Basics you need to know about PEB industrial shed and factory building
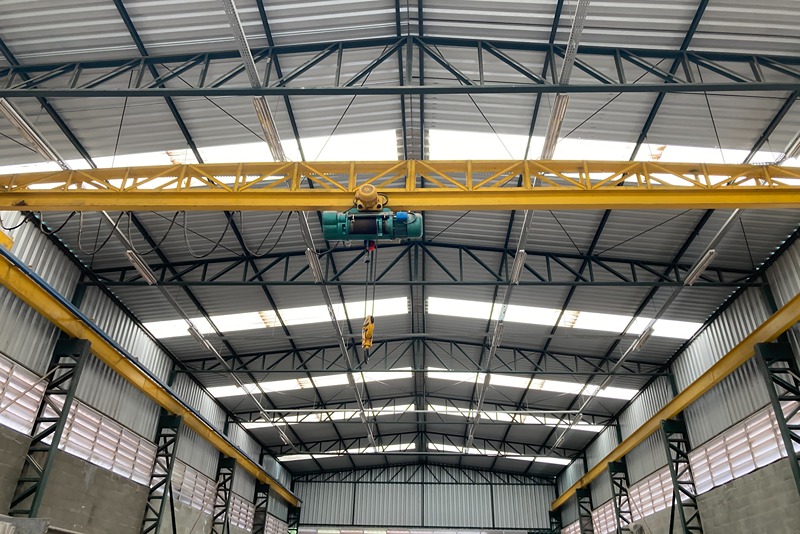
PEB industrial sheds and factory buildings are steel structures designed using prefabricated components manufactured in controlled environments. These components are transported to the site and assembled to create structures customised for specific industrial applications. PEBs differ from traditional construction methods as they are pre-designed to exact specifications, ensuring a precise fit and minimal wastage during construction. Their modularity allows them to accommodate various industrial operations, including manufacturing, warehousing, and assembly. Core features of PEB industrial sheds and factory buildings 1. Customisation for industry-specific needsPEBs are highly customisable. Engineers design these structures to account for industry-specific requirements, such as:a. Heavy load-bearing capacity: Suitable for industrial cranes and heavy machinery. b. Ventilation and air circulation: The design incorporates natural ventilation systems and HVAC compatibility. c. Natural lighting: Skylights and translucent roof panels reduce reliance on artificial lighting.2. Optimised spans for large, unobstructed spacesIndustrial operations often require open layouts to allow machinery installation, workflow efficiency, and storage. PEBs can span up to 90 metres without internal columns, making them ideal for such needs.3. Fast-track construction Components of PEBs are fabricated simultaneously while site preparation occurs, leading to significant reductions in project timelines. This overlap of processes allows businesses to reduce downtime and achieve operational readiness quickly.4. Durability under industrial conditions PEBs are engineered to endure operational stresses such as machinery vibrations, high temperatures, and exposure to chemicals or moisture. They are made from high-strength steel that adheres to strict quality standards, ensuring reliability over extended service periods.5. Energy and cost efficiency PEBs incorporate features like reflective roofing, insulated panels, and natural ventilation, reducing energy costs. Prefabrication ensures minimal material wastage, lowering construction costs without compromising on quality.
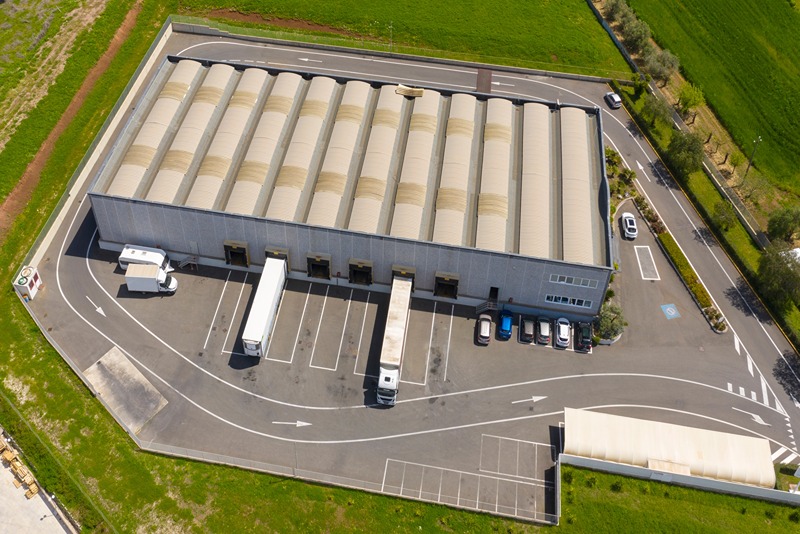
Technical components of PEB sheds and factory buildings 1. Primary framing Made from steel sections like I-beams, primary framing provides the structural strength to withstand loads, including wind, seismic forces, and operational stresses. Frames are pre-designed for specific load requirements, ensuring structural integrity.2. Secondary framing Purlins, girts, and eave struts support the roof and walls, adding stability and distributing loads. These components also facilitate easy attachment of roofing and wall panels.3. Roof and wall panels Roof and wall panels, often made of galvanised or coated steel, protect the structure from environmental elements. Panels are available in varying thicknesses and profiles, offering options for thermal insulation and soundproofing.4. Fastening and Joining SystemsHigh-strength bolts and nuts provide secure connections between components. Pre-drilled holes enhance accuracy and speed during assembly.5. Foundation Requirements Because of their optimised design, pre-engineered buildings (PEBs) need lighter foundations than traditional buildings. This results in reduced material and labour costs.Accessories Accessories like ridge ventilators, louvres, and sliding or roll-up doors can be integrated seamlessly into the design.Applications in industry1. Manufacturing plants PEBs accommodate assembly lines, heavy equipment, and industrial robots with layouts tailored for efficiency. Custom designs allow for the integration of mezzanine floors or cranes for material handling. 2. Warehousing and distribution centres Wide-span designs maximise storage capacity, with the option to incorporate automated storage and retrieval systems (ASRS).3. Processing units PEBs house food processing lines, chemical plants, and textile mills with provisions for safety measures like fire-resistant materials and temperature-controlled zones.
4. Service and repair workshops PEBs are used for automotive repair centres and engineering workshops, where heavy-duty operations and flexible layouts are critical.5. Energy and utility sectors With modular, adaptable designs, PEBs support solar power plants, wind turbine installations, and utility centres.
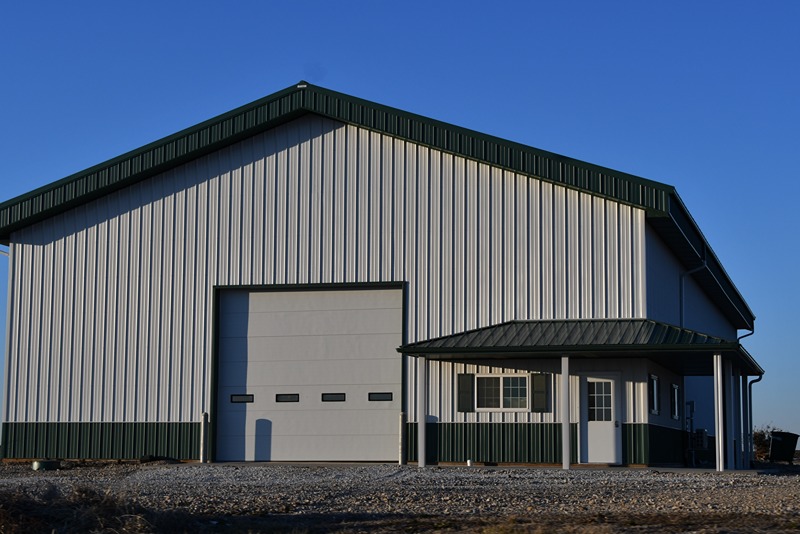
Why steel is integral to PEBs1. Strength-to-weight ratio Steel provides high structural strength while keeping the building lightweight, allowing for larger spans and reducing foundation requirements.2. Corrosion resistance Galvanised and coated steel components resist rust and environmental wear, ensuring long-term durability in industrial settings.3. Ease of fabrication and assembly Steel’s malleability allows for precision fabrication, ensuring a tight fit during assembly. Pre-drilled holes and standardised components simplify the construction process.4. Recyclability Steel is fully recyclable, aligns with sustainable construction practices, and reduces waste. Advantages of PEB industrial sheds and factory buildings1. Reduced lifecycle costs PEBs minimise maintenance costs with their durable materials and low-waste design.2. Scalability and flexibility Modular designs allow for easy expansion or modification as business needs grow.3. Regulatory compliance PEBs meet industrial safety standards, including fire resistance and load-bearing requirements.4. Customised layouts PEBs can incorporate advanced features like integrated cranes, mezzanine floors, and insulation systems tailored to operational needs.
Buy online
Mild SteelStainless SteelStructural SteelTMTCementJSW One MSME
About usBlogsSitemapJSW One TMTPolicy
Terms & conditionsPrivacy policyReturn policy