Corrosion-resistant steel coatings for industrial and machinery parts in harsh Indian climates
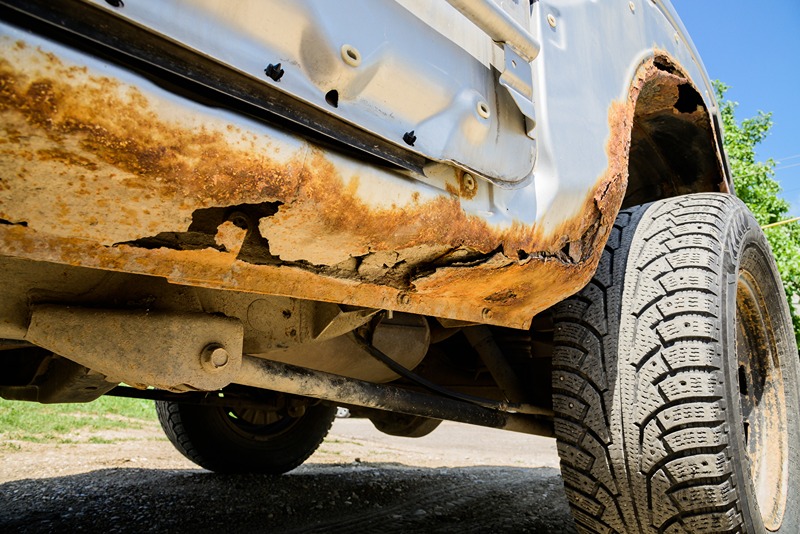
Steel is an essential material in industrial and machinery applications, offering strength, durability, and versatility. However, its susceptibility to corrosion poses a significant challenge, particularly in the extreme environmental conditions found across India. High humidity, coastal salinity, industrial pollutants, and temperature variations accelerate steel degradation, leading to reduced operational efficiency and increased maintenance costs. Corrosion-resistant steel coatings provide an effective solution, enhancing the lifespan and performance of steel components used in harsh climates.
How corrosion-resistant coatings protect steel
Corrosion-resistant coatings form a protective barrier between steel and environmental elements, preventing oxidation, rust, and surface deterioration. These coatings use advanced chemical compositions and application techniques to withstand aggressive atmospheric conditions, including exposure to moisture, salt, chemicals, and UV radiation.
Zinc coatings, such as galvanisation, provide sacrificial protection, ensuring the steel remains intact even when the coating is breached. Epoxy and polyurethane coatings offer strong chemical resistance, shielding industrial machinery from corrosive substances commonly encountered in manufacturing plants. Ceramic coatings enhance thermal stability, making them suitable for high-temperature environments, while fluoropolymer coatings ensure non-stick properties for specialised machinery applications.
Choosing the right coating for Indian climatic conditions
The diverse Indian climate demands tailored corrosion-resistant solutions. In coastal regions such as Mumbai and Chennai, where salt-laden air accelerates rust formation, hot-dip galvanisation and zinc-aluminium coatings provide robust protection. Industrial hubs like Delhi and Ahmedabad, exposed to high pollution levels and chemical fumes, benefit from epoxy-based coatings that resist acid and alkali attacks.
For extreme temperature variations, as experienced in Rajasthan and central India, ceramic coatings with thermal insulation properties prevent steel components from deteriorating due to heat-induced expansion and contraction. In high-humidity zones such as Kerala and Assam, polymer-based coatings offer water resistance, reducing moisture penetration and subsequent corrosion.
Application techniques for maximum durability
The effectiveness of corrosion-resistant coatings depends on proper surface preparation and application methods. Abrasive blasting removes existing rust and contaminants, ensuring strong adhesion. Thermal spraying, electroplating, and powder coating techniques provide uniform coverage and superior durability compared to conventional paint applications.
Advanced nanotechnology-based coatings are gaining traction, offering ultra-thin yet highly effective corrosion barriers. These coatings provide self-healing properties, enhancing longevity and reducing maintenance requirements for industrial machinery and infrastructure components.
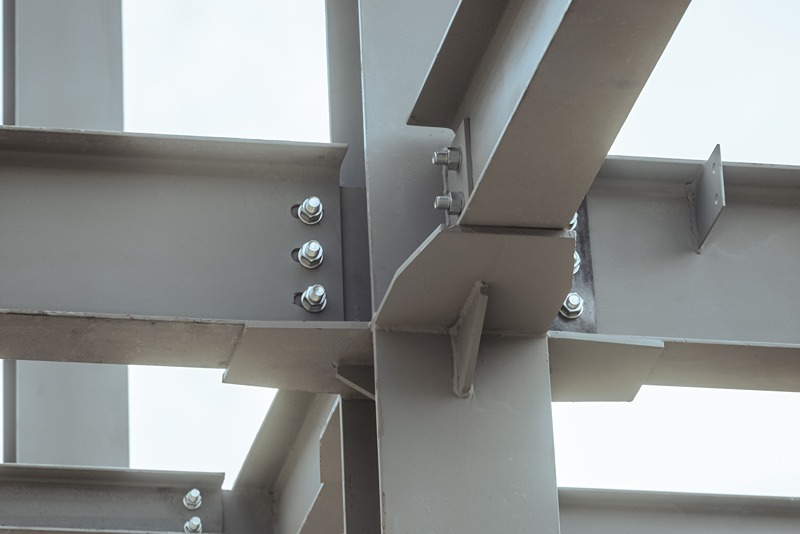
Economic and environmental advantages of corrosion-resistant coatings
Beyond performance benefits, corrosion-resistant coatings contribute to cost savings and sustainability. They extend the service life of machinery and industrial parts, reducing the frequency of replacements and downtime. This leads to lower maintenance costs and increased operational efficiency.
Additionally, modern coating formulations focus on environmentally friendly solutions. Water-based and solvent-free coatings reduce volatile organic compound (VOC) emissions, aligning with India’s push towards greener industrial practices. The adoption of sustainable coating technologies helps industries comply with environmental regulations while improving asset longevity.
Future trends in corrosion protection for Indian industries
As industries across India seek enhanced durability and cost-efficiency, research in corrosion-resistant coatings is evolving. Smart coatings with embedded sensors enable real-time monitoring of corrosion levels, allowing predictive maintenance and reducing unexpected failures. Graphene-based coatings, known for their exceptional strength and chemical resistance, are expected to revolutionise steel protection in the coming years.
With continuous advancements in coating technology, industrial sectors such as manufacturing, construction, and transportation can achieve greater resilience against corrosion, minimising long-term economic losses.
Conclusion
Corrosion-resistant steel coatings play a vital role in ensuring the durability of industrial and machinery parts in India’s diverse and challenging climates. By selecting the right coating solutions based on environmental exposure, industries can significantly enhance asset longevity, reduce maintenance costs, and improve overall efficiency. As protective technologies advance, adopting innovative coatings will be crucial in safeguarding industrial investments against corrosion-related deterioration.
Buy online
Mild SteelStainless SteelStructural SteelTMTCementJSW One MSME
About usBlogsSitemapJSW One TMTPolicy
Terms & conditionsPrivacy policyReturn policy