In the world of construction materials, cement plays a vital role in ensuring the strength and durability of structures. When it comes to choosing the right type of cement for a project, two standard options that often come into consideration are Ordinary Portland Cement (OPC) and Portland Pozzolana Cement (PPC). While both OPC and PPC are essential building blocks in construction projects, they have distinct characteristics that set them apart. In this article, we will delve into the differences between OPC and PPC cement to help you decide. Want to stay updated on the latest insights into construction materials and techniques? Register now to receive exclusive content straight to your inbox.
Composition
One of the primary distinctions between OPC and PPC cement is their composition. OPC is made from a combination of limestone (62 - 67%), silica (17 - 25%), alumina (3 - 8%) and gypsum (0.1 - 0.3%) that is finely ground to form a powder. On the other hand, PPC cement incorporates pozzolanic materials like fly ash (used up to 35%), or volcanic and gypsum (4%) along with clinker.
Grade and IS code
OPC cement has three different grades: OPC 33, OPC 43, and PPC 53. Each grade is covered under IS 269. On the other hand, PPC cement only has grade 33, having IS 1489 (Part 1 & 2).
Differences between Ordinary Portland Cement (OPC) and Portland Pozzolana Cement (PPC)
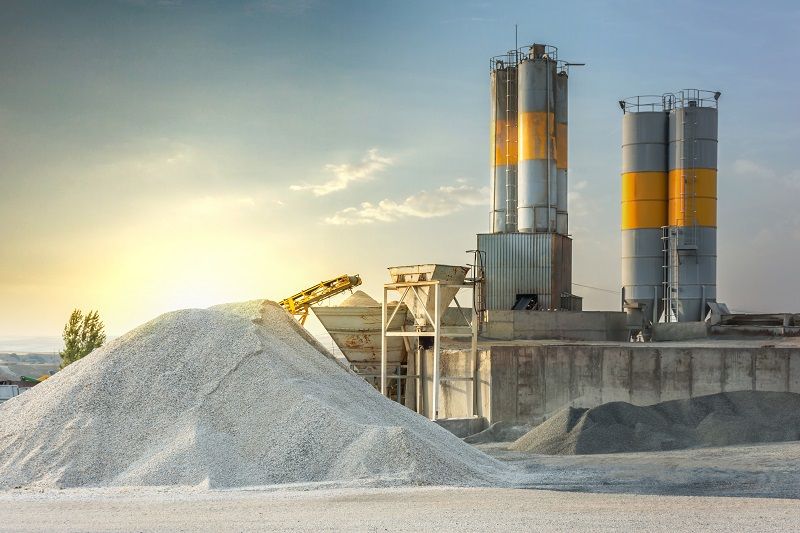
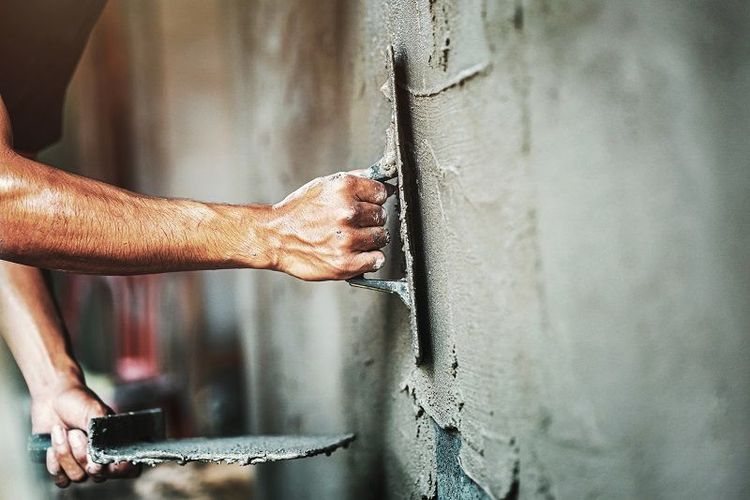
Setting time
Ordinary Portland Cement and Portland Pozzolana Cement's initial setting time is be at least 30 minutes, and the final setting time should be at most 280 minutes and 600 minutes, respectively.
Strength
When it comes to strength parameters, OPC cement takes the lead. It offers higher early-age compressive strength compared to PPC cement due to its composition. This makes OPC ideal for projects that require quick setting times or where high initial strength is crucial. However, it's important to note that both types of cement can achieve similar ultimate strengths over time with proper curing techniques.
Heat of hydration
The heat of hydration occurs when water reacts with cement, releasing heat. The amount of heat released is determined by factors such as the cement's composition, the curing temperature, the water-to-cement ratio, and the fineness of the cement. OPC cement generates more heat during the hydration process, while PPC cement has a slower hydration process thereby generating less heat.
PPC applications
- Mass concrete works: PPC is ideal for mass concrete works like dams, retaining walls, and large foundations, as it reduces the heat of hydration and prevents thermal cracking.
- Hydraulic structures: PPC is used in hydraulic structures, such as canals, ditches, and irrigation projects, due to its ability to resist chemical attacks from water and salts.
- Masonry mortar: PPC is commonly used in masonry mortar for bricklaying and plastering due to its excellent workability and setting characteristics.
- Repair and rehabilitation: PPC is often used in repair and rehabilitation works for old and damaged structures. It provides better resistance to chemical attacks and improves the durability of the repaired structures.
- Soil stabilisation: PPC is sometimes used in soil stabilisation projects, where it is mixed with soil to improve its strength and reduce settlement.
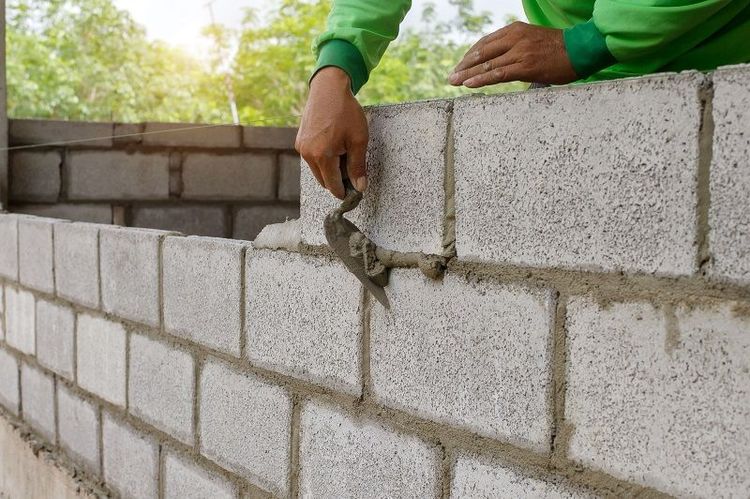
OPC applications
- General construction: OPC is widely used in various construction projects, including residential, commercial, and industrial buildings. It is suitable for all general-purpose concrete works, such as beams, columns, slabs, and foundations.
- Bridges and highways: OPC is employed in constructing bridges, highways, and other infrastructure projects due to its strength and durability. It can withstand heavy loads and harsh environmental conditions.
- Pre-stressed concrete: OPC is utilised in pre-stressed concrete elements, subjected to tensioning to counteract potential tensile stresses.
- Marine structures: OPC is preferred in marine structures like harbours, docks, and offshore platforms due to its resistance to the corrosive effects of seawater.
- High-rise buildings: OPC is often used in the construction of high-rise buildings because of its high compressive strength, making it suitable for supporting the weight of tall structures.
Conclusion:
In conclusion, while both OPC and PPC cement serve as essential components in the construction industry, they possess distinct characteristics that make them suitable for different applications. OPC is ideal for projects requiring quick setting times. Understanding these differences will enable construction professionals to make informed decisions when selecting the most appropriate type of cement for their projects. Sign up for exclusive updates to refine your material selection process.
Buy online
Mild SteelStainless SteelStructural SteelTMTCementJSW One MSME
About usBlogsSitemapJSW One TMTPolicy
Terms & conditionsPrivacy policyReturn policyBanking partner