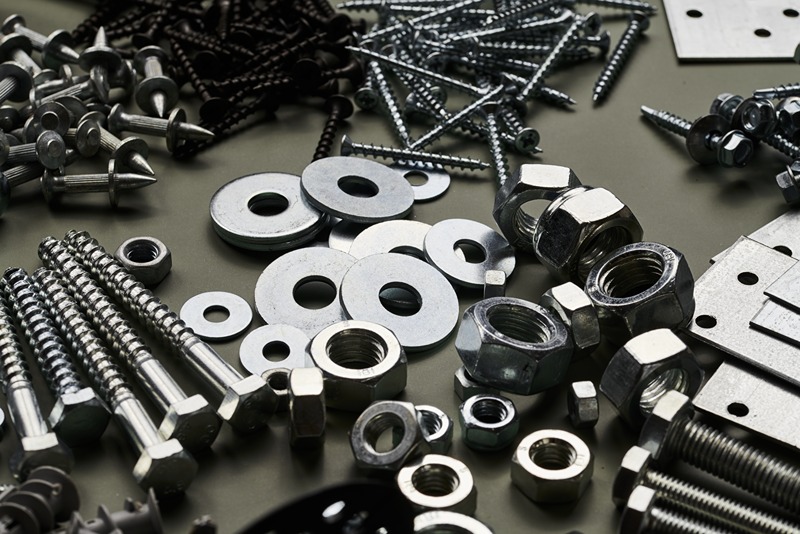
Selecting the appropriate coating Choosing the right coating for steel fasteners requires a thorough understanding of the operational environment and the specific demands of the application. Here are the technical factors to consider: Environmental exposure: assess the type and level of exposure the fasteners will face, including humidity, salt, chemicals, and UV radiation. For example, marine environments require robust coatings like hot-dip galvanising due to the high salt content and moisture levels. Mechanical stress: consider the mechanical loads and stresses the fasteners will endure. Fasteners subjected to high friction or stress, such as those in automotive or heavy machinery applications, may benefit from harder coatings like manganese phosphate or epoxy. Thermal conditions: evaluate the fasteners' temperature range. Coatings like PTFE are suitable for high-temperature applications due to their thermal stability, while zinc coatings are limited by their melting point (around 419°c). Chemical resistance: determine the fasteners' chemical exposure. PTFE or epoxy coatings provide superior resistance for environments with frequent contact with corrosive chemicals. Best practices for applying coatings The application process significantly influences the performance of a coating. Here are technical guidelines to ensure optimal coating application: Surface preparation: Proper surface preparation is crucial for coating adhesion and longevity. Techniques such as abrasive blasting, acid pickling, or alkaline cleaning may remove oxides, oils, and contaminants from the steel surface, ensuring a clean substrate for coating.
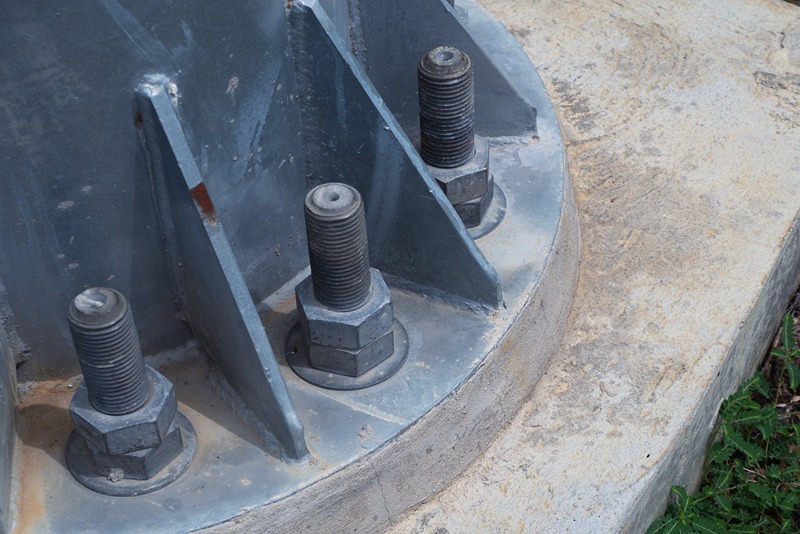
Coating application: The choice of application method depends on the coating type. For instance, hot-dip galvanising involves immersion in molten zinc, while electro-galvanising requires an electroplating setup. Spraying techniques are used for PTFE and powder coatings, requiring careful control of application parameters to achieve uniform coverage. Curing process: Curing is essential for developing the coating's final properties. For epoxy and powder coatings, this typically involves heating the coated fasteners to a specified temperature to initiate a chemical reaction that forms a durable finish. The curing temperature and time must be precisely controlled to prevent defects such as blistering or incomplete curing. Quality assurance: Implement rigorous quality control measures to verify coating thickness, adhesion, and uniformity. Non-destructive testing methods, such as ultrasonic thickness gauges or magnetic induction, can be employed to ensure compliance with specifications. Conclusion Applying the right coatings to steel fasteners is a technical process that significantly enhances their durability and performance in various environments. By understanding your application's specific requirements and selecting the appropriate coatings and application methods, you can ensure long-lasting protection against corrosion and wear. At JSW One MSME, we offer a range of high-quality steel products and coatings tailored to meet your project needs, providing reliable solutions that enhance the longevity and reliability of your fasteners.
Buy online
Mild SteelStainless SteelStructural SteelTMTCementJSW One MSME
About usBlogsSitemapJSW One TMTPolicy
Terms & conditionsPrivacy policyReturn policy