Galvanized steel: An indispensable material for the future of the automotive industry
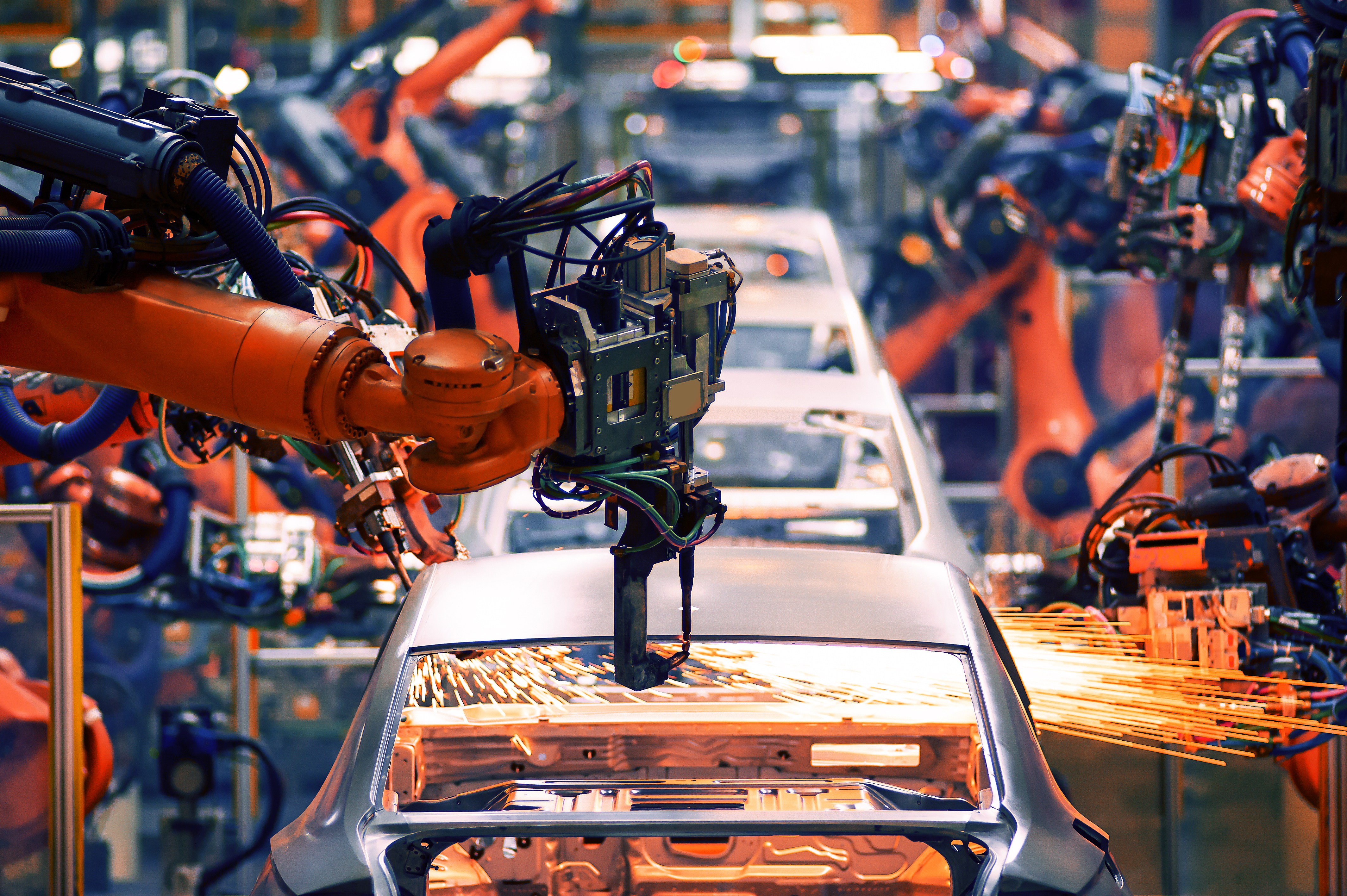
With a valuation of over $100 billion and an annual production of 23 million units, the Indian automotive industry is the fourth-largest in the world and is set to climb to the 3rd spot by 2025. It accounts for 2.3% of India’s total GDP.
A key factor in the development of the sector has been India’s domestic steel output, currently second only to China by production volume. The automotive industry is among the largest consumers of steel, with over 9% of the total annual steel production used in automobile manufacturing. For automotive MSMEs, steel offers the perfect combination of attributes - high tensile strength, low specific weight, and high manufacturability.
Among the different types of steel available to the industry, galvanized steel stands out as an excellent choice, offering a good balance between material properties, surface finish, and shelf-life. But what is galvanized steel, and how does it differ from other types of steel?
What is Galvanized Steel?
Galvanized steel is a type of steel that has been coated with zinc. The exposed zinc coat acts as a protective sheath that prevents the steel from rusting and corrosion. This helps to extend the lifespan of the underlying metal, while reducing the rate of deterioration, resulting in significantly lowered maintenance costs. The zinc coating sacrifices itself to protect the metal underneath.
It is one of the most widely used steels in manufacturing due to its versatility, resistance to corrosion, durability, and low capital investment. It's also an easy material to work with.
In the auto industry, galvanized steel has been in use since the early 1900s, and is still used today to make car bodies, doors, and hoods. In the last few decades, innovations in the industry have resulted in the use of galvanized steel (together with AHSS) in auto components as well, making it the staple material for European and US automotive industries.
Two major types of galvanized steel are utilized in the auto industry: hot-dipped galvanized steel and electro-galvanized steel. These two types of galvanized steel differ only in the method used to apply the zinc coating. While hot-dipped GS is produced by dipping steel in molten zinc in a furnace, electro galvanization involves passing an electric current through a zinc anode and steel conductor.
Let’s now take a look at the benefits of galvanized steel in automobile manufacturing.
Galvanized steel - Benefits over other materials used in automobiles
Galvanized steel is easy to work with and can be fabricated into various shapes without losing its quality or strength. This makes it a good material for car manufacturing, which calls for intensive forming and processing of sheet metal.
When used in bulk, galvanized steel is less expensive compared to other advanced, corrosion-resistant steels.
It is much more durable than normal steel, thus requiring less maintenance. Compared to conventional steel, which has a lifespan of 20-25 years, galvanized steel can last 40-50 years.
The tough zinc coating provides high resistance to mechanical damage in transport, vibrations, and extreme weather conditions. This makes it ideal for use in cars that are constantly exposed to the elements like rain and snow.
Compared to other processed steel products, steel galvanization is well understood and has a long history, making it faster to produce and easier to use in forming processes.
Galvanized steel retains its lustre and good surface finish after long-term use,
Galvanized steel has excellent toughness and strength, significantly higher than uncoated steel varieties.
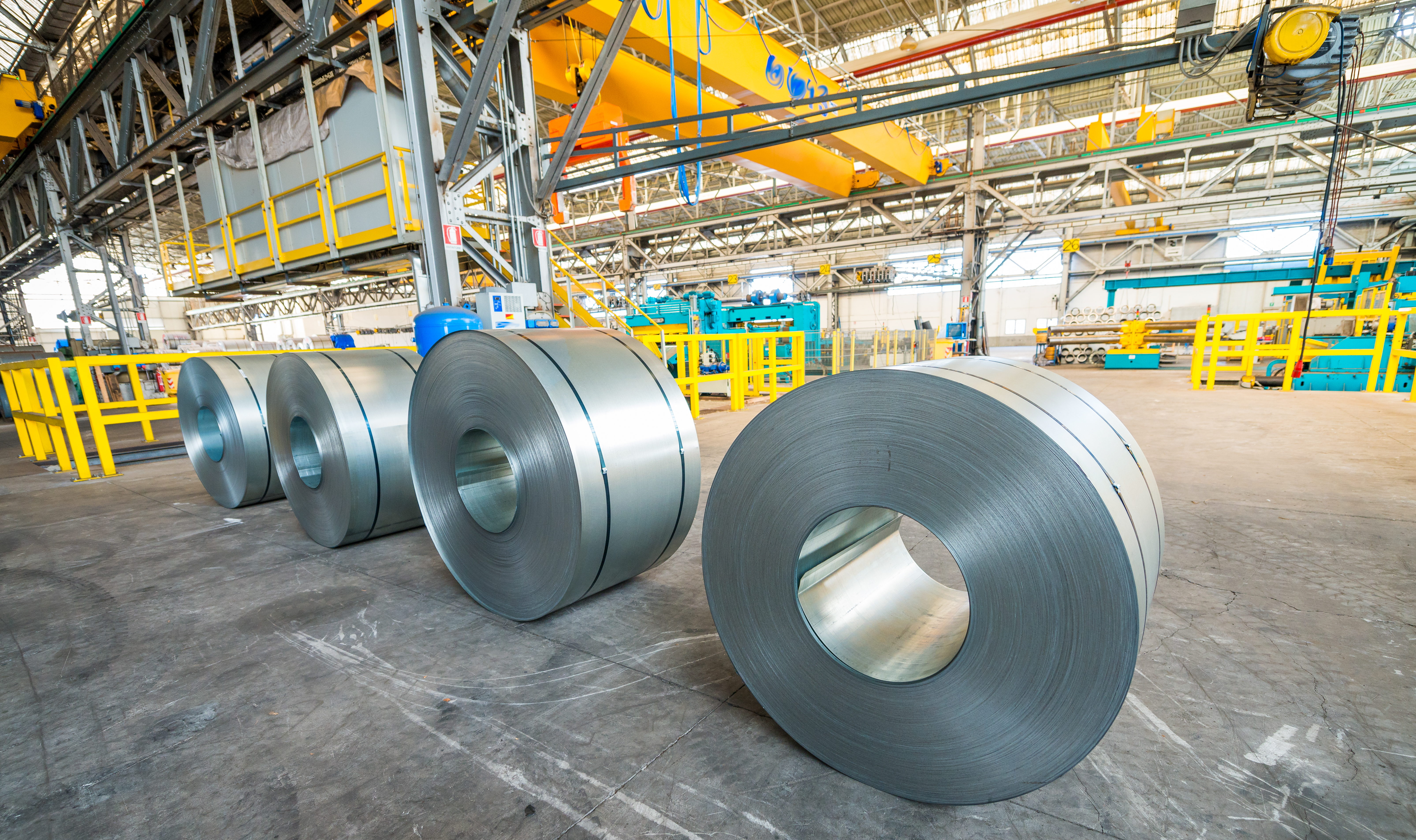
Is India lagging in the use of galvanized steel in cars?
Despite its popularity, galvanized steel is used in less than 30% of cars produced in India (depending on the brand), compared to 70% in the EU and the US.
The reason for this large gap between global and Indian averages is that the cost of galvanizing is higher in India than in other countries. This means that when MSMEs/companies look at their costs, they will have to take into account not only the cost of raw materials but also the cost of processing them into usable products. This is why 95% of cars sold in India do not provide any anti-corrosion or anti-perforation warranties, which are considered hygiene offerings elsewhere.
Due to the low use of GS in BIW (body in white) design, studies indicate that vehicles produced in India are more prone to corrosion, posing a safety hazard to drivers’ safety, and adding to car maintenance costs.
In 2018, IIT Bombay conducted a car quality survey in Mumbai and Chennai, with a sample of 500 cars across brands manufactured between 2000 and 2017. The cars were checked for rusting on their various components, and for general wear and tear.
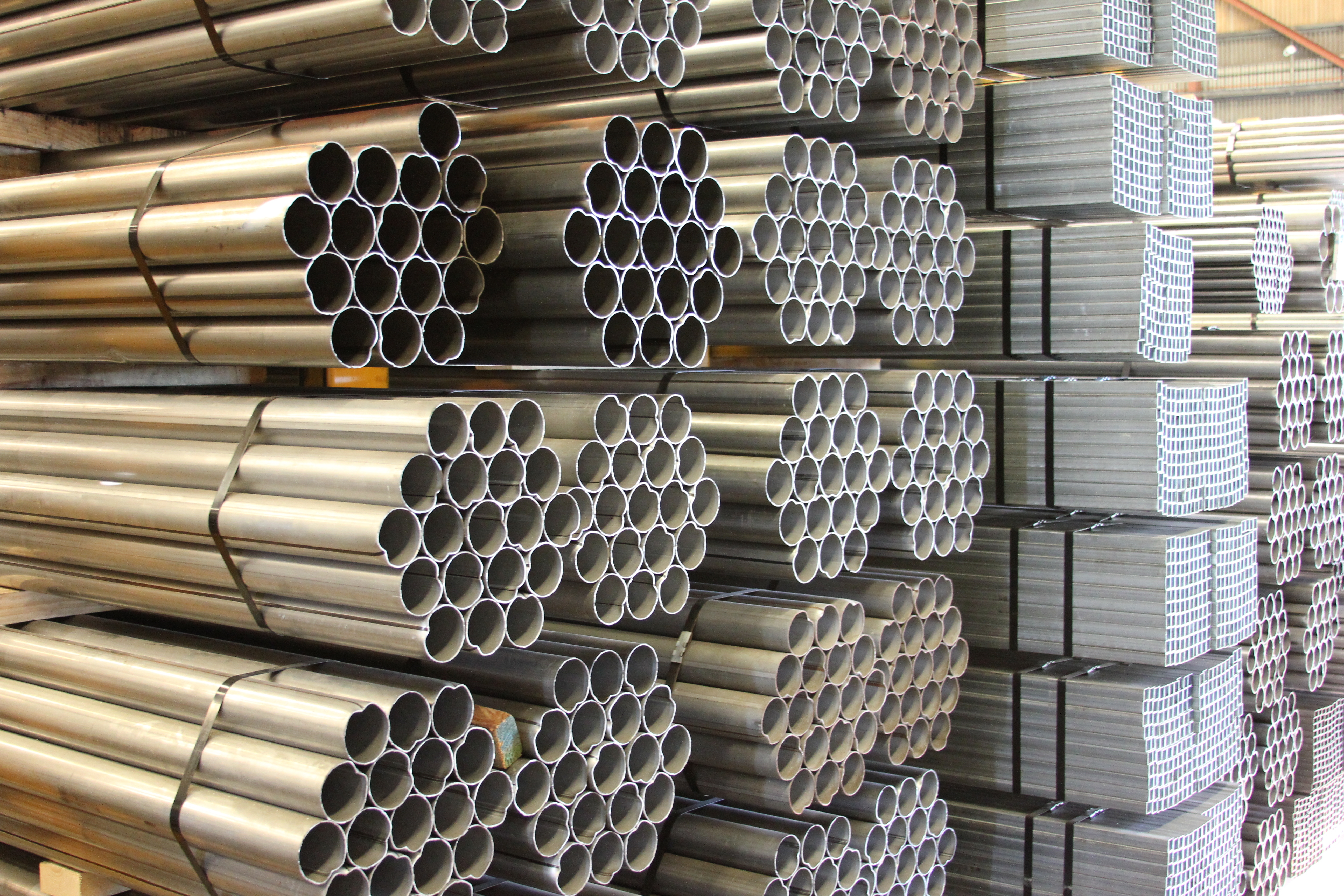
The most defining conclusion from the study was the noticeable difference between the corrosion of cars with 30% galvanized parts (primarily Indian cars ranging from 2-8 lakhs) and those which have nearly 70% galvanized parts (including some foreign brands). When cars falling into the same year were compared, it was evident that cars with 70% galvanized components had much better resistance to corrosion and other imperfections.
Considering its short-term and long-term benefits to MSMEs, large car makers, and the Indian auto industry as a whole, it would not be a stretch to label galvanized steel indispensable to the automotive industry.
Has your business made the switch to Galvanized Steel yet? JSW One offers a convenient, one-stop marketplace for all your galvanized steel buying needs. Choose from a variety of galvanized steel sheets and coils, certified under Indian Standards IS 277:2018 and IS 15961:2012. Shop now and get attractive discounts on select purchases.
Buy online
Mild SteelStainless SteelStructural SteelTMTCementJSW One MSME
About usBlogsSitemapJSW One TMTPolicy
Terms & conditionsPrivacy policyReturn policy