Cost-effective steel fabrication solutions for small businesses
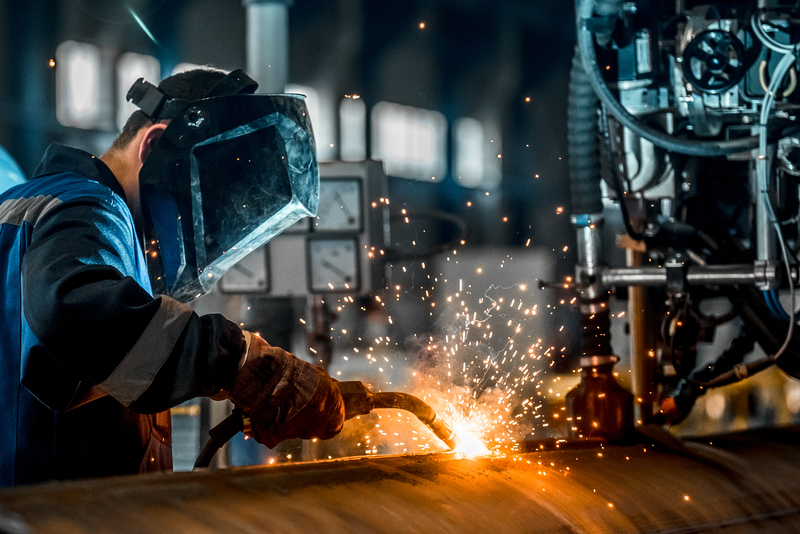
Steel fabrication is crucial for small businesses due to its versatility and durability in constructing various products and infrastructure. However, small businesses face significant cost challenges in this area. They encounter high initial investment costs for specialised equipment like welding machines and cutting tools, need help recruiting and retaining skilled labour, and contend with fluctuating material prices. Additionally, meeting regulatory standards adds another layer of expenses. Overcoming these obstacles demands careful financial planning, strategic investments, and a focus on operational efficiency to maintain competitiveness in the market.
Material costs:
Types of steel: steel fabrication involves using various types of steel, each with unique properties and costs. Common types include carbon steel, stainless steel, and alloy steel. Steel costs vary significantly based on factors such as composition, grade, and market demand.
Labour costs:
Skilled labour expenses: skilled labour is crucial for successful steel fabrication but comes with expenses. Welders, fabricators, and technicians with specialised skills command higher wages, contributing to labour costs.
Productivity impact: the productivity of skilled workers directly influences fabrication efficiency and, consequently, overall costs. Efficiency in welding, cutting, and assembly tasks can significantly impact labour expenses.
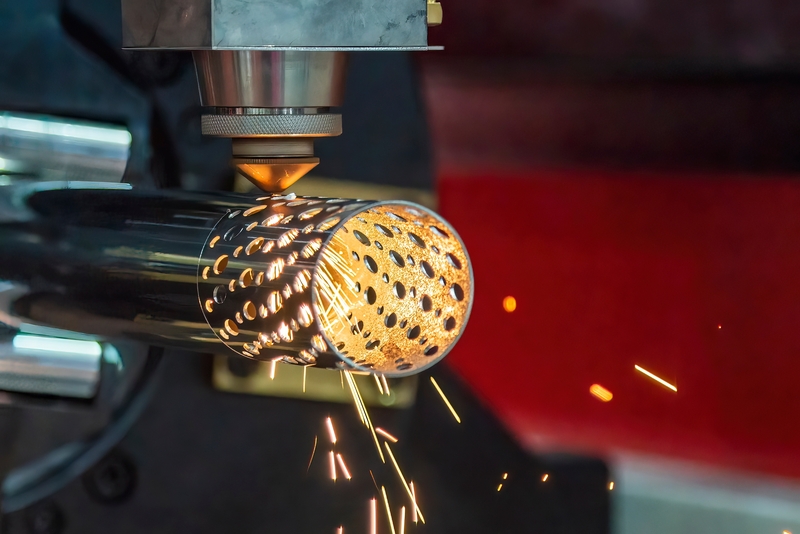
Equipment costs:
Machinery investment: steel fabrication requires specialised equipment such as welding machines, cutting tools, and bending machines. The initial investment in acquiring this machinery constitutes significant fabrication costs for small businesses.
Quality and capability: the quality and capability of equipment directly affect fabrication efficiency and production costs. Higher-quality machinery may offer improved precision, speed, and reliability, leading to cost savings in the long run.
Overheads:
Utility expenses: utilities such as electricity, water, and gas are essential for running fabrication operations but contribute to overhead costs. Energy-efficient practices and equipment can help mitigate utility expenses.
Rent and insurance: rental expenses for facility space and insurance premiums for property and liability coverage are additional overhead costs. Negotiating favourable lease terms and comparing insurance quotes can help manage these expenses effectively.
Cost-effective strategies
Material selection:
Choosing the correct grade and type of steel: consider required strength, corrosion resistance, and cost. Conduct a thorough analysis of the specific requirements of each project to determine the most suitable steel grade.
Investigate suppliers while buying from verified sellers and assess steel quality using test certificates.
Process optimisation:
Streamlining fabrication processes for efficiency: analyse current workflows to identify bottlenecks and inefficiencies. Implement lean manufacturing principles to eliminate waste and improve productivity.
Implementing lean manufacturing principles: This entails identifying value from the customer's viewpoint, mapping the value stream to streamline processes, and establishing a pull-based system to match production with customer demand.
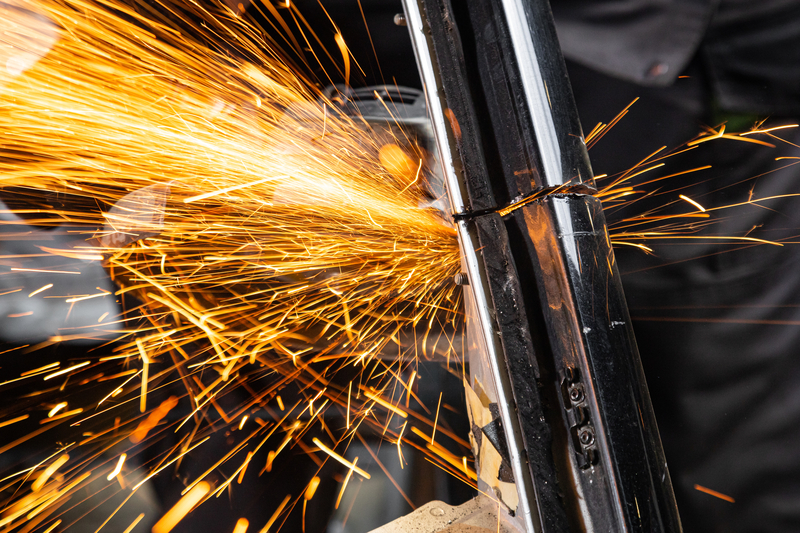
Workforce management:
Training programs to enhance skills and productivity: invest in training programs to improve the skills of your workforce, leading to higher-quality output and increased efficiency.
Utilising versatile workers for multiple tasks: cross-training employees allows for flexibility in task assignments, which can help maintain productivity levels during fluctuations in workload.
Equipment investment:
Evaluating the cost-benefit of purchasing vs leasing equipment: consider upfront costs, maintenance expenses, and technological advancements. Evaluate whether leasing or purchasing equipment aligns better with your financial goals and operational needs.
Identifying essential equipment for cost-effective fabrication: prioritise investments in equipment that directly contribute to productivity and quality improvement. Conduct a thorough cost-benefit analysis before making any significant purchases.
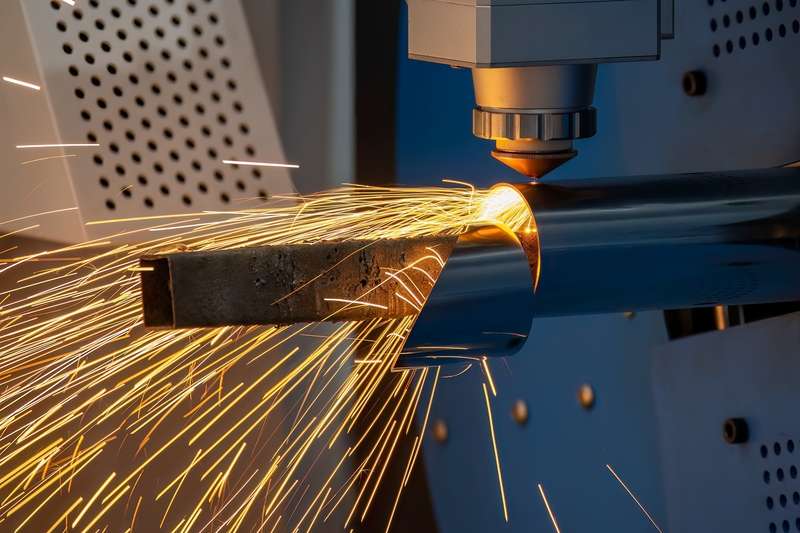
Outsourcing:
Assessing the feasibility of outsourcing specific tasks: evaluate non-core tasks or requiring specialised expertise. Outsourcing can reduce overhead costs and improve focus on core competencies.
Building partnerships with reliable third-party vendors: establish relationships with vendors consistently delivering quality materials or services at competitive prices. Negotiate favourable terms and maintain open communication to ensure smooth collaboration.
Apart from the strategies mentioned above, financial considerations play a critical role. Prudent budgeting for ongoing maintenance and upgrades is essential to ensure the equipment's longevity and optimal performance while preventing unexpected expenses. Moreover, for small businesses with limited capital, exploring financing options such as loans, leasing, or equipment financing programs can provide avenues to acquire necessary machinery without straining cash flow or compromising operational stability.
Buy online
Mild SteelStainless SteelStructural SteelTMTCementJSW One MSME
About usBlogsSitemapJSW One TMTPolicy
Terms & conditionsPrivacy policyReturn policy