Colour-coated steel: The perfect blend of aesthetics and sustainability
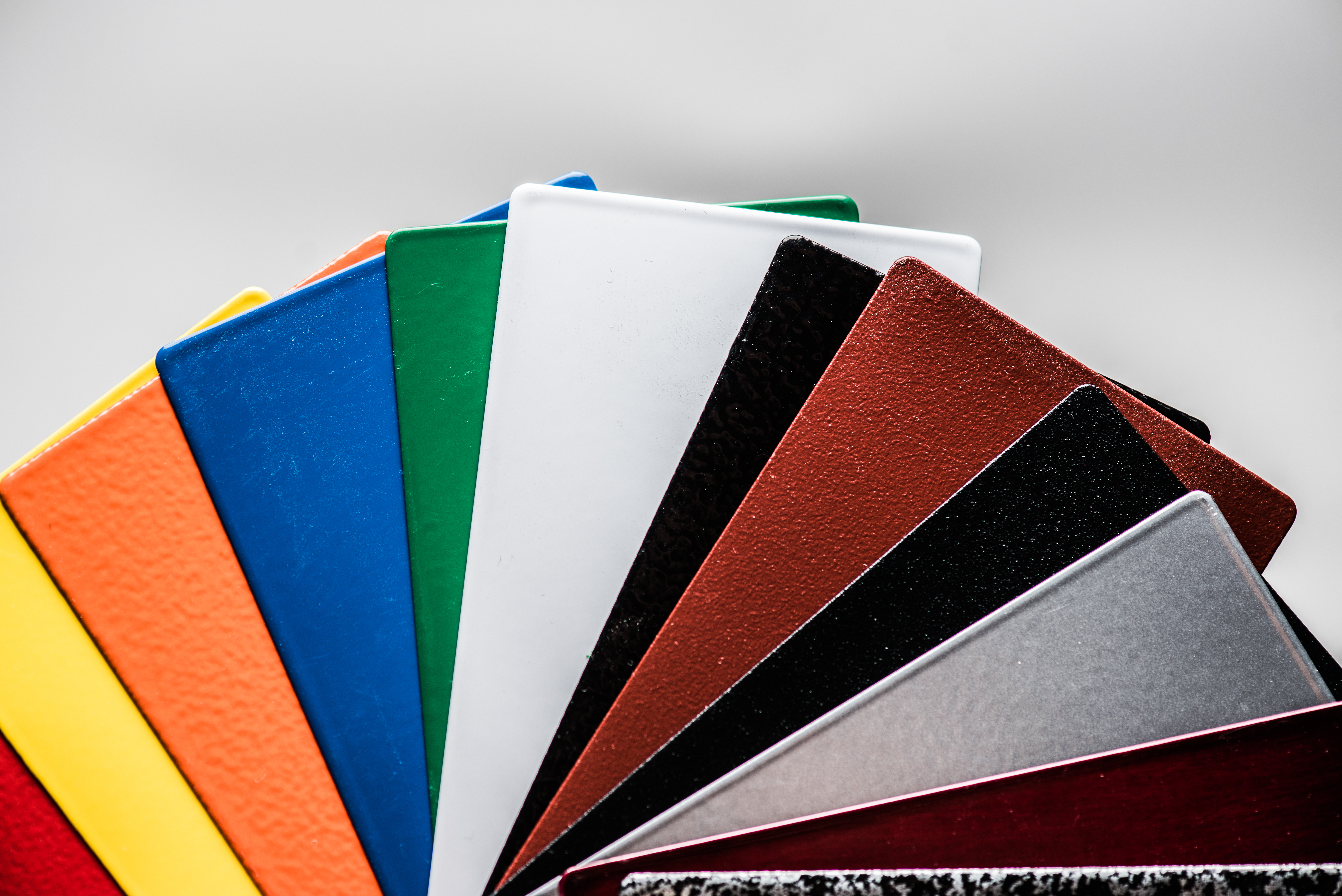
Pre-painting or colour-coating is simply described as applying a decorative or protective coating to a steel substrate in a continuous process after pre-treatment. These paint coatings are used to enhance productivity and add environmental benefits & strength to the substrate steel, while extending long-term protection from corrosion. The base material of colour-coated steel consists of an aluminum & zinc coating which protects the steel from corrosion by sacrificing itself and reacting with environment to form protective compounds. The pre-treatment layer not only improves the corrosion resistance, but also gives a good adhesion to the coating layer. This layer also gives the final colour to the product. It also imparts in steel an aesthetic finish and improves durability.
Colour-coated steel coils are in increasing demand from a variety of business sectors ranging from construction to home electronics, fabrication, and even chipmakers, as consumers have become more self-assertive and want to have their goods in style.
Coated steel is generally categorized into three broad categories: -
Metallic coating: - This is typically a coating of zinc in pure or alloyed form. This process is called galvanising. These coatings can be applied by using a sprayer, electromechanically, chemically, or mechanically. This kind of coating is applied on equipment requiring a shiny or glossy appearance. The metallic coating applications include air conditioners, vehicle parts, outdoor electrical boxes, laundry appliances, refrigerators, roofing sheets, etc.
Organic coating: - Organic coating is a non-metallic coating, mostly polyester paint or polyvinylidene fluoride paint (PVDF). PVDF sheets are costlier as compared to polyester paint but give higher impact and scratch resistance. Organic coated sheets are generally used in lifts, furniture, ceilings, decorative partitions, etc.
Tinplates: - Tinplates are made by coating tin on cold rolled steel. Annealing and tempering process is used to prepare a cold rolled sheet for tinning. Tin is applied to the black plate (tempered steel used as a substrate for tinplate) through the continuous electrolytic bath. The tinplate market is generally small as compared to other coated steel products and food industry investments are mainly driving this market.
Coating process
1. The coil is moved to the uncoiler whereby the steel is placed on a pay-off arbor for unwinding
2. The end of the previous coil is mechanically joined to the beginning of the next coil, which allows for the continuous feed of the coil coating line.
3. The entry tower will now allow the material to accumulate and continue the operation of the coil coating process. This accumulation will continue to feed the coil coating processes while the entry has stopped for the stitching process
4. The cleaning and pre-treating process focus on preparing the steel for painting. Dirt, oil, and debris are removed from the steel strip at this stage.
5. The steel enters the pre-treatment stage now and it goes through a chemical application to facilitate paint adhesion
6. The steel has to go through a dried in place chemical coater, where a chemical material is applied to provide enhanced corrosion performance
7. The steel strip now enters the prime coat stage wherein a primer is applied to the pretreated steel, after which the metal strip goes through a thermal oven to cure.
8. After the primer application, a final coat is applied to the steel strip. This topcoat provides corrosion resistance, colour, flexibility, and durability.
9. The coil is now removed from the line and packaged for shipment or additional processing
Tests conducted on the colour-coated steel
Ensuring the integrity of the coating is absolutely essential. There are severe risks associated with coating failure and hence testing the mechanical properties of a coating is one of the best ways to make sure that the coating can withstand the environmental and operational conditions in which it will be placed.
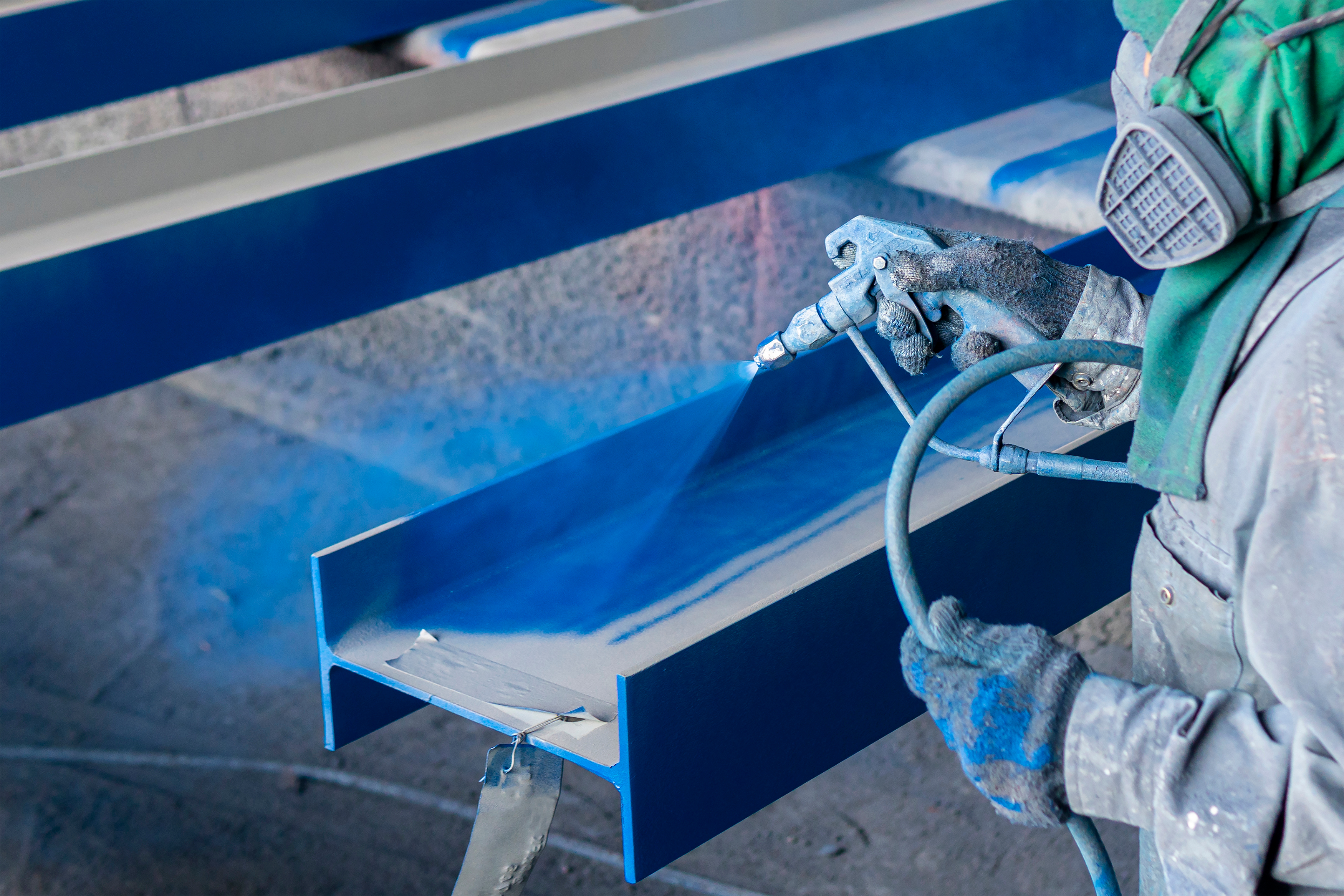
Impact test – The impact test is exercised to judge the resistance of the colour coating to the mechanical damage. It is carried out by the falling weight test as per the ASTM D 2774-84 standards. This method is used to check for cracks or loss of adhesion in areas other than the impact area.
Bending adhesion test – This test is done to assess the adhesion of coating films to the steel substrates. A 180 degrees’ bend is made by applying force in a bending machine and the sample is folded twice the thickness of the substrate to assess the colour coating adherence.
Flexibility test – This test is carried out to determine the flexibility resistance to cracking of colour coating on the substrate. It is conducted with the help of a conical mandrel. A sample of the coated steel sheet is bent over the mandrel through 180 degrees in one second, post which the colour-coated film is looked into for cracks and sheds.
Hardness test – Also known as the pencil test, this test is done to examine the hardness of the coat to in turn assess the mechanical damage. The sample is fixed at the bottom of the equipment with the help of two fixtures. A minimum of 2H high hardness is essential for the substrate to clear this test as per the ASTM D 3363-74 standards.
Chemical Resistance Test – The samples of the colour-coated sheets are immersed in distilled water, 5 % aqueous solution of NaOH, and 5 % aqueous solution of H2SO4 solution for 24 hours. The samples are then evaluated for any evidence of chemical attacks, blistering, disbondment, chalking, or cracking.
The corrosion control provided by the colour coating is remarkable as compared to either system used alone. The coating protects the base steel and extends barrier protection besides slowing down the zinc consumption rate. All these combined really provide longevity to the coated steel. Even after the coating is weathered down, the zinc is there to provide rust protection after the paint peels off. This synergy provides at least 1.5 -2.5 times more corrosion protection than the sum of the lifetimes of zinc and colour coating used individually. Besides corrosion resistance, the other advantages of using the colour coated steel are: -
Prevention from flaking and peeling
Excellent formability and design flexibility
Easy to install
Maintenance free
Recyclable and environment friendly
Lightweight but structurally strong
Thermal efficiency
We at JSW One are dedicated to supplying the best quality colour-coated products to our customers which withstand all kinds of weather, be it heavy rains, salty sea air, humid coastal areas, cold snow areas, or heat.
JSW Colour Coated Steel is manufactured using high-quality hot metal, made of the most superior and environment-friendly Corex technology. It offers several grades including high tensile steel with a yield strength of min. 550 mpa and max. 700 mpa to meet the need of various applications. Roofs made from light-coloured JSW Colour Coated Steel can result in less heat radiation into homes, compared to other commonly used roofing materials. Steel roof when combined with insulation makes a cost-effective and energy-efficient roofing system. JSW Colour Coated Steel is available in a variety of paint systems like Regular Modified Polyester (RMP), Silicon Modified Polyester (SMP), Super Durable Polyester (SDP), Poly Vinyldened Fluoride (PVDF), etc. The base metal has the first layer of primer coating on both the top & bottom surface for superior adhesion with the paint system. The final paint coat provides additional protection to withstand harsh weather conditions and other factors affecting longer life. The superior coating technology resists cracking and peeling even during heavy forming operations.
As the largest producer of coated products in India, JSW Steel brings together the strength of steel, the beauty of paint and enhanced corrosion resistance all in one unbeatable package. JSW’s colour coated steel come in a wide range of thicknesses, widths, colours and profiles. They are designed with superior coating technology to resist cracking and peeling, even during heavy forming operations.
Shop for the top-class colour-coated products from JSW – JSW colouron plus and JSW pragati plus at jswonemsme.com, today!
Buy online
Mild SteelStainless SteelStructural SteelTMTCementJSW One MSME
About usBlogsSitemapJSW One TMTPolicy
Terms & conditionsPrivacy policyReturn policy