How market volatility affects steel prices, and what that means for order quantities
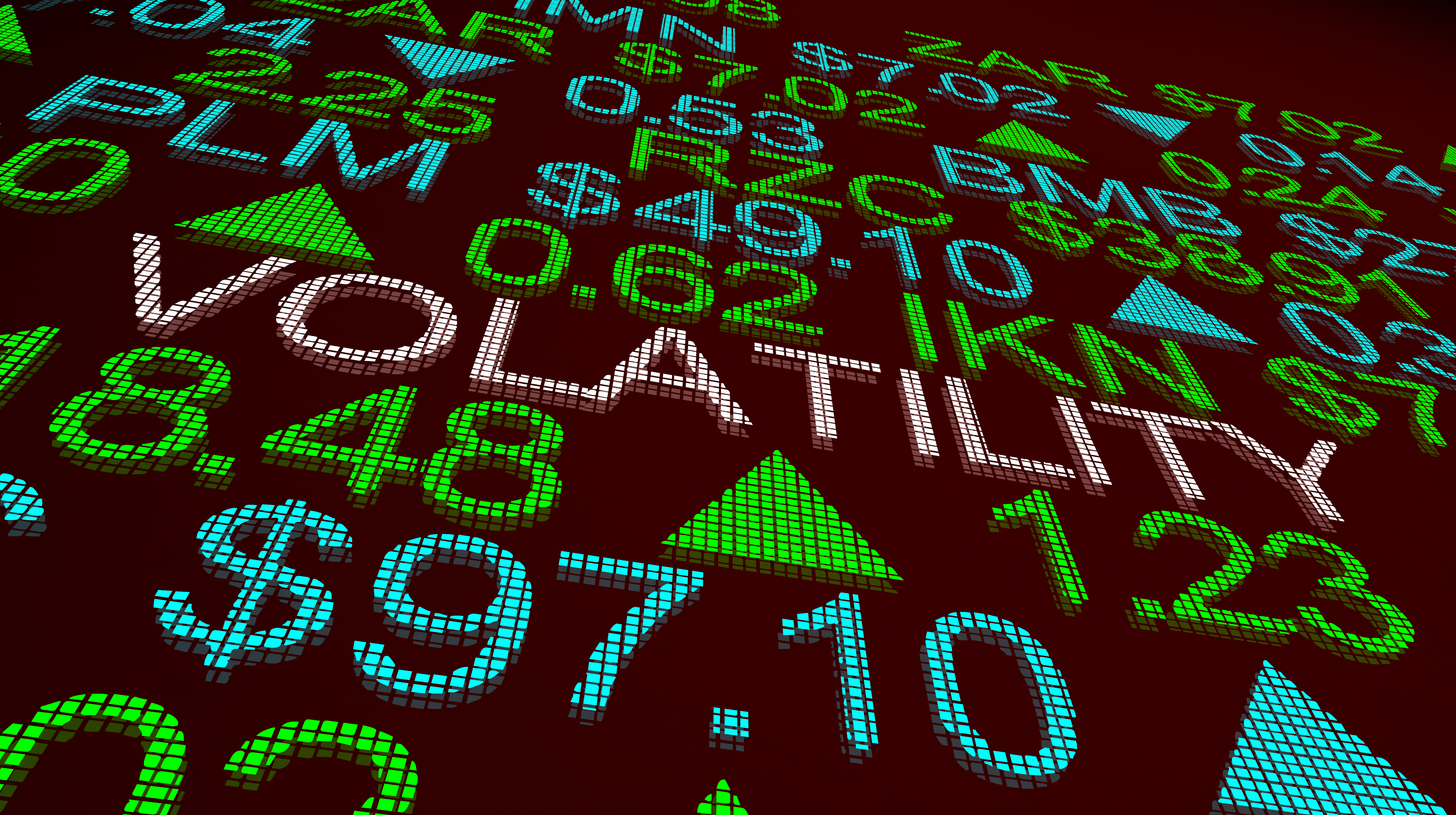
Across the past two years, markets across industries have suffered from volatility spurred by slow output and rising demand. Steel is no stranger to fluctuating market conditions, and many worry about the likelihood of an unstable market, where demand and price fall and suppliers are left with a lot of steel and no one to buy it. Major geopolitical events impact the steel demand and how it will be used, which in turn affects the prices of steel. For example, infrastructure slowdown limit the construction in a country, reducing the demand of certain steel products, and hence the prices are likely to go down. This up-and-down value of goods and commodities during a specific period is precisely termed "market volatility." Market volatility is measured by the day-to-day difference in the prices of these goods and commodities. Since prices are determined by demand and supply, volatility is also the function of the market's underlying demand and supply characteristics. Volatility-causing changes are frequently abrupt and unanticipated, and they are commonly triggered by more important occurrences like pandemics, wars, recessions, inflation, and policies, to mention a few.
How does that affect order quantities?
Steel demand varies in response to steel price fluctuations driven by big geopolitical events. For example, we witnessed extreme volatility in steel prices due to soaring inflation in the US, COVID-induced supply chain bottlenecks and the Russia-Ukraine war.
Prices usually decrease when demand decreases and vice versa. This typically results in either a surplus or a shortage of material with suppliers or in mills. Concern among steel mills and suppliers increases when purchasing demand decreases. The safer option for the buyers in such cases is maintaining a minimum order quantity, which enables them to hedge against the ,risk arising out of price fluctuations, while ensuring productivity levels
What is the minimum order quantity?
MOQ or minimum order quantity is the minimum amount of product that a manufacturer will allow his customer to purchase. MOQ protects the buyers from the unnecessary cost of storage, more so if the steel requires specific maintenance or care. While many businesses actively manage their financial and delivery risks and recognise that the unpredictability of raw materials is a critical factor, only some do it in a systematic, structured manner. Maintaining an MOQ has the following benefits: -
MOQ or minimum order quantity is the minimum amount of product that a manufacturer will allow his customer to purchase. MOQ protects the buyers from the unnecessary cost of storage, more so if the steel requires specific maintenance or care. While many businesses actively manage their financial and delivery risks and recognise that the unpredictability of raw materials is a critical factor, only some do it in a systematic, structured manner. Maintaining an MOQ has the following benefits: -
1. Healthier cash flow: - By establishing a MOQ, manufacturers can ensure that their cash is not being taken captive in large quantities of raw materials while progressively releasing finished goods in little quantities.
2. Lower inventory:- A well-designed MOQ can assist reduce inventory because most manufacturers produce more than one kind of product or product category. Companies can maintain lower total costs for finished items and raw materials by setting a smaller MOQ. This lowers the inventory level by releasing cash and lowering holding expenses.
3. Higher profits - Demand and MOQ are interrelated. This implies that even though a business may establish a lower MOQ, they know that production will occur in bigger volumes later on in the cycle. This necessitates striking a balance between inventory holding costs and demand in order to give the lowest viable price on smaller lots. By striking this balance, a business can make a higher profit while satisfying customers who want to buy minimum quantities, by producing larger quantities throughout the cycle due to known demand and forecasts.
Three significant issues may hamper businesses:
Lack of market understanding - When we consider market understanding, we don't suggest successfully forecasting fluctuations in the price of raw materials, but rather a fundamental understanding of market dynamics and great insight into market information. Market data often needs to be adequately examined, and the underlying drivers of market dynamics are not tracked. As a result, organisations lose critical response time and are caught off guard.
Lack of oversight regarding the scope of risk exposure - Most businesses need more visibility into the risk associated with the direct raw materials they purchase for subsequent processing. This awareness, however, rapidly impairs when it comes to the materials they indirectly purchase through vendors. Additionally, it might be challenging to predict the timing of the impact because changes in raw material prices often need to catch up in their influence on the bottom line.
Lack of understanding about how to manage the exposure of raw material - It is not unusual that most businesses lack knowledge of the appropriate measures to handle the movement of raw materials because they also lack a thorough understanding of the market dynamics and their actual raw material risk exposure.
How to mitigate this risk?
A thorough understanding of the market dynamics is necessary for any raw materials strategy to be effective. The following activities are crucial:
Recognise the fundamental pricing determinants - Various factors, including supply and demand and changes in the underlying feedstock, can affect the price of raw materials. Understanding the most important aspects and what changes in these variables affect prices is crucial.
Obtain relevant information to track prices - The best way to avoid surprises is to keep an eye on market reports for derivatives, feedstock materials, and raw commodities. When price movements become more apparent, you can predict them or, at the very least, be ready to react quickly.
Create transparency - Transparency on expected changes in the price of raw materials not only forms the cornerstone of any mitigation attempt but also enables a much more professional, fact-based budgeting process.
4. Inventory planning and management to hedge against material unavailability in volatile market conditions lead to safeguards against production time losses and productivity drops.
5. Opportunity costs: A volatile market is also a good time for alert businesses to time the market and makes windfall profits by buying above MOQ or Inventory levels to level off against expected price hikes as production slows or availability dips
While there is no fool-proof method to prevent your business from the market volatility that the steel industry experiences, The market volatility that the steel industry experiences is manageable for businesses that keenly observe macro economic indicators and observe market behaviour closely. However, you can exercise control over the inventory by purchasing from suppliers like JSW One MSME, who can provide you with exact quantities that meet your specifications. If you require a high or low-volume order for your steel needs, reach out to us for a quick quote.
No blogs found
Buy online
Mild SteelStainless SteelStructural SteelWelding consumablesTMTCementJSW One MSME
About usBlogsSitemapJSW One TMTPolicy
Terms & conditionsPrivacy policyReturn policy