OPC primarily comprises 96% clinker and 4% gypsum, and small amounts of other additives. It offers high early strength but might have higher heat generation during curing.
On the other hand, PSC includes a blend of 45% to 50% slag with 45%-50% clinker, and 3%-5% gypsum. PSC tends to have better long-term strength, and improved workability and lower heat generation by 20-50%. Join us to access a range of top-tier cement products, including both OPC and PSC—register to get started.
Strength and durability:
OPC usually exhibits higher initial strength but may have lower long-term strength than PSC. Due to the presence of slag, PSC tends to develop strength more gradually over time and often surpasses OPC in long-term durability.
Difference between ordinary portland cement and portland slag cement
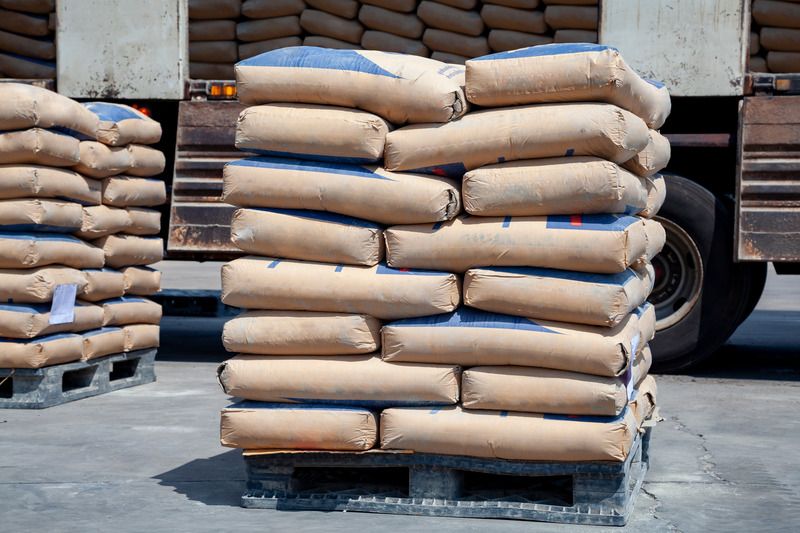
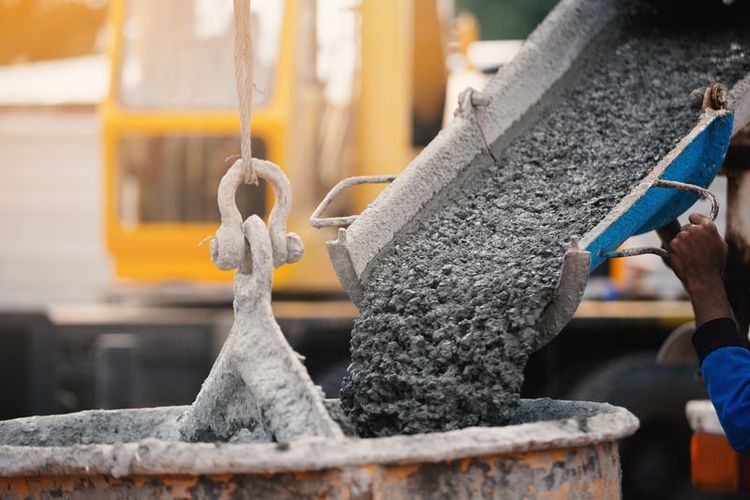
Resistance to environmental factors:
Compared to OPC, PSC often provides better resistance to chloride ingress, sulphate attack, and alkali-silica reactions. This makes PSC more suitable for construction in aggressive environments like marine projects, coastal roads etc. or where durability is a concern.
Sustainability:
PSC is considered more environmentally friendly as it incorporates a byproduct (blast furnace slag having binding properties that complement OPC), reducing the need for clinker production. This leads to lower CO2 emissions during the manufacturing process compared to OPC.
Cost considerations:
The cost of PSC might vary based on the availability of blast furnace slag in a particular region. Sometimes, it can be more cost-effective than OPC, but it might be pricier in areas where slag is less available.
Overview of OPC:
OPC is the most commonly used type of cement in construction. It's made primarily from limestone, clay, and , which are heated in a kiln to form a clinker. The clinker is then ground with gypsum to produce OPC. Different grades of cement (like OPC 33, OPC 43, OPC 53) have varying proportions of clinker, influencing their strength.
Manufacturing process:
Extraction of raw materials: limestone, clay, and other materials are quarried and extracted.
- Preparation of raw materials: these materials are crushed, ground, and proportioned to achieve the desired chemical composition.
- Clinker production: the prepared raw mix is heated in a rotary kiln at high temperatures (about 1450 degrees celsius), forming a clinker.
- Grinding: the clinker is then finely ground with gypsum to produce OPC.
Strengths and characteristics:
- OPC typically exhibits high initial strength and is widely available in various grades of cement like OPC 33, OPC 43, and OPC 53, based on its compressive strength after 28 days of curing.
- It tends to have a fast setting time, allowing for quick construction progress.
Common applications:
- OPC finds use in various construction applications, including residential and commercial buildings, roads, bridges, dams, and other infrastructure projects.
- Its versatility makes it suitable for general-purpose concrete works, masonry, plastering, and other construction activities.
Overview of PSC
PSC is a type of blended cement composed of OPC, gypsum, and GBFS – a byproduct of the steel industry. The slag typically constitutes 25-70% of the cement composition.
Manufacturing process:
- Clinker production: the raw mix is heated in a kiln to produce clinker, similar to the OPC manufacturing process.
- Addition of blast furnace slag: the clinker is blended with GBFS during the grinding stage. This blending results in the production of PSC.
Strengths and characteristics:
PSC tends to have lower heat generation during curing, reducing the risk of cracking.
PSC's slower strength development might offer improved workability and reduced permeability. Register today to access our premium OPC and PSC cement products, designed for optimal performance in all construction projects.
Common applications:
- PSC is suitable for various construction applications, particularly where durability and resistance to harsh environmental conditions are essential.
- It's commonly used in marine structures, sewage systems, coastal construction, and areas prone to sulphate attacks or chloride exposure.
PSC is also employed in residential and commercial buildings, bridges, dams, and infrastructure projects where enhanced long-term strength and durability are desired.
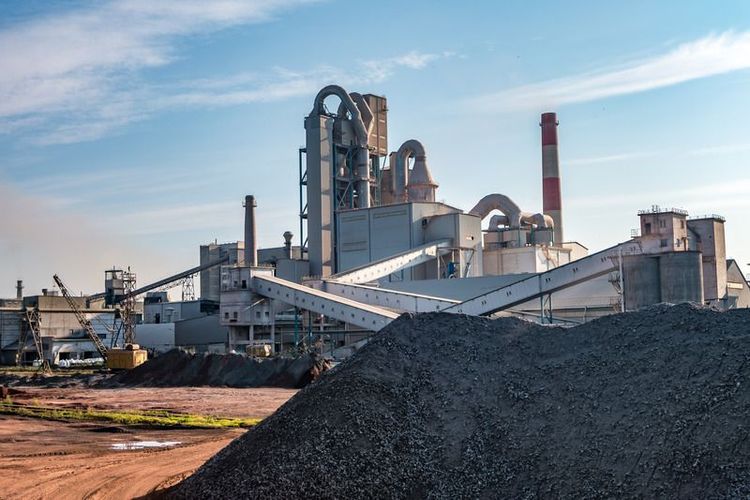
Key differences between OPC and PSC
Composition:
- OPC primarily comprises clinker, gypsum, and minor additives without any additional blending materials.
- PSC includes OPC clinker, gypsum, and GBFS, usually 25-70% by weight.
Manufacturing process:
- OPC is produced by heating a mix of limestone, clay, and other raw materials to form clinker, which is then finely ground with gypsum.
- PSC involves the same process as OPC up to the production of clinker. However, during grinding, PSC includes the addition of blast furnace slag.
Heat generation and setting time:
- OPC typically generates more heat during curing and has a faster initial setting.
- PSC produces less heat during curing and offers a slower setting time, enhancing workability and reducing the risk of cracking.
Buy online
Mild SteelStainless SteelStructural SteelTMTCementJSW One MSME
About usBlogsSitemapJSW One TMTPolicy
Terms & conditionsPrivacy policyReturn policyBanking partner