Best practices for welding steel in auto parts manufacturing
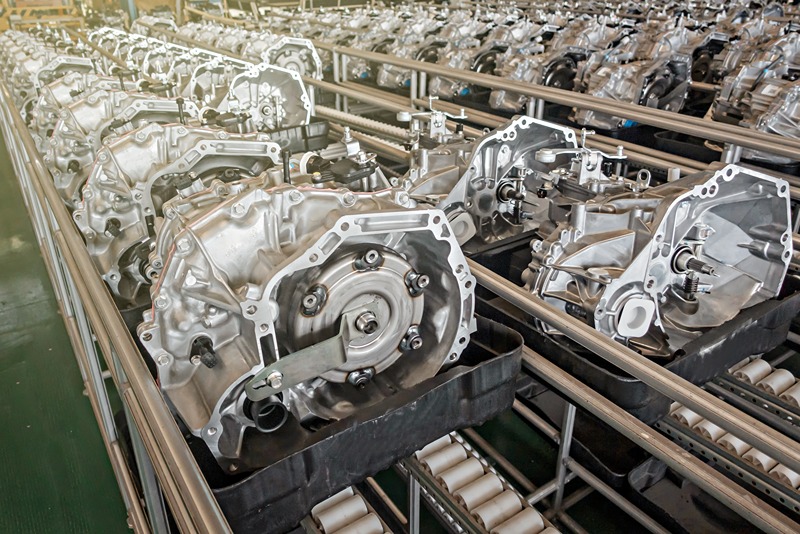
Welding plays a crucial role in auto parts manufacturing, particularly for Indian MSMEs focused on quality and durability in steel components. Steel remains a primary material in vehicle construction, so precise welding ensures robust, long-lasting parts. This blog offers insights into best practices for welding steel aimed at MSMEs. Select the right welding process In auto parts manufacturing, different welding techniques are used based on the type of steel and component. Below are the commonly employed methods:
MIG Welding (Metal Inert Gas): Ideal for high-volume production, MIG welding involves a wire-fed process, making it faster and suitable for joining thicker metals. It is widely used in automotive manufacturing for components such as body panels and interior parts. Try Ador Automig-1 ER70S-6 C-Mn Steel MIG Welding Wire, available on the JSW One platform, for a reliable process.
TIG Welding (Tungsten Inert Gas): TIG welding produces precise, clean welds, especially for thin, intricate parts. It’s frequently used for smaller, more delicate automotive parts, such as pipes and fuel tanks. For this purpose, Ador Tigfil ER70S-2 C-Mn Steel TIG Welding Wire is an excellent choice.
Resistance Spot Welding: Often used for joining sheet metal in cars, spot welding is highly efficient, ensuring fast production. It is typically employed for tasks such as welding chassis components and body frames.
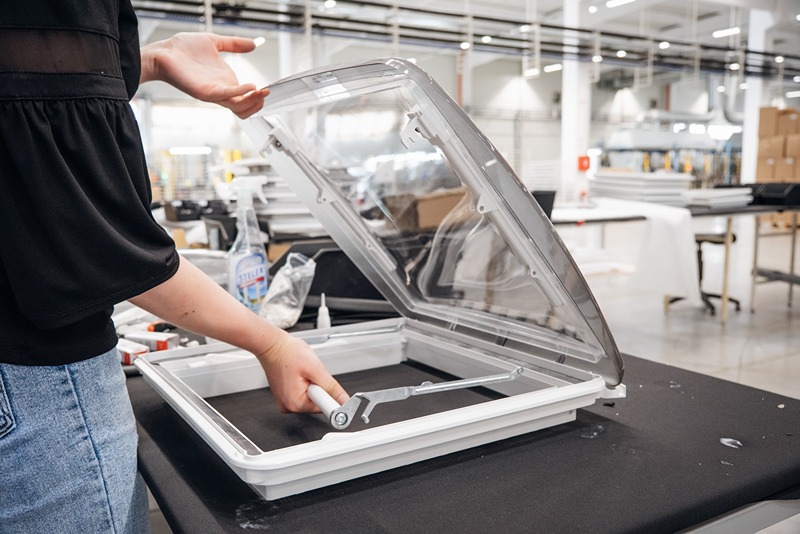
Choose the appropriate welding consumables Selecting the right welding consumables is vital for ensuring strong, durable welds. When welding mild steel, consumables like Ador Kingbond S E6013 Mild Steel Welding Electrode are recommended for general-purpose welding tasks, providing a smooth, stable arc. For carbon-manganese (C-Mn) steel, Ador Automelt EM12K C-Mn Steel SAW Welding Wire offers superior performance in submerged arc welding applications, ensuring high deposition efficiency. For projects requiring stainless steel welding, opt for the Ador Superinox 2A E316-16 Stainless Steel Welding Electrode. This electrode offers excellent corrosion resistance, making it ideal for automotive components exposed to harsh conditions. Follow proper safety protocols Safety should be a top priority when welding steel in auto manufacturing. Ensure that all workers are equipped with proper personal protective equipment (PPE) such as gloves, helmets, and goggles. Welding produces harmful fumes, so it is essential to maintain proper ventilation in the workspace. Additionally, fire prevention measures, such as having fire extinguishers nearby, should be in place at all times. Control heat input to prevent warping Automotive parts, especially those made from thinner steel sheets, can warp due to excessive heat input during welding. A common technique to mitigate this is skip welding, where welds are spaced out to distribute heat evenly. This method allows the workpiece to cool between welds, preventing distortion. For added control, using a smaller diameter welding wire can help. For example, in MIG welding, a 0.8 mm wire such as Ador Automig-1 ER70S-6 C-Mn Steel MIG Welding Wire helps minimise heat input while maintaining the integrity of the weld.
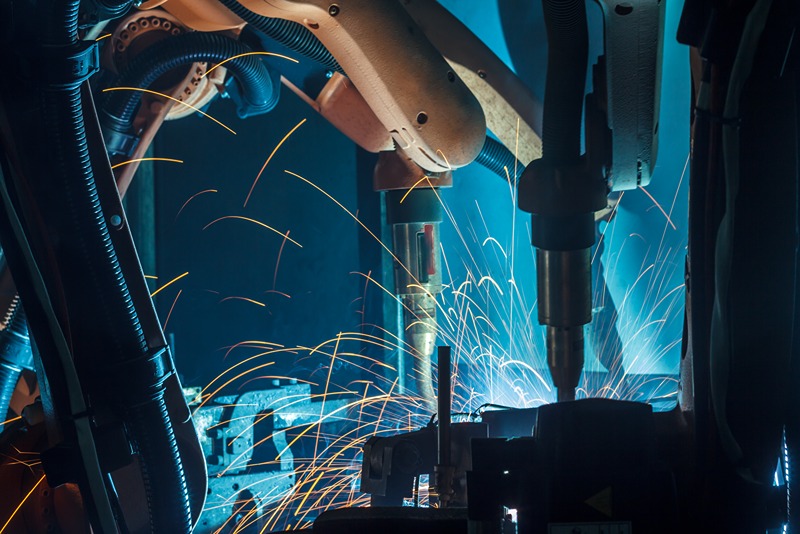
Clean and prepare surfaces before welding A clean surface is critical for producing strong welds. Any dirt, oil, or rust on the steel can compromise the weld, leading to weak joints. Always ensure that the welding area is thoroughly cleaned using a wire brush or degreaser before starting. This simple step significantly reduces the chances of defects and ensures a smooth, durable weld. Use the correct power settings Thin automotive steel sheets can easily be damaged if the welding machine is set to a high-power level. Always begin with a lower power setting, particularly when welding thinner materials, to avoid burning through the metal. This approach helps achieve cleaner, more precise welds without compromising the material’s strength. Employ backing bars for better heat dissipation When welding delicate or heat-sensitive auto parts, a backing bar can prevent overheating and reduce the risk of warping. A backing bar, often made from copper or aluminium, is clamped to the workpiece to quickly dissipate heat, resulting in a more controlled welding process.
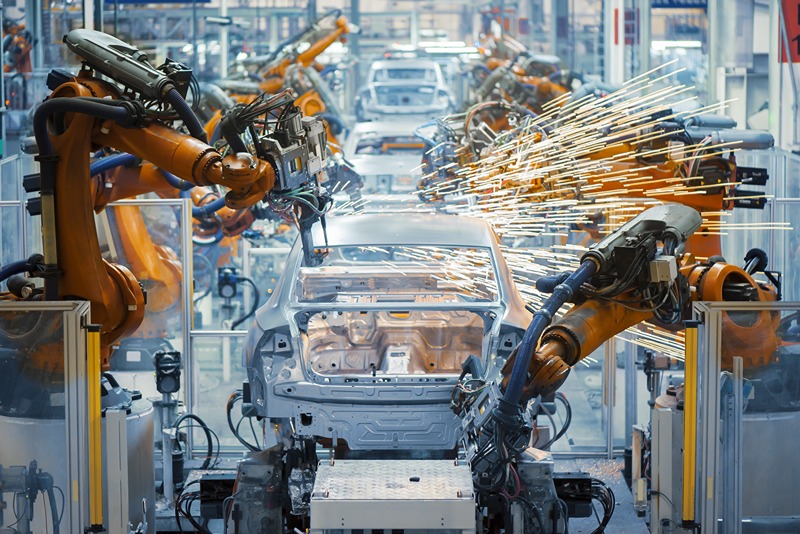
Test and inspect welds After welding, it is critical to inspect the joints for quality. Techniques such as non-destructive testing (NDT), including visual inspection and ultrasonic testing, can help identify potential defects, such as cracks or weak points. This step is essential in ensuring that the welded parts meet the required strength and safety standards for automotive use. Conclusion By carefully selecting the appropriate welding process—be it MIG for high-volume applications or TIG for precision work—businesses can optimise their operations based on the specific requirements of different components. In addition, controlling heat input, maintaining clean surfaces, and utilising backing bars are all crucial for avoiding defects such as warping and weak welds, particularly in thin automotive steel parts.
Buy online
Mild SteelStainless SteelStructural SteelTMTCementJSW One MSME
About usBlogsSitemapJSW One TMTPolicy
Terms & conditionsPrivacy policyReturn policy