In the realm of construction, the durability and longevity of structures are paramount. However, even the most carefully designed and meticulously constructed buildings can fall victim to a common adversary known as concrete spalling. In this blog post, we will delve into the intricacies of concrete spalling – what it is, what causes it, and the detrimental effects it can have on the structural integrity of concrete surfaces.
What is concrete spalling?
Concrete spalling is a phenomenon that occurs when concrete surfaces start to chip, crack, and break off. It's not merely a cosmetic concern; it's a signal of underlying structural issues. Imagine a weathered sidewalk with pieces of concrete strewn about or a parking garage with chunks of concrete missing from its columns. These are textbook examples of concrete spalling, a telltale sign that something is amiss beneath the surface.
Concrete spalling: Causes, effects and repair
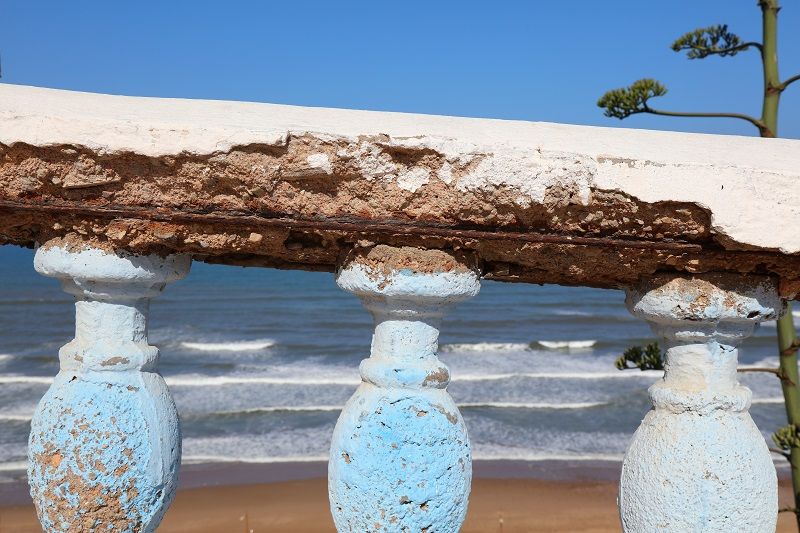
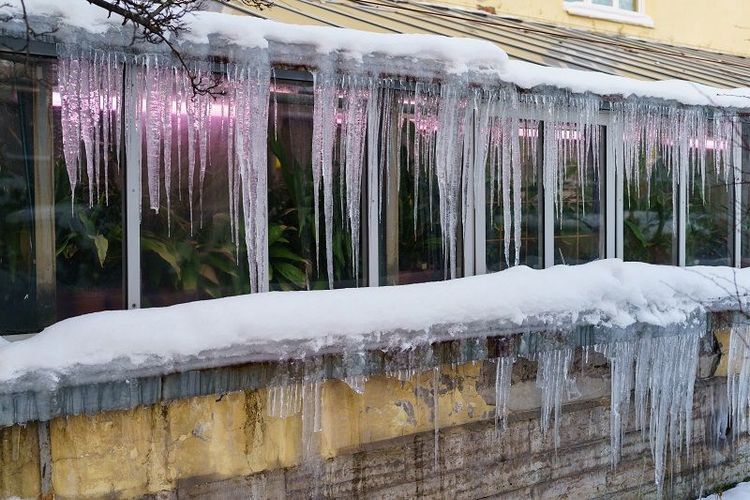
Concrete is prone to spalling when exposed to temperatures between 200 degrees Celsius and 500 degrees Celsius. Spalling can be affected by internal factors such as water-cement ratio, moisture content, aggregate types, and permeability. External factors like heating rate, fire temperature, environmental conditions (temperature and humidity), and load level can also play a role.
Causes of concrete spalling
1. Freeze-thaw cycles
One of the primary causes of concrete spalling is the relentless cycle of freeze and thaw. When water infiltrates the concrete, it occupies space within the material. During freezing, this water expands as it turns to ice, exerting pressure on the concrete. When the ice thaws, the water contracts, leaving behind voids and cracks. Over time, these cracks propagate, causing chunks of concrete to break off. Climate and geographical factors play a significant role in the severity of freeze-thaw damage.
2. Corrosion of reinforcement
Reinforcement bars play a crucial role in enhancing the structural strength of concrete. However, when moisture and oxygen reach the reinforcement, a destructive process known as corrosion begins. As the reinforcement rusts and expands, it exerts pressure on the surrounding concrete, leading to cracks and spalling. This hidden enemy can weaken structures from within, compromising their load-bearing capacity.
3. Alkali-silica reaction (ASR)
The seemingly innocuous interaction between certain aggregates and alkalis in cement can result in a destructive chemical reaction called alkali-silica reaction (ASR). This reaction produces a gel-like substance that swells upon absorbing water, causing concrete to crack and spall. Identifying ASR-induced spalling can be challenging, but it's essential for preventing further deterioration.
4. Chemical exposure
Concrete surfaces are often subjected to various chemicals, ranging from acidic solutions to sulphates. These substances can react with the concrete, weakening its structure and leading to spalling over time. This is particularly evident in industrial environments where chemical exposure is commonplace. Using chemical-resistant materials and implementing proper storage and handling practices can mitigate this cause of spalling.
Effects of concrete spalling
The consequences of concrete spalling are far-reaching and can significantly compromise the overall integrity of a structure. Firstly, the structural stability of the affected concrete is compromised, reducing its load-bearing capacity and potentially jeopardising the safety of occupants. Secondly, the aesthetic appeal of the structure takes a hit, as spalling leads to an unsightly appearance that diminishes the value of the property. Furthermore, spalled areas become more vulnerable to additional deterioration, accelerating the cycle of damage.
Prevention and remediation
1. Quality concrete mix design
The foundation of preventing concrete spalling lies in the mix design. Ensuring the proper ratio of aggregates, cement, water, and additives is crucial. Additionally, using appropriate aggregates and cement types for specific environments can minimise the potential for spalling.
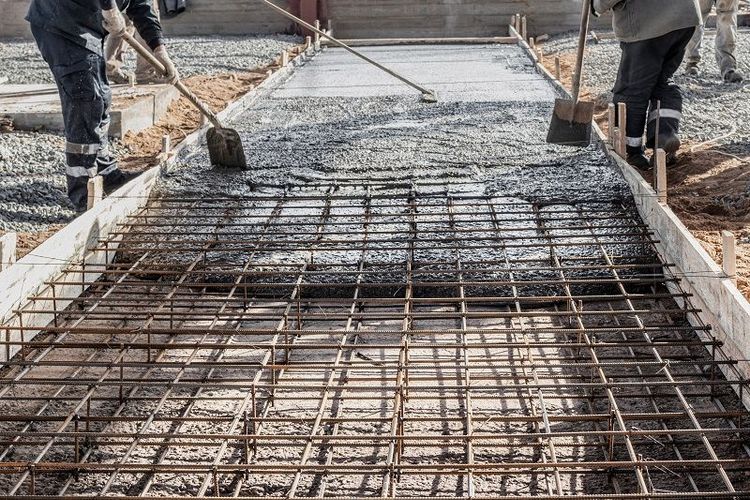
Repair material selection:
For minor surface spalling: apply a patching compound or repair mortar designed for small repairs. These materials are typically polymer-modified and have good bonding properties.
For deeper spalling: use a repair mortar or concrete mix that matches the existing concrete in terms of strength, colour, and texture.
Mixing and application:
Follow the manufacturer's instructions for mixing the repair material. Typically, you'll need to add water and mix until you achieve a workable consistency.
Apply the repair material to the damaged area, ensuring it is compacted and properly shaped to match the surrounding surface. Use a trowel or other suitable tools for application.
Finishing:
Smooth the repaired surface to match the texture of the surrounding concrete. You can use a trowel, float, or other finishing tools to achieve the desired texture.
Curing:
Properly curing the repaired area is essential for the material to gain strength and durability. Cover the repaired section with plastic sheeting or use a curing compound to retain moisture during the initial curing period.
2. Waterproofing and sealing
Applying waterproof coatings and sealants to concrete surfaces forms a protective barrier against moisture infiltration. This is particularly important in areas prone to freeze-thaw cycles. Regular maintenance of these coatings ensures their effectiveness over time.
3. Corrosion protection
To combat reinforcement corrosion, the use of corrosion-resistant materials reinforcement is recommended. Applying protective coatings to reinforcement bars and closely monitoring signs of corrosion can extend the lifespan of concrete structures.
4. Avoiding alkali-silica reaction (ASR)
Selecting aggregates with low potential for ASR is essential. Supplementary cementitious materials like fly ash or slag can also mitigate the risk of ASR by reducing the availability of alkalis. Conducting expansion tests on potential aggregate combinations can help identify potential ASR issues early on.
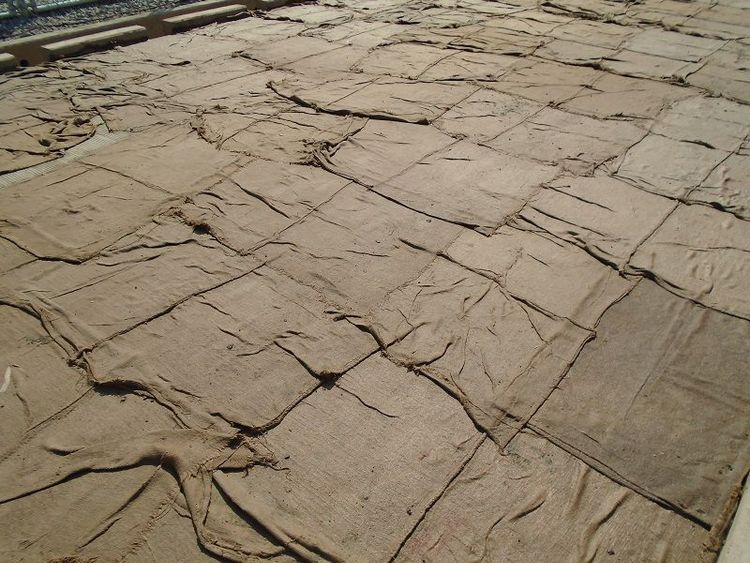
5. Chemical exposure management
For environments where chemical exposure is likely, taking measures to prevent chemical ingress is vital. This includes proper storage, handling, and containment of chemicals, as well as the use of chemical-resistant barriers to protect concrete surfaces.
Repairing spalled concrete involves addressing the damaged areas and restoring them to their original condition. The specific approach for repairing spalled concrete depends on the extent of the damage and the underlying causes. Adequate curing, proper reinforcement, correct placement, and regular inspections are essential to ensure the long-term durability of concrete structures. Consulting with a professional engineer or concrete specialist is recommended for specific projects to determine the best approach for preventing concrete spalling.
Buy online
Mild SteelStainless SteelStructural SteelTMTCementJSW One MSME
About usBlogsSitemapJSW One TMTPolicy
Terms & conditionsPrivacy policyReturn policyBanking partner